Digital competence: Preparing digestible portions
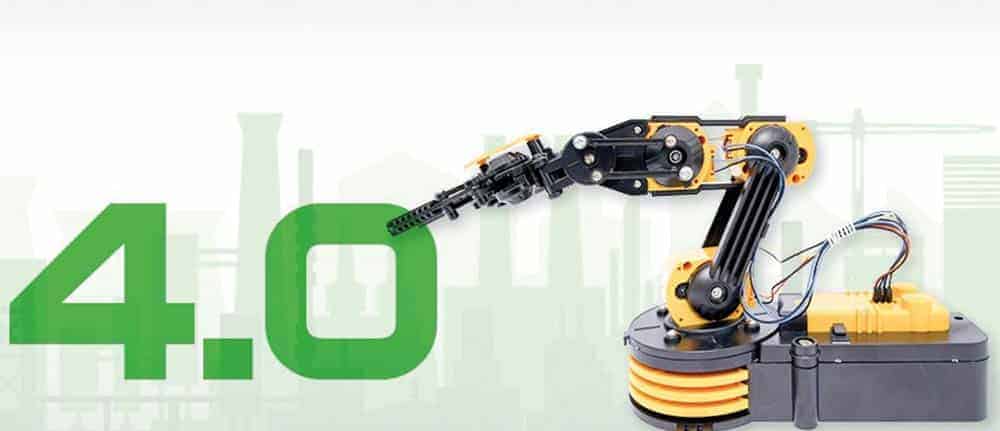
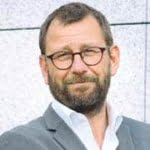
So far, so good - but sometimes so far, so unclear when it comes to implementation, as our experience shows. Many companies know that they need to do something, and many already have a digitalization strategy.
But sometimes there is a lack of clear guidelines and prioritization when it comes to getting specific: Where do I start? What milestones do I set? How long should sub-projects take?
If you don't have the answers to these questions or a competent partner at your side, you will get bogged down faster than the CEO can say "budget approved". Companies can make 2019 their year of success in terms of digital transformation if they follow just a few basic procedures.
Three pillars, three steps
It is not uncommon for those responsible to have a mammoth program ahead of them: the entire product lifecycle management has to be turned upside down, real-time data from production through to logistics and service processes has to be recorded and everything has to be interlinked across as many platforms as possible.
Everything is feasible - the prerequisite is digital continuity in the product development process, which we summarize under the keyword smartPLM.
Why this continuity is the measure of all things can be easily illustrated with an example: If Amazon guarantees delivery within 24 hours and has digitally optimized all but one of the logistical process steps, this is not enough.
Then the order is at the point where a media break occurs, two days before it is forwarded. The chain is therefore only as strong as the weakest link. However, such digital continuity also means greater criticality of system availability and often also an increase in complexity.
This is why reference models, for example, are crucial for recognizing dependencies in data structures and sub-processes and for ensuring trouble-free operation.
Digital transformation is based on the three pillars of "virtual product", "digital process" and "autonomous production". The aim is to build these three pillars gradually rather than all at once. The recipe for success is to break down the digital transformation of the company into digestible portions. Three steps are recommended:
Create a digitalization strategy (derived from the corporate strategy) Define milestones Set up sub-projects While these points may seem obvious or even banal at first glance, we see time and again how transformation projects fail when such a structure is missing.
Many companies already have a digitalization strategy, but some simply let the major "digitalization" project run for three years. If you take this approach and want to see the benefits after the time has elapsed, you are opening the door to a waste of budget and time as well as overworking the team.
Instead, it is important to focus on the aforementioned sub-projects, which should be coherent and distinct from the other units, pursue a clear objective and adhere to typical planning parameters such as budget and time.
It is essential that a sub-project goes live quickly and generates tangible benefits - and therefore lasts no longer than three to six months. Longer periods make it more difficult to maintain team and management motivation, which is a factor that should not be neglected in any change project!
In this context, it also makes sense not to think in terms of functional units and departments, but in terms of the process, and to allow a great deal of freedom in the projects in order to not only allow new ideas, but also to promote them.
Opportunity for SMEs
To qualify this recommendation somewhat - this approach corresponds to a top-down approach and leads to success in most cases. However, depending on the circumstances at the company, a bottom-up approach or a mixture of both can also lead to the desired result.
This means that sometimes the practical use of digitalization in a limited area gives rise to ideas or approaches for optimizing business processes on a larger scale.
This happens regularly when we start with our solution for process control in a sub-area such as design approval. The obvious advantages of process-driven object handling very quickly generate ideas for use in other sub-processes. In this case, it is therefore worth pursuing a dual strategy and combining both approaches.
Incidentally, the digital transformation of companies is the hour of SMEs, and not just because cloud-enabled solutions often fit their requirements perfectly.
In contrast to large corporations, there is also a better chance of bringing together decision-makers from all areas. This allows end-to-end business processes to be rethought and digitized together, starting with the customer.
This is demonstrated by a recent example in which we as Cenit supported a medium-sized, family-run mechanical engineering company. After just a few very efficient meetings with the management and division heads, we were on the ball:
The relevance of breaks in digital continuity has increased massively in recent years and will continue to increase rapidly if the individualization of machines demanded by customers is reflected in the diversity of variants and frequency of change - as a consequence, central value creation processes are becoming increasingly difficult to control and manage.
Together, the weak points were quickly identified, fields of action derived from them and an obvious solution architecture developed. From then on, it was only a small step to project planning and commissioning.
This meant that the customer was literally "ready to grow!", i.e. ready for an expandable digitalization strategy. The prerequisite for this parade route is that the management is willing to actively participate not only in the project foundation, but also in the project itself in appropriate committees.
After all, digitalization is a matter for the boss, and real process optimization always brings significant change and therefore also fears and uncertainties. Professional change management must therefore be an integral part of any project planning.
How standard can it be?
When we help customers with their digital transformation, the question of the degree of IT standardization almost always arises. Our recommendation is to support 80 percent of core processes with standards and rely on customized software for a maximum of 20 percent - and to consciously accept the disadvantages that this 20 percent entails.
This consideration is about implementation speed, robustness and update capability. Those responsible should always bear in mind that the use of cloud applications will massively reinforce the trend towards standardization.
The large platform providers protect their "digital core" and provide their software in ever shorter cycles. In a 24-hour deployment cycle of the provider, classic, month-long update preparations, as with individually developed solutions, are simply impossible.
Media discontinuities are still most tolerable if the number of variants of a product is not too high - but the trend is towards more complex products.
Conclusion
Platform economy pays off at this point because you can scale. Based on the experience of more than 200 projects in various areas of the manufacturing industry, we have developed a holistic approach from project methodology to system packaging and configuration.
A preconfigured solution based on the SAP or 3D Experience platform is particularly suitable for those who want to achieve results quickly - it contains all typical PDM functionalities, supports the core processes in engineering and prepares the "hand-over to production", for example, through properly controlled release and change management.
Digitalization will become even more of a competitive factor in 2019 - in the confrontation with similar as well as new market competitors that were born in the digital world.
While it is still possible to position oneself against competitors of the same type with classic virtues such as efficiency, cost reduction and shorter lead times, the situation is different with new competitors:
What good would it have done Nokia, for example, against Apple to produce its cell phones only half as expensively and twice as quickly? In other words, digitalization makes an important contribution to more creativity, foresight, a more flexible organization and further developed business models.
The ROI of digital transformation can then be calculated not only in the traditional way by increasing efficiency or reducing process costs, but also through increased or completely new sales that were not possible in the previous business model.
Now it's just a matter of getting started. We recommend a healthy mix of two typical approaches - with the American courage to get started and accept deviations as part of the learning curve, paired with the proven German diligence in thinking through goals and dependencies.