S/4 Conversion
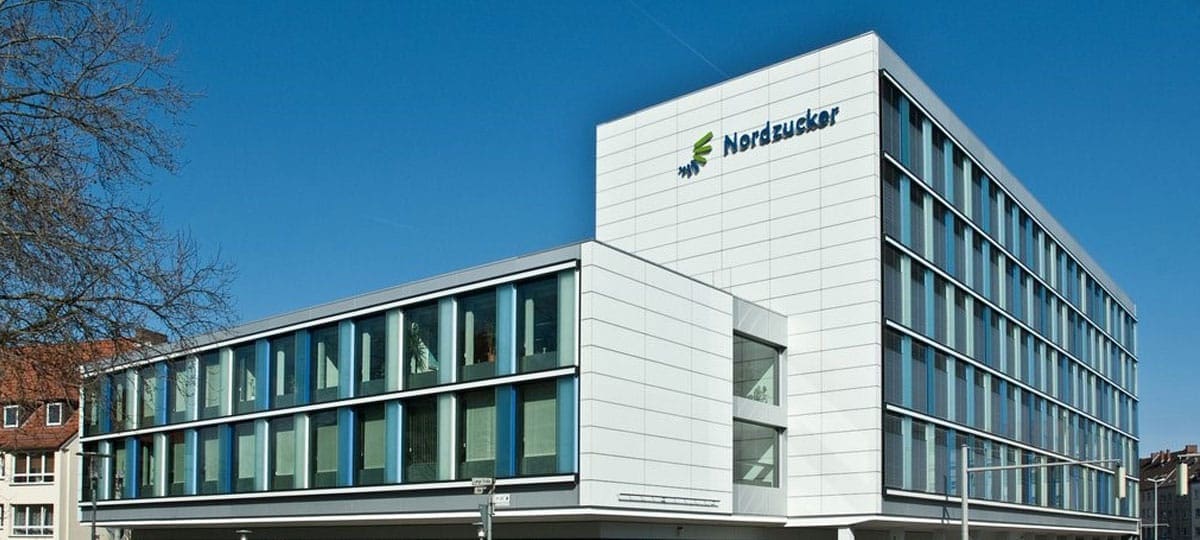
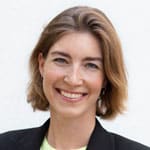
Nordzucker transforms ERP productive system
Nordzucker controls its business processes via SAP. In order for the company, which is headquartered in Braunschweig, Germany, to continue to grow and expand its core competencies, it relies on stable business processes ranging from planning, procurement and logistics to finance and controlling. "We operate in eight countries with this system, have around 50 active company codes, 16 production sites and 1500 users on the productive system," says Michael Jansen, Head of IT at Nordzucker.Â
Two years ago, the company decided to convert the old ECC to S/4. The introduction of S/4 formed the essential basis for Nordzucker's digitization strategy. Since the business processes at Nordzucker were already well mapped in the SAP system, the focus was primarily on a technical conversion, i.e., the functional deltas between the legacy system (ERP/ECC 6.0) and S/4 Hana.
Complex transformation approach
In the case, processes usable under S/4 are adopted and only changed in selected areas. In order to create stable operation and the basis for further projects after the implementation project, internal resources in IT and the specialist department were heavily involved in the project work. For support, especially with new topics such as condition contract management and credit management, Nordzucker called in a competent and experienced implementation partner.
The biggest challenge in the project was the very special framework conditions. For example, Nordzucker used a module called Agricultural Contract Management (ACM) in the old system that was developed specifically for the industry and could not be converted in this form. At the same time, customizing and in-house developments had to be retained for the most part. "In parallel with the project, it was also our ambition to maintain our legacy system landscape so that we would not have a hard freeze over the entire project period," explains Jansen. Therefore, a more complex transformation approach was required: a mix of brownfield and greenfield, and then data migration in addition to conversion. The individual approach was developed together with experts from T.Con before the start of the project and further refined during the initial project phases.
The current 3-tier landscape with development, test and production systems remained in place for the time being. It was supplemented by an ECC system with the ACM removed. The setup was supplemented by another system, the migration system. Here, trials and experiments were carried out. In addition to the technical implementation, the implementation of major simplifications, such as the introduction of condition contract management and the business partners, also had to be taken into account. Furthermore, an initial starter kit of new functions was also planned, including the first Fiori apps, RFQ management and CO-MA, which is based on the new Universal Journal.
The essential basis for the project's success was, above all, a project phase plan that was precisely tailored to the particular transformation of the system landscape. The first phase included scoping, fit-gap workshops, and evaluation of the potential of the Fiori UI. This provided the project team with a list of issues to be addressed as part of the rest of the project. Phase two started a little later, but was carried out in parallel in large parts. Thus, the project team converted the Green ECC and started with the custom code adaptation.
The challenge of data migration
In the third project phase, the build phase, the project team dealt with the implementation of the simplifications and other new functions as well as with the data migration, which proved to be the central effort driver. "The extensive custom code adaptation and also the data migration challenges were managed together with the competent developers on the part of T.Con," reports Jansen. "Especially in difficult situations, it was always possible to rely on a solution from colleagues - especially when the SAP migration cockpit that was mainly used only provided very incomplete solutions." In close cooperation directly with SAP and with the help of the technically very experienced colleagues, the SAP migration cockpit could then be used as the most important tool for the data migration.
Cut-over and go-live
These phases were followed by the test phase, cut-over and go-live. These took place as planned and were very successful from Nordzucker's point of view. "There was no disruption to business-critical processes, the planned downtime before the go-live was adhered to, and the migration of inventories was 100 percent error-free," says Jansen. "The reduction in delivery quantities planned to minimize risk was reversed within a very short time, and during the entire Hypercare phase the number of defects remained within an extremely manageable range."
With the smooth, error-free migration to S/4, important project goals were achieved: concrete improvements in the area of reporting, implementation of important simplifications such as condition contract management, and initial experience with the new Fiori UI. But above all, the establishment of a new technological basis that provides a foundation for further innovations. In the end, T.Con was able to deliver what the first contact had promised. Nordzucker will continue the cooperation in S/4 follow-up projects, but also in other areas such as SAP SuccessFactors and SAP BW.