In-company training 2.0: Tablets and digital planning tool
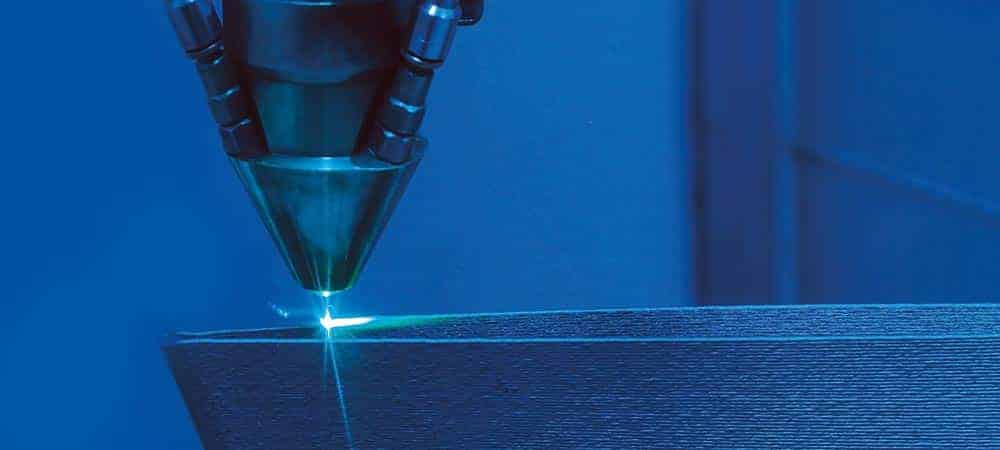
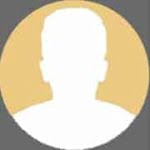
Robots, virtual reality goggles, 3D printers - apprentices find a highly modern, exciting environment at automotive supplier Hirschvogel Umformtechnik.
The training center in Denklingen alone has around 3,000 square meters of state-of-the-art CNC turning and milling machines, simulation and CAD technology available for this purpose.
Training for control and regulation technology, tablets and e-learning are also part of the program. Training manager Peter Geier explains why the latest technologies and digitalization in training are so important to the company:
"When our current apprentices enter the workforce in a few years, many of them here at our plants, we want them not only to understand these new technologies themselves, but also to become trailblazers, multipliers, by passing on their knowledge to their work teams."
The requirement to be up to date in training is not limited to content, but also applies to processes: A large proportion of training management now runs digitally. Peter Geier reports on how this came about:
"With a good 160 trainees being trained both here at the center and at two other plant locations, it is quite a challenge to organize exactly who works on which machine and when. In the past, we mainly used Excel tables.
But adjusting the data in the planning and Outlook calendars after each change and then resending the information by mail increasingly seemed very time-consuming and error-prone."
In addition, there was also no record of which qualifications were taught at the respective workplaces. The company wanted to organize all of this better and more clearly using suitable software. All qualifications and training stations were then to be displayed and retrievable at a glance, as well as the grades and assessments achieved and the report books.
A capacity-oriented allocation of the machines was to be made possible in order to prevent overcrowding and waiting times and to optimize the utilization of the machine park. The other selection criteria were:
Interface to existing SAP HCM (Human Capital Management), integration of in-house courses such as presentation training, evaluations and reports, planning data should be available for export and further distribution in formats such as PDF files, MS Outlook or Excel.
While most of the programs then reviewed were able to meet these requirements more or less comprehensively, two points tipped the scales in favor of the decision: Flexibility and integration with the existing SAP HCM and thus the elimination of expensive interfaces.
The decision was made in favor of Lighthouse, which offers such fully HCM-integrated, intuitive software in the form of its standard software Bluelight.
"With Lighthouse, in addition to the software, we have also found a cooperation partner who is open to further developments. Since we have been using the solution, we have already been able to optimize and jointly develop several functions, and these results then benefit other users as well."
says Peter Geier.
Nine job profiles
Before the solution could be customized and implemented for Hirschvogel in close cooperation with the internal SAP team, the company still had some "homework" to do:
Hirschvogel offers a total of nine apprenticeship occupations, including the six core occupations at the training center: Industrial mechanic, toolmaker, machinist, mechatronics technician, electronics technician for industrial engineering and technical product designer.
The plants also train materials testers, IT specialists and industrial clerks. For each of these apprenticeships, the first task was to describe the respective job description once again more clearly.
The descriptions include both the content specifications and competencies from the IHK framework plans and additional, company-specific requirements. The steps for acquiring each individual competence were then broken down in detail.
Together with the data on when which machines and workstations are available, very precise time- and capacity-optimized throughput plans can be created.
Bluelight was initially tested in 2015 in a pilot project for the six core job profiles, in parallel with the running system. After around one year of successful testing, the new system was transferred to the production system.
Roles and rights had been defined in advance, and the trainers had also been trained. Analogously, the three additional job profiles were integrated in the following year.
Courses, plans and grades at a glance
It is now easy to keep track of everything, even with 160 apprentices and several locations: When and where does the basic metal course for the first year of apprenticeship take place?
A click in the schedule shows not only the location and times, but also the responsible trainers. In-house training courses and vocational school days are also stored in the system. The schedules are automatically transferred to the trainees' personal Outlook calendars.
Grades and evaluations are entered by the trainers. The results of the feedback discussions customary at Hirschvogel are also reflected in the system, thanks to additional programming.
In this way, the full-time trainers can see at a glance where each individual young person currently stands in their training. Evaluations and reports can also be created as desired.
Peter Geier emphasizes the new software's contribution to quality assurance. Since the individual planning steps in Bluelight build on each other, the system "educates" the users involved, so to speak.
Only when the acquisition of a qualification has been confirmed in writing by the trainer and trainee can the next stage be planned:
"My particular highlight as training manager is that with the system we now also have a very clear structure, a standard that applies to everyone. That helps us avoid mistakes and inaccuracies."
He describes the collaboration with Lighthouse as fruitful and productive. In parallel to the rollout plans for further company locations, Hirschvogel is also currently thinking about the future.
High on the wish list is the automated adjustment of schedules in the event of last-minute changes to machine occupancy and trainee attendance - no easy task for standard software.
A new functionality that should particularly please the trainees will be implemented in the company by the end of the year: They will then receive their individual training plans directly on their smartphones.