Production and detailed planning in the S/4 cycle
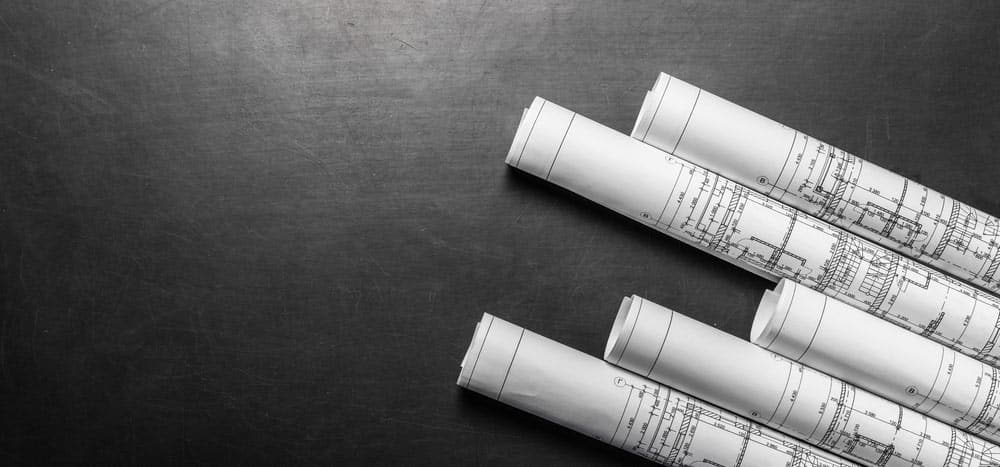
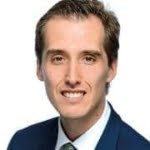
The latest feature of S/4 for SCM is Production Planning & Detailed Scheduling (PP/DS). The module, which already included the SAP SCM solution, has now been integrated into S/4 Hana in the latest Release 1610.
The PP/DS module adds some new functionalities to the previous production planning: For example, extended finite planning is now available, which allows capacities to be planned automatically and granularly instead of manually and rudimentarily as before.
Furthermore, users can access more tools for detailed production planning. These optimize capacities automatically or interactively, taking into account factors such as orders and workstations, resulting in optimal utilization of time and resources and reduced costs.
In addition to capacity planning, S/4 now has other tools that were previously only available in the SCM systems. These include planning boards as well as alert monitoring and the context overview, which show the requirements and capacity situation across all BOM levels at a glance.
Some of the new tools can also be used with the new UI5 or Fiori interface and used as mobile apps, which greatly improves usability.
The new material planning run, MRP Live, which achieves results much faster, is based on S/4 technology. Because Hana can be combined with the PP/DS module, this allows both demand planning and capacity planning to be carried out.
Thanks to MRP Live, planning can be done in one system instead of several, which is why this module is also called OneMRP. MRP Live makes it possible, for example, for finished products to be planned via PP/DS, but unfinished parts via MRP.
This is how the transformation goes
The new SAP Business Suite and Hana can be evaluated via a test implementation. For this purpose, test scenarios are set up on a converted S/4 system and various processes are run through, including, for example, setup optimization with production resources/tools, the setup of an availability check with AATP (advanced available to promise), model-mix planning from the automotive industry, and material staging with integration in EWM (Extended Warehouse Management).
The transformation process is an important criterion about which the technical evaluation provides information: In order to take full advantage of all functionalities, it was previously necessary to connect an SCM system to the ERP system.
The question now is how best to migrate data from an already connected SCM system to the PP/DS module now integrated in S/4 Hana. In addition, existing customer programs must be adapted for S/4 Hana.
Such an upgrade or migration can be carried out in five steps. First, the initial scenario is defined; one of the relevant questions is whether SCM is already connected to ERP.
The data model and scope are then determined, as is the amount of master and transaction data that needs to be migrated. This is followed by the actual conversion, followed by the technical configuration of the S/4 system and the connection of the UI5 or Fiori interfaces.
Finally, the functionalities of old and new processes are analyzed and compared according to SAP's Simplification List in order to derive necessary measures.
Master and transaction data
The upgrade affects master data such as work centers and material masters, among other things. In the case of the material master, some existing parameters, for example in repetitive manufacturing, are omitted, but PP/DS adds a new view with parameters for extended planning.
In addition, the source determination for master and transaction data changes significantly. For example, production versions become mandatory for in-house production - whereas for external procurement, the source lists are no longer relevant.
Setting the appropriate parameters in the master data (material master & work center) activates advanced planning in PP/DS. Since no external system such as an SCM needs to be connected anymore, complicated interfaces such as the Core Interface (CIF) are greatly simplified by eliminating almost all integration models.
S/4 makes dynamic inventory calculation possible. Inventory is no longer stored in tables or databases. Instead, it is calculated automatically at runtime by the new data management for material documents, such as goods receipts and issues.
The LiveCache of a formerly connected SCM system, where order data was previously stored, can be imported into the new system to receive the transaction data in S/4 Hana.
The challenge in migration is to keep the downtime window and thus the business interruption as small as possible. A multi-stage approach is ideal for this.
First, the existing SAP landscape is analyzed and the scenario is determined as to how the conversion can be carried out. Then the test implementations and migrations take place to determine how the go-live migration will proceed. It is also important that tables and programs of the customer are included. This is the final result of the minimal downtime approach.
System extensions
There are three options for system expansion: In the brownfield approach, the existing ERP system is converted directly. The greenfield approach involves setting up a completely new S/4 system and implementing it from scratch.
It is also possible to transform a system landscape, i.e., to integrate several ERP systems into one S/4. The SAP Migration Cockpit and SAP Landscape Transformation tools are available for support.
If the SCM system is to be preserved because it has functionalities that are not available in PP/DS, there are similar options for preserving this landscape and connecting it to S/4: Either this is done by converting the ERP directly and then migrating the data from the PP/DS of the SCM system to the equivalent on the S/4 system.
Or through a two-step upgrade, in which the ERP system is upgraded to an ERP on Hana with subsequent conversion and migration.
It is also possible to first upgrade the ERP to an ERP on Hana and then install the APO on ERP add-on. The data is then migrated from SCM to APO and then the conversion to the S/4 system takes place.
If there are customer developments on the SCM system that refer to stored data in the SCM system, a new mapping must be performed so that the data on the S/4 system can be read by the new PP/DS component.
After the master data change, it must also be checked whether the programs continue to function. Interfaces from the SCM to the ERP system are no longer needed and must be replaced by direct data procurement.
Various tools check which codings in customer programs are obsolete or need to be changed currently or in the future.