Digitization and standardization

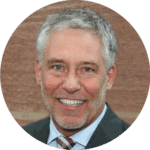
Uhlmann Pac-Systeme digitizes worldwide service with MobileX
In order to standardize and optimize its global service processes due to strong growth, Uhlmann Pac-Systeme was looking for an intuitive, future-proof and offline-capable solution for integration with SAP CS and HR in 2017. In addition, the project aimed to improve the quality of reporting and accelerate the turnaround times of service orders. With its packaging lines, comprehensive services and digital solutions, the company offers consulting, project management, implementation and services from a single source as a total solution provider.
Uhlmann Pac-Systeme ultimately opted for MobileX-MIP for Field Service, primarily because of the solution's adaptability to the specific requirements of the pharmaceutical industry. Another decisive point was the MobileX release monitor, an add-on module of the mobile solution, which allows the office staff to check the technicians' confirmations before they are posted in SAP.
The roll-out began in Germany in January 2019. The solution was then rolled out to all service agencies, for example in Austria, Sweden, France, China, and the UK. Since 2020, MobileX Field Service has now been in use at Uhlmann Pac-Systeme worldwide in five languages (German, English, Spanish, French and Chinese).
The service technicians receive their orders on their tablets or laptops and can use them to view all details about the order and the system, such as the service history and instructions. The orders are for repairs, maintenance, preventive maintenance measures or plant conversions. The commissioning of new plants is carried out by dedicated teams of fitters, programmers and project managers, who spend one or even several weeks on site at the customer's premises for the installation. They also use MobileX-MIP to document their work.
Dynamic forms
In addition to feedback containing information on working hours and details in text form, the technicians and fitters also use the mobile solution to create their service reports and fill out checklists and forms. Using the "Dynamic Forms" module, for example, quality assurance checklists are created at the end of installation and signed by the customer. This ensures maximum work and legal security.
The use of a release monitor has, above all, digitized the internal release and follow-up processes of service orders and thus massively simplified and accelerated them. Whereas previously all order documents and checklists had to be manually transferred in paper form or scanned and checked in order to initiate subsequent processes such as the release of travel expenses, payroll accounting and invoices to customers, the checking of feedback and triggering of follow-up processes is now carried out digitally and largely automated across all departments using the release monitor. In this way, the internal logistical effort could be reduced by 95 percent and the increased order volume could be fulfilled with the same number of employees.
The digitization of service orders at Uhlmann Pac-Systeme's Laupheim site has made it possible to do away with eleven folder trolleys that were filled with around 2,000 paper folders every year. Already during the roll-out phase, this saved 35,000 pages of printouts per year, which is equivalent to half a ton of wood, over 9,000 liters of water, 1,800 kW/h of energy and 185 kilograms of CO2.
"The data quality of the feedback and checklists has improved exorbitantly with the introduction of MobileX-MIP for Field Service," explains Kai Kathan, Team Leader Services at Uhlmann Pac-Systeme. "In addition, we have been able to cut service order turnaround times by more than half. We are also demonstrating our innovative strength as a market leader to customers by digitizing order processing."
For the future, Uhlmann Pac-Systeme plans to expand the use of Dynamic Forms. More technical details such as equipment-related information or outstanding activities from the last operation are to be transferred to the form so that technicians are even better equipped for their operations and can fill out forms even more easily.
As part of the Uhlmann Group, Uhlmann Pac-Systeme is the world's leading systems supplier for pharmaceutical packaging machines with 19 locations in 14 countries. Over 100 service technicians are deployed worldwide to service and maintain more than 10,000 machines in 80 countries.
