The digital supply chain has many hurdles to overcome
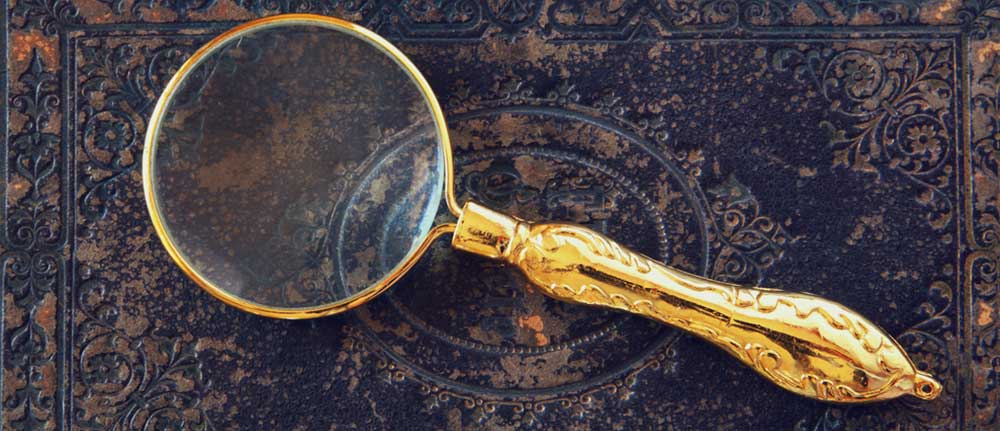
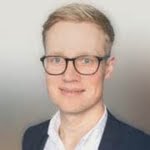
The Internet of Things is changing the possibilities of logistics from the ground up: Until now, the location of a good has only been determined on the basis of assumptions, and expensive and cumbersome RFID solutions have done little to change this.
The real-time tracking and localization of pallets, containers and trucks made possible by IoT is the basis on which many processes - including those within plant logistics - can now be automated.
Sensor and camera technology also make a contribution to this. For example, a truck used for refrigerated transport can itself use sensors to report when the prescribed refrigeration temperature has been reached, thereby automatically triggering the loading process. Onboard units in trucks take into account the weather, tank level and traffic situation to tell production exactly whether material will arrive on time.
AI as low-cost cognitive services
Camera systems use OCR text recognition to capture container numbers or truck license plates so that the gate can open automatically for notified vehicles.
Such solutions, which previously existed only in special systems, are now available with AI (artificial intelligence) technologies as inexpensive cognitive services. But so far, the automation potential created by IoT has only been used selectively in logistics.
One of the biggest road blocks is that existing systems are not designed for hybrid business models. Track & Trace generates a lot of data outside the SAP systems. Early bird projects show that true digital supply chains can only be created by combining SAP and non-SAP functions in a meaningful way.
Indirect use and future security
IoT data, which also comes from external sources such as sensors, points to an important construction site in the SAP environment: The need to set up hybrid business models in the context of collaborative processes, in which data moves through different ERP systems, is constantly increasing.
Technologically, SAP is able to support such modern architectures with S/4 Hana. However, for many users, the question of how to create a model that is future-proof and cost-effective with the indirect use of SAP is still open.
In addition, the complex hardware integration associated with IoT is chronically underestimated. Today, logistics companies have to set up their internal IT departments in such a way that, in addition to core planning systems, they also have to deal with the processing of hardware data from a wide variety of sensors and camera systems.
Many things are also changing in plant logistics: Technologically, the ERP system must be able to automatically trigger process steps based on these new data flows between companies.
However, this means that we are moving away from purely transactional systems to process-oriented systems. Basic functions are available in Transportation and Warehouse Management and the SAP Cloud Platform, but not in the simplicity that customers need today.
Anyone who currently wants to implement such integrated solutions must either integrate more than a handful of SAP solutions or rely on alternative offerings such as the Leogistics Digital Supply Chain platform, which holistically synchronizes all modes of transport such as truck, rail or ship across any system.
Logistics cost factor
Logistics costs can account for up to 30 percent of manufacturing costs. In site logistics, more effective processes are therefore increasingly decisive for competitiveness.
There is also potential for optimization, for example, in classic time window management, which is used for scheduling truck loading and unloading. Solutions such as the Supply Chain Control Tower use telematics integration and smart apps to flexibly direct loading so that other trucks are brought forward if a scheduled vehicle is late.
Only the beginning
With all these IoT topics that are already technologically feasible, the industry is still at the very beginning - processes are still heavily paper- and Excel-driven, and there are hardly any networked systems.
That is why standards must now be set as a matter of urgency. In addition, monetary incentives are needed to motivate logistics partners with their very different challenges to make digital efforts. Without process incentives in the form of remuneration and billing models, the digitization of logistics will remain a patchwork.