SAP maintenance mobile
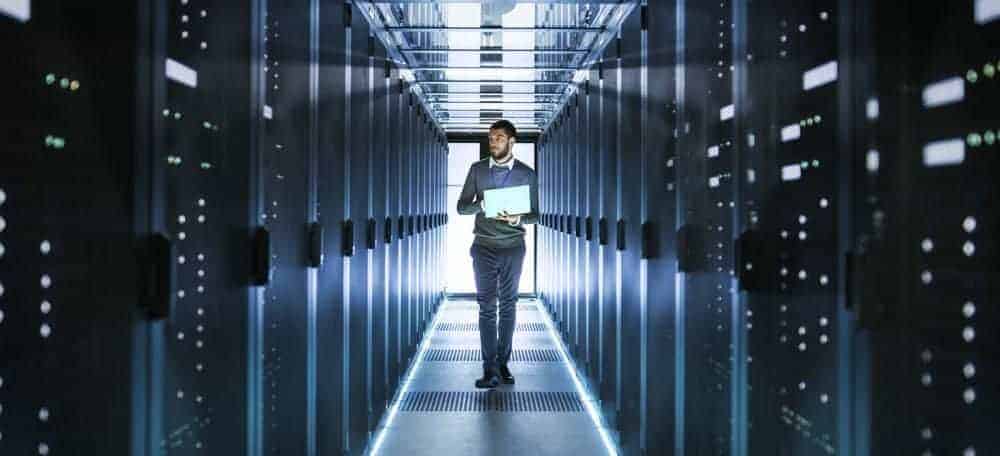
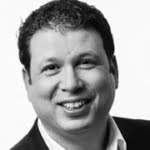
The use of smartphones and tablets, which are in direct communication with the SAP EAM module, guarantees end-to-end process flows without media breaks and interface losses.
The gain in efficiency and convenience becomes clear when looking at an everyday use case using a mobile solution in maintenance:
Consider a limited scenario in which a production worker reports defective equipment for maintenance action.
Since the employee has a mobile device, he or she can pick up the technical space and equipment by simply scanning the barcode or using RFID.
Photos can also be transmitted in this way, on which the defective area is made clear with handwritten markings. This eliminates transmission errors when writing on the paper form.
The information is available to the team leader in SAP ERP without any loss of time. Incorrect recording is virtually eliminated by the scanning process and the use of optional damage codes or text modules.
The latter can schedule the order with little effort, as the data is already in SAP and he can easily gain insight into the availability or delivery time of any spare parts that may be required.
Once the order has been placed, the maintenance technician also receives all the necessary technical documentation, checklists and the history of the defective equipment. Everything is centrally stored on his mobile device.
The maintenance technician scans the barcode on the defective device and automatically reports the start time of the repair work. If necessary, he is guided step by step through the activities to be performed via the documentation synchronized to the device.
For the feedback of the findings and the completed work, the maintenance staff can use predefined text modules. However, free text input is still available.
In addition to the pure time savings, this also enables standardized reporting. Since the results of all checklists are available in tables in SAP, evaluations and reports can be created automatically in the system.
The checklists to be completed (primarily for S&E orders) are also available on the mobile device. This eliminates the need for paperwork and the risk of transmission errors.
The maintainer can document his completed work by digital signature, and a digital approval process can be implemented.
The advantages include a reduction in administrative activities, optimization of data quality, increased evaluation capability, greater process reliability and time savings.
Must: Flexible solution
It is not sufficient if a mobile application fulfills the process requirements at the time of initial operation, but only allows future adaptations at great cost due to a static development platform.
Before a company decides on a pilot project with a provider, the question of the flexible, cost-effective expandability of the solution in the event of changes in requirements and processes should be clarified.
Once the initial investment has been made, it becomes more difficult to change platforms. However, there is not only the question of the flexibility of the development platform offered, but also whether it can be made available to the customer.
The use of different mobile devices within an application is mandatory so that the user can be provided with the optimal device according to his activities.
Offline, but properly
Experience shows that there are hardly any customers for whom an exclusively online scenario is sufficient. The term offline must be questioned in detail.
What is essential is a sophisticated synchronization concept and whether this extends into the document management system and SAP. Over the years, the preference of the end device selection and mobile operating systems in the company can shift.
It is important to ensure that the change of mobile device or even mobile operating system does not result in high follow-up costs.
The area of conflict between business requirements, SAP expertise and experience in the development of mobile applications is complex.
It is important to select a vendor that has both experience in programming mobile applications and in-depth knowledge of maintenance operations and processes.
Many companies have recognized the benefits of digitization in maintenance solutions. The reduction of administrative activities and availability of all relevant information leads to higher employee satisfaction in the area of maintenance. The increased efficiency leads to cost benefits and improved data quality in maintenance.