Route processes
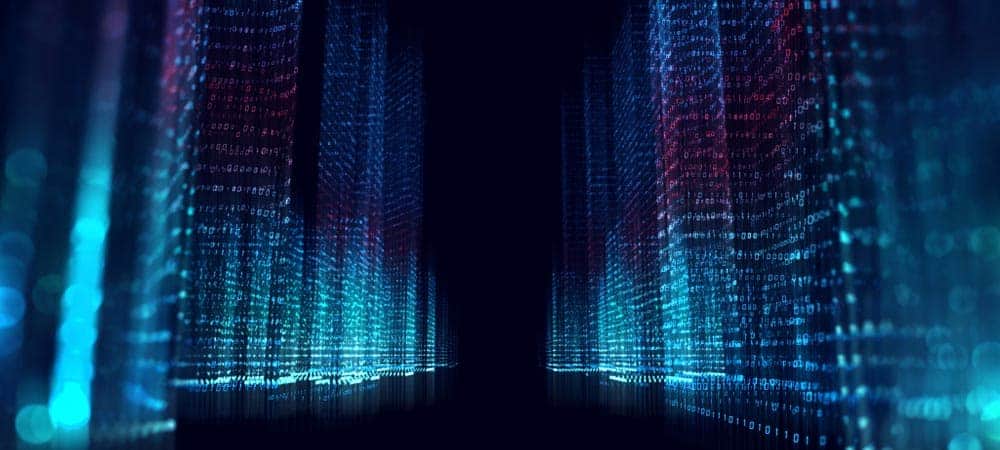
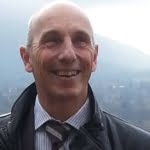
With its Digital Transformation 2025 strategy, Telegärtner, an existing SAP customer, has set the course for continued economic success and expansion in the future. A core objective of the transformation is to significantly increase the digitization and automation of processes in order to place the customer even more at the center of the company's activities.
The core competence of the owner-managed Telegärtner Group, whose heart is Telegärtner Karl Gärtner in Steinenbronn, is the development and production of innovative and high-quality coaxial connectors. The family-owned company is one of the market leaders in this field and produces several million coaxial connectors per year - from miniature connectors for electronic devices to precision connectors for laboratory measuring equipment. With almost 700 employees at eleven locations worldwide, the Telegärtner Group is also one of the top addresses in the field of cable assembly as well as network components, plastic injection moulded parts and industrial electronics.
Harmonized master data
The prerequisites for this are uniform systems and harmonized master data, both within the group and with the customer. With the introduction of S/4 Hana (version 1909) at Telegärtner, a foundation stone has been laid for the harmonization of the IT landscape. With this modern, integrated ERP suite, which uses the latest SAP technology and replaces an aging multi-ERP landscape, the data from all Telegärtner companies will be consolidated and managed centrally in the future. The roll-out to the other companies in Germany (Telegärtner Gerätebau and Telegärtner Kunststofftechnik), Great Britain, Slovakia as well as in the USA and Japan is to take place gradually.
"With S/4 Hana, we are in a position to actively shape the digital transformation. But even in this ERP suite, process gaps are opening up, for example in route processing with our sister company Telegärtner Gerätebau. We close these by using SAP-based add-ons," says Alexander Voss, Head of IT at Telegärtner.
In the standard modification-free
In the case of third-party order processing, this is handled by the Speedi-Strecke solution from WSW-Software, which extends the standard S/4 functions without modification. The benefits of the solution became apparent shortly after it went live. The sister company's route processes are now completely integrated and IT-supported and thus handled very efficiently, transparently and securely in S/4.
"We carry out drop shipment business with individual customer orders instead of SAP delivery schedules and process between 70 and 100 orders every day, so this is a business-critical factor," explains Alexander Voss. Processing with individual orders is necessary because Telegärtner Gerätebau assembles or manufactures the cables, cable systems and cable assemblies according to customer requirements. For this reason, there are a large number of product variants that Telegärtner manages in SAP S/4 in the classic variant configuration (LO-VC).
The realignment of the route process from order-related to delivery-related proved to be a major challenge during the implementation of Speedi-Strecke. Due to the changeover, the workflows of the end users also changed and they required additional training. The necessary know-how transfer was cascaded, first from the WSW software to Inhouse Consulting, which then carried out the internal training on its own. This effort was worthwhile, because the delivery-related invoicing of orders in Speedi-Strecke offers a number of advantages. When invoicing the orders, the software -automatically- takes into account the date of performance, which some customers insist on. In the old ERP system with its order-based invoicing, it still had to be added manually to each individual document and invoice. For the employees, this meant an additional workload of four to six hours per week. Now that this has been eliminated, they have more time for their -actual core tasks - a big plus.
Transparency and agility
All order progress in the draw frame process can also be tracked at any time, which was previously only possible with a great deal of effort. All it takes now is a few mouse clicks and the desired information is available. Thanks to this transparency, important questions - Where is the customer order at the moment? When can it be invoiced? What about the delivery bill? - can be answered quickly and satisfactorily.
Alexander Voss assesses the use of the Speedi solution as thoroughly positive: "We use it to handle the route processes with our sister company in a completely integrated, end-to-end manner and thus efficiently and quickly in S/4 Hana." The smooth interaction of Speedi and the ERP suite is ensured by a special transition package from WSW-Software, so that investment security is guaranteed.