Digital Factory
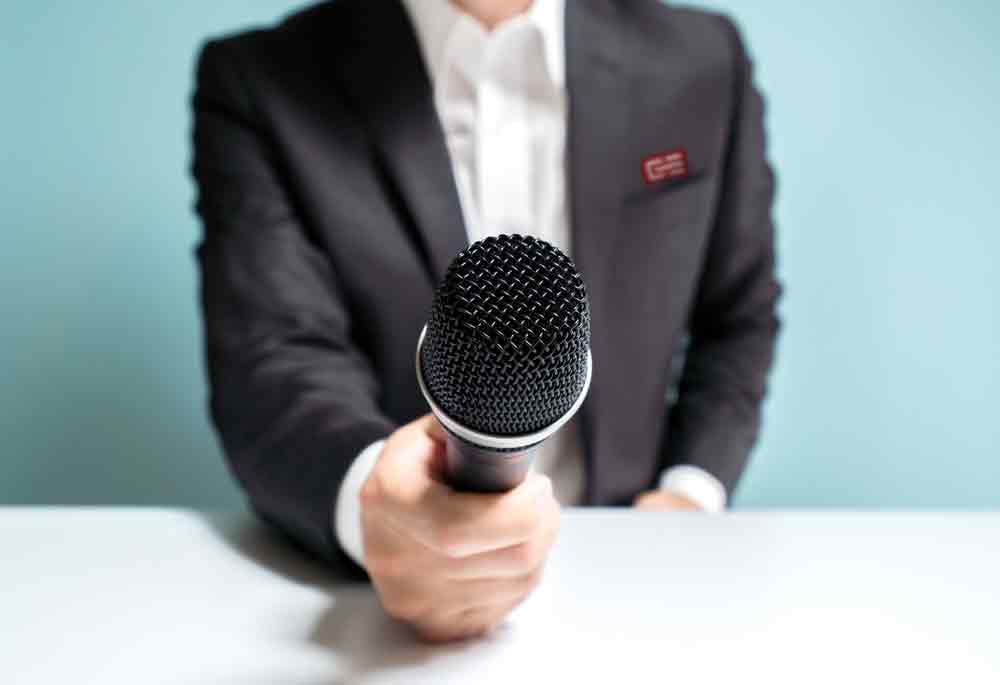
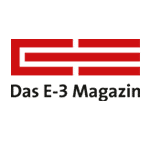
Digitization projects often come to a standstill due to a lack of acceptance among the workforce. Have you had similar experiences in your projects and do you also offer change management support in advance here?
Thomas Gard: The effects on existing workflows must be taken into account. It makes sense to involve employees directly in order to jointly identify potential for improvement on the store floor.
This starts with an analysis of the employees' suggestions for improvement and then moves on to a joint definition of the dialogs for redesigning the workplaces.
With this approach, change management begins with the involvement of employees at the earliest possible stage. This gives employees the opportunity to help shape their new workplace.
In our experience, this can increase acceptance in the project.
Where do you see the impact?
Gard: Orbis' strategy is, among other things, to improve the presentation of information and thus shift decisions to the operational process level - to the point of origin.
With this strategy, employees are upgraded because they are more involved, for example, in troubleshooting. Information is pushed.
This relieves employees of the "duty to fetch" information. In essence, dialogs from supervisors such as "Have you already checked status XY on the machine today?" no longer take place.
Digitization can thus help to make work easier and more valuable. In addition, uniform or monotonous activities can be reduced through comprehensive networking and digitization of production.
IT is only one aspect of Industrie 4.0; there is also know-how in mechanical engineering, sensor technology, embedded systems and automation. What technical and personnel requirements must a potential customer have in order to start a smart factory project?
Frank Wilhelm: In addition to IT know-how, in-depth manufacturing and plant know-how is a crucial prerequisite. As a rule, these prerequisites are already in place in the companies.
The implementation of such a project implies the integration of the various vertical and horizontal specialist areas. This affects the vertical IT structures of the complete automation pyramid from the ERP to the control level and requires a certain willingness and openness to deal with this new topic without reservation.
And horizontally?
Wilhelm: Horizontally, at the process level, all areas are affected, from design, logistics and production to quality assurance, maintenance, service and personnel.
In particular, the interaction between process IT and production IT must be ensured, as the SAP processes must be integrated into an exchange of information with the systems and devices on the store floor.
The Orbis software serves as a "gateway" between the process and technical worlds. It translates the language of SAP processes into the technical language of machines and systems and vice versa. The result is the desired bidirectional exchange within the Smart Factory.
What role does standardization play in the Smart Factory? And which standards does Orbis use?
Wilhelm: Standardization is an essential success factor for implementing a smart factory. Our experience shows that for successful project implementation, the three core areas of system infrastructure and system levels, the technical connection of the end devices (network connectivity), and the process flows and integration (technicality) must be standardized on a customer-specific basis.
And what is missing?
Wilhelm: In particular, a standardized interface to all machines would be desirable. The heterogeneity of technical end devices and manufacturers is a major hurdle.
For this reason, Orbis has focused on standardizing information for simple and fast process integration into the SAP systems. This way, all relevant information for process control flows together there.
Machines and devices can thus be connected in a short time, and the maintenance effort can also be significantly reduced. Orbis supports today's common industrial protocols as well as the OPC connection.
With MPS, Orbis has created a solution to automate the entire process chain end-to-end. To what extent can MPS be customized to meet individual needs? For which industries and types of production?
Wilhelm: Orbis adapts the manufacturer-specific machine interfaces and, with regard to integration into the business processes, uses a standardized object interface that enables direct and industry-standard communication.
Orbis Multi-Process Suite, MPS, is the basis for a simple, secure and fast implementation of Industry 4.0 processes in the SAP world. Furthermore, individualization and needs-based implementation is possible, based on the modular approach of graphical process modeling.
In principle, there is no restriction to specific industries or manufacturing methods. MPS consists of several modules. On the one hand, the technical connection of the machines, devices and systems is supported via the Orbis Multi-Process Interface.
Another essential component is the Orbis Multi-Process Viewer. This allows information to be visualized and dialogs to be enabled on all common devices.
Our solutions, integrated with SAP, open a smart path to the factory of the future.