Team Spirit Beats Algorithms
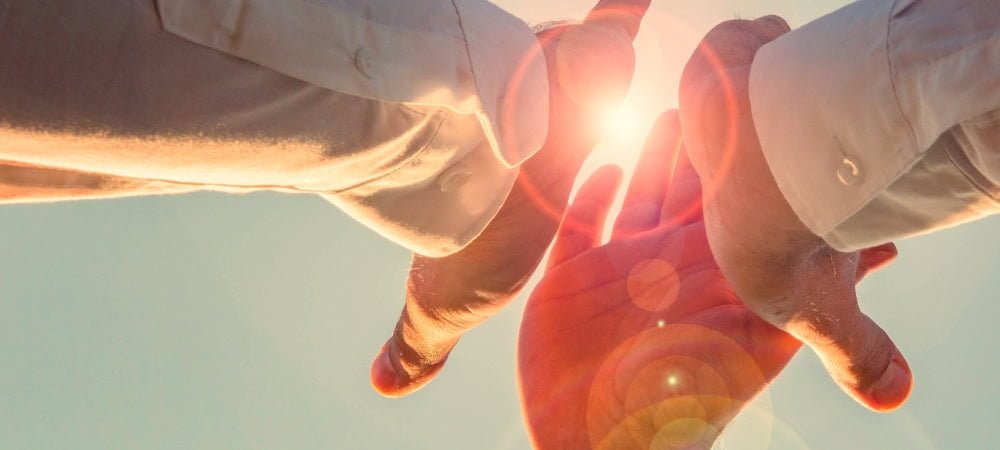

Successful retailers are distinguished by a sophisticated strategy, meticulous planning, and precise implementation. Regardless of whether they are considering a nearshore rather than an offshore retail supply chain network, they are able to weigh the advantages and disadvantages in a way that leads to optimal decision-making.
Supply chain potential
The optimal functioning of retail supply chains hinges on seamless interaction. For retail supply chains to reach their full potential, all functions must be aligned towards a common goal. When a retailer makes a new product purchase, this is done in close coordination with sales planning, order fulfillment, and order management. If planning, operations, logistics, warehousing, and IT focus exclusively on their own departmental KPIs, it will significantly restrict cross-functional collaboration and lead to information gaps and an increased workload.
There is much more to the retail industry than simply maintaining a well-stocked shelf. Modern retail supply chains are comprised of a vast network of suppliers, logistics providers, and numerous invaluable contributors who perform essential functions in warehouses, transportation, and stores. They are the unsung heroes of the supply chain. Rainer Schulz, Managing Director of Sysmat, outlines the steps required to optimize internal material flow: "An increasing number of factors are affecting the daily operations of companies across all industries, making it challenging to navigate. Consequently, those in charge are required to closely examine the factors within their control and implement necessary adjustments. One such area is that of internal material flow. Optimizing the internal material flow can help reduce production costs, shorten throughput times, and improve overall product quality. To design the processes accordingly and ensure successful implementation, a number of steps must be taken.”
Analysis and documentation
The initial step is to gain an overview of the current situation. A comprehensive analysis of all internal processes is an effective method for achieving this. This is the only way for those responsible to gain a comprehensive understanding of all relevant positions and ensure that all necessary information is included in the assessment. It is of the utmost importance to ensure that all relevant information is accurately documented, as this will provide a solid foundation for future decisions. By mapping out all processes, companies can implement this initial phase in a targeted manner.
The detailed analysis provides a foundation for the second step. In addition to identifying potential bottlenecks in the inventory, those responsible for the process examine the various stages to identify any weak points or potential sources of error that could disrupt the material flow. In this context, a lack of organization can result in missed delivery deadlines and goods not arriving at their destination or to the customer on time. It is essential to maintain a high degree of transparency in order to identify these causes.
Cost management
Many managers are often hesitant to modernize, concerned that it may disrupt production. Another ongoing challenge is the cost involved. However, updating the system reduces expenditure by ensuring that the supply chain is as fully utilized as possible. A graphical material flow computer, however, offers a different solution. The objective is to maintain low costs throughout the implementation process. Flexible interfaces and comprehensive testing capabilities allow for up to 70 percent time savings during implementation, positively impacting the bottom line. A three-weekend commissioning period is sufficient, with project managers closely monitoring the integration of all systems. Once testing is complete and deemed successful, the new environment is ready for use without any loss of production.