Transparent message bearer
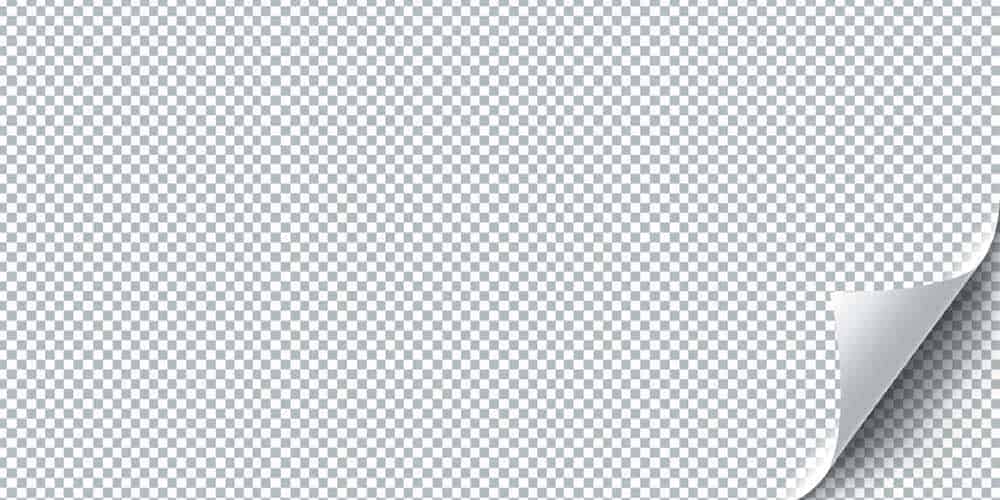
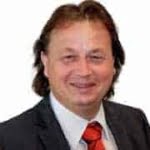
If errors occur during dispatch from SAP, it must be possible for the specialist department to correct them, ideally using user-friendly tools directly in SAP.
Was my EDI message delivered?
The department has to face such questions almost every day.
If EDI messages are sent, the department sees that its message was successfully sent from SAP, but here it is the same as with other "communication traps": "Said is not heard."
So how can the department see whether the message has actually been delivered to the partner?
Especially in the case of time-critical messages, the question is justified if, for contractual reasons, only a time window of 30 minutes is available after a message has been generated until it is successfully received by the partner or supplier.
The consequences of exceeding the time limit are often penalties (liquidated damages) for each late message, combined with a possible deterioration of the supplier rating, up to and including exclusion.
As a rule, it is technical errors that prevent the delivery of a message. These start already after the creation in SAP.
Even if the message appears to have been sent successfully according to the status in SAP, it is still possible that messages are still blocked in a queue.
However, after apparently successful dispatch from SAP, messages may also fail to reach their destination due to other factors:
If, for example, an EDI subsystem is interposed, there is a risk here that messages in the input channel of the EDI subsystem run into an error during a conversion or in the output channel. This stops the processing process.
In this case, of course, it is a further complication for the department to follow up.
A final very important aspect is not only the final receipt of the message by the partner or customer, but certainty that it has also been processed and posted there and that the information is thus transmitted to the sender.
It is precisely for these cases that no suitable tool is available to the specialist department as a self-service in the standard system.
The theoretical way of having the receipt or booking confirmed by telephone or e-mail does not seem practicable.
It is true that there are technical specialists who can provide support or eliminate the causes of errors over time so that the outstanding messages are processed successfully. But this takes a lot of time, as interdepartmental communication between the IT base and the business department is usually time-consuming.
Erroneous messages were quickly detected by SAP Basis, but a correction could only be initiated directly in the case of technical errors.
This is because the involvement of the specialist department is absolutely essential for all business management issues.
Due to the very different approaches and language used by the grassroots and specialist departments, this often resulted in friction losses and time delays.
In fact, there is a monitor for everything and everywhere. Be it in an SAP system based on very technical basis or on other non-SAP middleware systems.
These monitors are often only accessible to IT personnel who are often physically very far away and not visible to the person who needs it immediately: the business department.
With the Seeburger Console, these processes are displayed more transparently, holistically and centrally in the SAP system for the business department, namely exactly where the user is already located.
The specialist department is thus able to control every technical processing step directly in SAP in a user-friendly manner. Unnecessary time expenditure and the resulting additional costs can be avoided with the Seeburger Console.
Risks associated with faulty EDI messages
However, there are not only faulty messages, but a distinction is also made between missing EDI messages and EDI messages with different content.
In the case of erroneous messages, the risks are well known and quickly become apparent if no expected booking was made as a result. But what about messages that simply fail to appear, or successfully posted documents that should not have been posted?
The specialist department is used to finding error messages directly in SAP and taking appropriate action. However, it often gets lost in the everyday stress when messages simply fail to appear.
There are many reasons for this: it may be that they were not sent by the partner in the first place or that they ran into an error in the EDI subsystem.
Despite syntax checks on the SAP side, content-related field value deviations can still occur and lead to a document posting.
As a case study, an order was created in SAP and confirmed by the partner. In the next step, the delivery is made by the partner; however, the quantity differs.
This does not necessarily lead to an error, but there may be discrepancies in the inventory. In both cases, there is usually no notification to the department.
In this case, the appropriate use of control instruments directly in SAP ("target monitoring") can provide automated information, e.g. by e-mail, so that the department is informed in good time if EDI messages are missing or if field values differ in content from the document already posted.
Audit-proof document adjustment
In line with common compliance requirements, erroneous EDI messages can be adjusted and posted or sent with little effort, no matter what status the message is in:
No matter if the message is technically wrong or wrong in content.
However, there are also different ways and tools to perform a posting successfully. An EDI message consists of designations such as base or message type, technical segment names and often only five-digit technical field designations.
From the point of view of the business department, it is highly desirable for an EDI message to have precisely no such technical designations.
It is therefore better to use descriptive terms in the event of a necessary correction in SAP. Currently, as in this case, the IT expert must support the business department.
With the help of a suitable tool in SAP - such as the IDoc Document Processing Station as part of the Seeburger Console in SAP - all technical identifiers of a message are translated into a user-friendly format.
This makes it easier for the specialist department to make the necessary changes up to the final posting for a document - and without having to contact the IT expert.
But now, despite the translation into a user-friendly format, the department may still not know exactly which of the values are wrong and what needs to be inserted instead.
The Seeburger Console supports the specialist department with an editing functionality in SAP. When starting the booking process, the message now remains in the respective step of a transaction and indicates the error.
Exactly here the user then has the possibility to select the correct values via a context menu and to finally post the message.
Each of these changes is documented and stored in an audit-proof manner. This means that it is possible to trace what has been changed at any time - in line with compliance requirements.
Conversions before an IDoc in SAP
Not every message can or should be posted the way a partner sends it because, for example, field values do not correspond to what the SAP system requires. Therefore, numerous changes already take place in advance on the EDI subsystems through field value conversions.
However, it often happens that new values are sent by the partner, which run into errors during conversion and are therefore not forwarded further to the SAP system. In this case, an adjustment on the EDI subsystem is required by IT experts, whose very short-term availability is often not guaranteed.
If, on top of that, these EDI subsystems are operated as part of managed services or cloud-based, the whole thing is delayed even more.
A professional solution to this problem is a recoding of EDI messages directly from SAP by the business department. The business department itself can enter any missing (field) values in SAP and transfer them to the subsystem without consolidating an IT expert.
In this way, unnecessary waiting times and thus additional costs can be avoided in the department's self-service.
Monitor EDI messages
The most important added value of the Seeburger Console is to monitor all incoming and outgoing EDI messages (IDoc) from SAP in the simplest way for the user and to prepare them in a user-friendly format - with a jump to the detailed view.
The user thus has the possibility to see exactly how the data was processed and which data ran into errors and, above all, to track which processing step it is currently in.
But not only the current processing status in SAP is visualized for the user. The message is updated, for example, with the corresponding system status/document status, a short description as well as a status text and the status of the connected EDI subsystem in the sense of a traffic light display.
Optionally, it can be decided to extend or correct the erroneous EDI message using different tools.
Logs can be extended by importing documents (such as PDFs) from the subsystem so that they are then available for viewing in detail in SAP. Comprehensive control mechanisms inform the specialist department about all deviations or errors.