Cloud services complement the ERP system
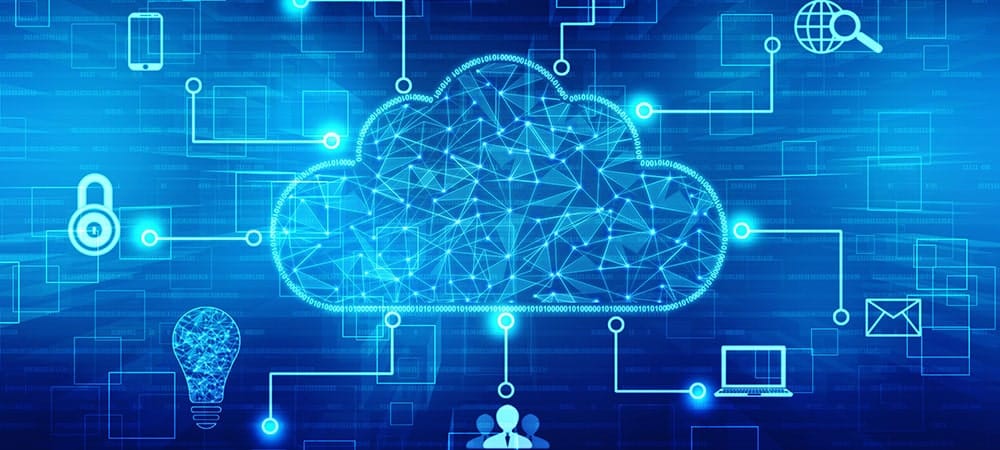
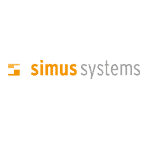
With the new simus connect cloud platform, you can achieve these goals 24/7, from any location and without investing in hardware or software. For the three typical domains of a manufacturer, there are comprehensive, highly functional software solutions with CAD/PDM, MES/MOM and ERP that ensure a high degree of digitization. These software solutions perform many functions critical to success - but they leave behind digitization gaps at the boundaries of the domains. Whenever systems rely on data from the foreign domains, conflicts and problems arise. These inconsistencies can often only be solved with interfaces, duplicated work, workarounds and numerous Excel spreadsheets. With simus connect, SAP users close these gaps through cloud services and achieve end-to-end processes.
Cloud platform simus connect
Due to limited resources, medium-sized companies do not want to invest in hardware and software, nor do they want to manage complex projects in order to achieve end-to-end processes. That is why simus systems, as a specialist for the cleansing, structuring and efficient use of technical mass data, has created the cloud platform simus connect. There, three services are offered 24/7 with which manufacturers can significantly improve the collaboration of domains integrated with SAP.
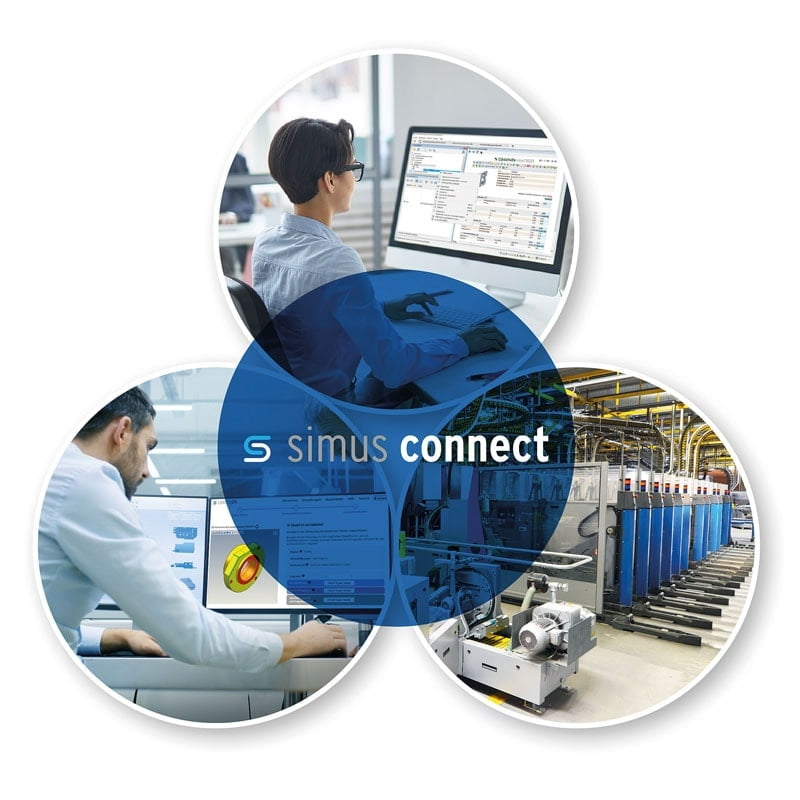
1. structure CAD models and components
Who organizes and structures the CAD models? How are they managed and prepared for further processes? While CAD and PDM as well as ERP systems provide (different) forms or lists for entries, they offer no support for the actual content task. The consequences: incomplete, inconsistent data, input errors, duplicate work, incompatible formats. How about closing this digitization gap automatically? The simus connect service from simus systems analyzes 3D CAD models in a patented process based on geometry, regardless of the modeling methodology, and classifies them fully automatically. Without the intervention of a designer, the software additionally calculates a "geometric fingerprint" for each CAD model, which enables a quick similarity search based on the native geometry. Likewise, the program fills the class-specific attribute lists with the determined values and creates 2D and 3D preview files for illustration.
If you can find the parts you need quickly and effortlessly, you won't redesign them. In this way, the entire company is spared superfluous duplicates. In purchasing, better margins are achieved through order bundling, and in production, savings are achieved through higher batch sizes and fewer items. In logistics and warehousing, lower inventories with a higher turnover rate reduce capital commitment and costs.
2. optimal work preparation
There is traditionally a high need for coordination between product development and production. But the technical data of the components on the one hand, and the information about manufacturing processes, capacity utilization, machine hour rates, material costs and finishing effort on the other, are kept in separate IT systems.
For effective detailed production planning and preliminary costing, work schedulers are just as dependent on information about component dimensions, work sequences, materials and tolerances of the future parts as they are on commercial costs and procurement prices.
simus connect automatically derives the necessary work sequences for production from the CAD model and creates a detailed work plan. Stored, customizable cost parameters result in a quick possibility for preliminary costing, which speeds up the preparation of quotations. When opting for external procurement, knowledge of product and production costs puts you in a better negotiating position, supports make-or-buy decisions and makes a decisive contribution to limiting manufacturing costs.
3. cost-conscious design
Separate silos of technical and commercial information and procurement prices leave developers in many companies in the dark about the follow-up costs of their projects. Yet up to 80 percent of manufacturing costs are already determined during product development. Often, minor changes in geometry, material or tolerances would generate significant savings! With simus connect, designers can now automatically calculate the expected manufacturing costs of their components and assemblies directly from the user interface of their 3D CAD system and display the calculation results. Without making any changes to the CAD model, costs for different tolerances, materials or surface treatments can be determined. The most expensive machining operations are tracked down and displayed in color at the touch of a button. This means that cost drivers can be identified during the development phase and effective countermeasures can be taken. Easy to use without interrupting work, the automatic calculation triggers knowledge gains, creates calculation knowledge and strengthens the cost awareness of the designers.
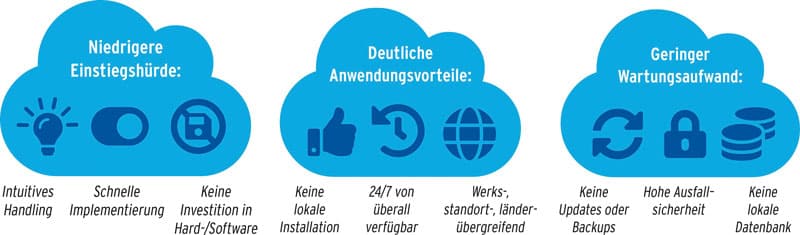
Image rights: simus systems GmbH, Karlsruhe.
Close digitization gaps now
Manufacturers have improved processes over many years and equipped the three domains of product development, work preparation, and purchasing and distribution with ERP software. Now the task is to close the gaps and thus achieve the full benefits of digitization. With the simus connect cloud platform, medium-sized manufacturing companies can use the three applications described above without their own software and hardware, in 24/7 operation, across plants, locations and countries. They thus gain a high level of reliability without the expense of updates and administration at fixed calculable usage costs.
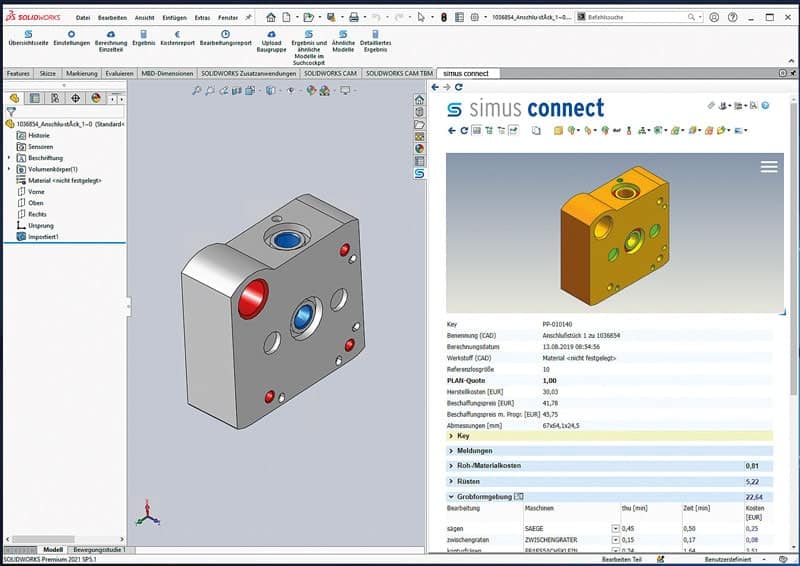