Paperless factory at ZF Friedrichshafen
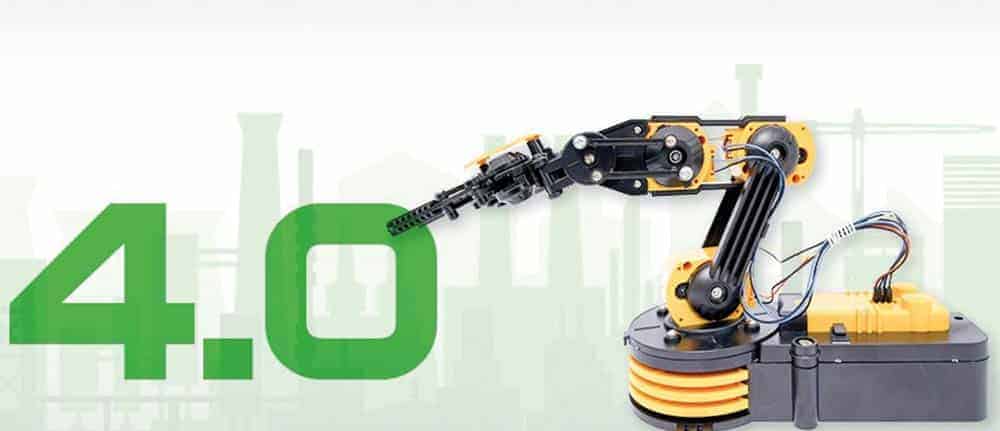
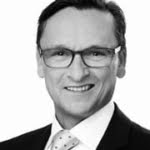
As a globally active technology group, ZF supplies systems for the mobility of passenger cars, commercial vehicles, and industrial technology and, with several hundred locations, is one of the world's leading companies in the field of driveline and chassis technology.
In the further development of ZF systems, one of the focal points is digital networking and automation. ZF is not only innovative with its own products, but also attaches great importance to the modernization of internal processes and procedures.
With the aim of improving collaboration on the machines through digital processes, a "Paperless Factory" project took place in 2019 in one of the Group's production halls. The use of paper in the production hall concerned was high because no mobile application was available that could be used to manage all the activities involved as well as the documentation.
Instead of being able to quickly access up-to-date information, employees had to rummage through folders as soon as machines were serviced or retooled. The use of paper forms represented a media disruption that was an additional source of errors.
Thus, the collaboration between operator team, foremen, quality assurance and support had to be put on a digital footing. Together with the implementation partner Camelot ITLab, a new system was introduced using modern technologies in the IIoT context, such as Hana, Fiori, SAP MII and mobile devices, which allows the digital control of work orders.
For the daily work of maintaining, inspecting and cleaning the machines, employees and supervisors receive targeted support through a central digital platform, for example, if certain maintenance work is to be carried out within the shift system at a predefined hourly frequency.
Via the platform, employees automatically receive notification of which actions are pending. Work is further facilitated by the quick retrieval of setup plans, which are stored in the system and guide employees in detail through the tasks to be performed.
If the employees have the right instructions quickly at hand, a lot of time can be saved, because the processes run differently depending on the machine or the material change. The foreman can also store his approval check digitally. This ensures that it is securely documented and archived.
The platform is easy and intuitive to use. Thanks to a stored authorization management, it can be ensured that each employee only sees the information that he or she actually needs. In addition, the ERP system was connected.
This also allows master data to be entered directly in the system, for example new lines, machines or materials. The platform offers the possibility to visualize the status of maintenance, inspection and cleaning work at any time. This has led to greater transparency and commitment.
The platform makes it easy to see which work steps have already been completed. At the same time, it is clear which employee is responsible for which work in which shift. The close involvement of over 50 stakeholders from different areas such as business, IT and operations was a particular challenge in this project. Nevertheless, consideration was necessary to ensure that the processes ultimately covered the requirements of all departments involved.
The project has resulted in a significant increase in efficiency, as the setup processes in the production hall concerned now take place much faster than before. At the same time, the administrative effort has been reduced.
The employees also find their way around the new system well, which leads to a high level of acceptance of the solution. The goal of the "Paperless Factory" has thus been achieved at ZF, the global technology leader, and further projects in this context are already being planned.