Analysis of machine data drives optimization
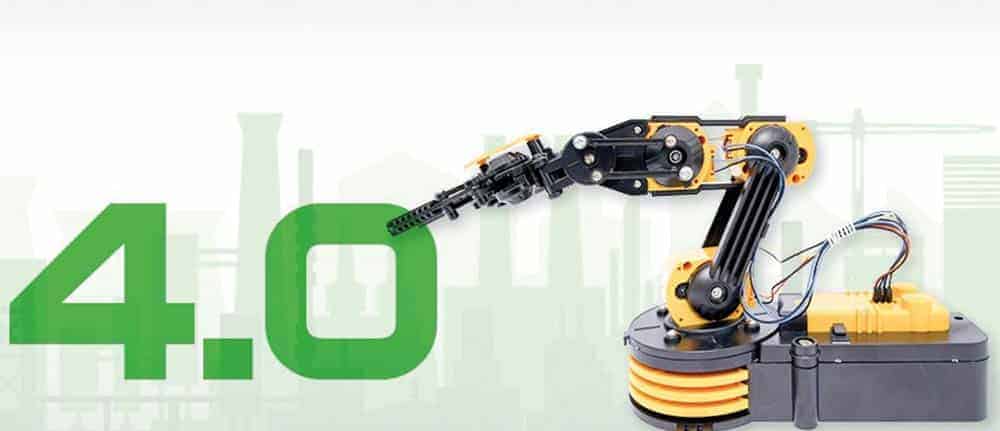
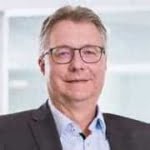
Machines on the store floor provide both product data (finished, yield, scrap quantities, throughput and cycle times) and process data (idle, operating, production and setup times, planned and unplanned downtimes). Process data can be used to derive efficiency losses in terms of availability, throughput or quality, which in turn are used to calculate Overall Equipment Effectiveness (OEE), which is based on standards such as SEMI-E10 and SEMI-E79, among others.
Exploit optimization potential
Only when this machine data is digitally recorded without gaps and analyzed in fine granularity in near real time can the transparency required to continuously improve manufacturing processes and increase their productivity be created. This is a business-critical factor these days.
To make the most of the optimization potential on the store floor, the use of a powerful and scalable self-service analysis platform is essential. It should have various filter and drill-down functions and allow the analysis of live data, which warns of the failure of a machine and indicates which jobs may still be processed.
It should be a matter of course that such a tool visualizes machine data and key figures such as OEE in dashboards in a compact and clear manner, as a diagram, graphic or table and with a defined color scheme. This can be, for example, a waterfall diagram that shows machine states distributed in different colors according to SEMI-E10 and makes improvement potentials visible.
In the best case, such an analysis platform also provides what-if analyses for simulations as well as functions for predictive analytics, artificial intelligence (AI) and machine learning (ML). These features make it possible to precisely match maintenance intervals to production, establish predictive maintenance, or extend the life of a plant without sacrificing manufacturing quality and productivity. Integrated planning functions that simplify production planning and make it more efficient are another benefit.
With the SAP Analytics Cloud (SAC), such a platform is already on the market. A major advantage of this software-as-a-service (SaaS) solution is its scalability - keyword Big Data - and the fact that users can perform and view their queries and analyses anytime and anywhere - on a desktop PC or mobile via smartphone or tablet.
SAC can be connected to a wide range of cloud and on-premises solutions, both SAP and non-SAP systems such as WSW Software's Mes Valeris. Queries and analyses can therefore be performed centrally in a single solution, producing more reliable results.
Direct access to live data
The source systems are connected either via a data import connection - in which case data is replicated to the cloud - or via a live data connection, which is currently available for BW, BW/4, S/4 and the Hana database. The live data connection enables, for example, real-time access to production data condensed and unified in BW from an MES and from ERP (single source of truth), so that faults can be identified immediately and one can react without delay.
But the requirements associated with the introduction of SAP Analytics Cloud are complex. To manage them efficiently, you need the support of an experienced partner with the necessary know-how in terms of both SAC and store floor processes. Then nothing will stand in the way of the success of data-based optimization of production.