Effective and efficient maintenance
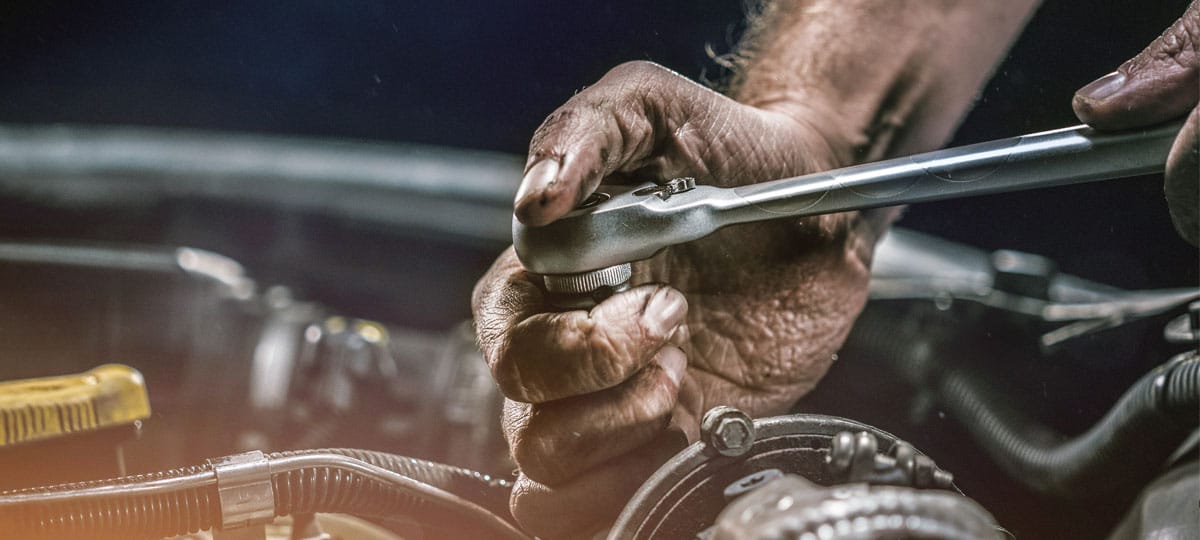
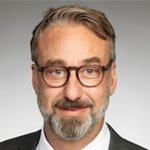
Integrated Business Planning (IBP) for Maintenance, Repair and Operations (MRO)
For it is only by "mentally anticipating future action by weighing up various alternative courses of action and deciding on the most favorable path" - as the German economist Günter Wöhe defined planning - that it is at all possible to get at least a little solid ground under one's feet and to limit the many imponderables.
The bottlenecks along global supply chains and the shortage of skilled workers have shown very clearly in recent years how important it is to plan in order to make the best possible use of scarce and valuable resources.
We are also seeing increasing commitment in the context of maintenance, especially in short-term planning, which covers the time horizon of around the next eight weeks and is aimed at specific maintenance orders. By contrast, medium-term (from around eight weeks) and long-term (from one year) maintenance planning are not yet so much on companies' agendas.
Squaring the circle: Reduce MTTR (Mean Time to Repair), increase MTBF (Mean Time Between Failures) while reducing costs. Whether in the short term, medium term or long term, the goal of maintenance planning must be to provide the right resources and materials so that maintenance runs on time and effectively. This contributes to high asset availability and reliability. In addition to this effectiveness dimension (doing the right things), there is also an efficiency dimension (doing things right): The available employees, vehicles, tools and materials, and service providers should be used optimally. This means reducing the Mean Time to Repair (MTTR) and increasing the Mean Time Between Failures (MTBF) while minimizing maintenance and inventory costs is the high art of planning.
Resources and budget
Whereas short-term planning involves planning the available resources and materials, medium-term and long-term maintenance planning is concerned with providing the necessary resources and materials based on future requirements and planning the necessary budget for them: employees must be recruited, retained and further qualified, tools and machines procured and reserved, and external service providers commissioned. This sounds trivial - but it is quite demanding due to the enormous change in almost all areas. In order to implement planning against this background that really helps to ensure effective and efficient maintenance, deep integration is essential. But some companies still use traditional spreadsheet tools like Microsoft Excel for their planning.
In the present, it is not necessarily clear what the actual requirements will be in the future. It is possible to extrapolate the requirements based on the respective maintenance strategy. However, this requires a very good database of past maintenance activities, current maintenance plans and the current condition of the equipment. In many companies, this is not yet a reality. In addition, components that are replaced during maintenance are often reconditioned or manufactured internally or externally. These "secondary requirements" must also be taken into account in maintenance planning, which further increases complexity.
The challenge in long-term maintenance planning is to take these influences into account in good time and to initiate appropriate measures at an early stage. Knowledge of these influencing factors is distributed among various people in companies, who must work together in an integrated process.
If measures are not addressed in good time, problems that arise may not be solved in the short term. For example, given the current shortage of skilled workers, it is conceivable that it will take months or even years to expand the existing team. A similar shortage exists for tools, spare parts and external service providers. Supply chain issues can further exacerbate the situation for companies.
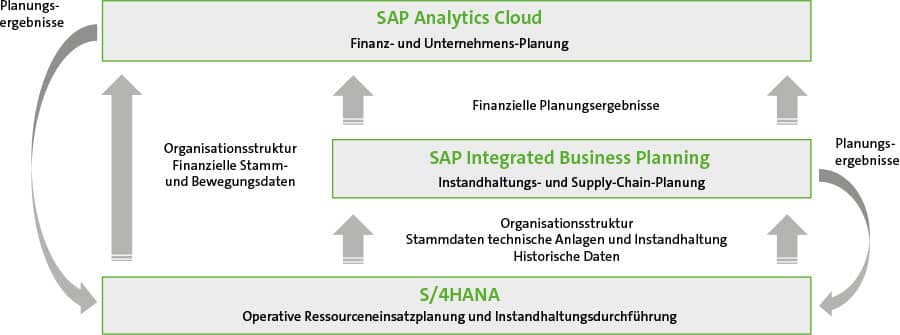
Integrated applications
However, integrated maintenance planning cannot be realized with Excel alone. Instead, dedicated and integrated applications should be used. On the one hand, this involves the systems in which the necessary master data (for example, equipment, maintenance plans and routings) and transactional data (for example, orders and confirmations) are stored. In an SAP environment, this is essentially S/4 (or ERP/ECC 6.0).
On the other hand, applications are required with which planning can be carried out on the basis of the existing data. This is possible in part with S/4 and includes, in particular, short-term and operational planning. SAP offers the standard solutions S/4 Asset Management for Resource Scheduling (RSH) and SAP Field Service Management (FSM) for this purpose.
In addition, SAP Integrated Business Planning (IBP) is a cloud-based application that can be used to plan all aspects along the supply chain. IBP for Maintenance, Repair and Operations (MRO) is available specifically for maintenance planning. The tool reads the master data and transactional data via an interface and determines the requirements. Based on the requirements, the inventory is optimized on the one hand and the supply of resources and materials is planned on the other. The procedure depends on the maintenance strategy.
Preventive maintenance consists of cyclically recurring measures. The requirements can therefore be easily derived from the maintenance and work schedules. For corrective maintenance, predictions must be made on the basis of transactional data from the past. The requirements are derived from the assumed incidents. Increasingly important in the mix of maintenance strategies are condition-based and predictive maintenance. The connection of new digital components and sensors makes the current condition of machines and systems transparent and enables valid forecasts to determine requirements.
Special cases are projects for the renewal, improvement or expansion of assets and customer service. In the case of projects, the requirements from individual project planning are the input for resource planning; in the case of customer service, it is the support agreements made and sales planning.
Maintenance, Repair, Operations
The approach in IBP-MRO is based on time series planning. This means that planning is consolidated in time intervals and not based on individual maintenance orders. By default, IBP-MRO follows the process below, but this can be customized to meet individual customer needs.
Both master data (functional locations, equipment, materials, routings, maintenance plans) and transaction data (material postings and order confirmations) are transferred from S/4 Hana to IBP and mapped to the master data structures and key figures in SAP Integrated Business Planning. For this, IBP uses the SAP CI-DS tool, which is always delivered with IBP. SAP standard extractors are available for all the data mentioned above. The requirements for preventive maintenance come from the maintenance plans and task lists maintained in S/4. The maintenance plans are used to derive when the maintenance activities are to be performed. The task lists are used to break down what effort and which materials are required.
Corrective maintenance
The expected demand for corrective maintenance is calculated for each effort and material. For this purpose, IBP-MRO provides operators based on the Croston-TSB method, which are geared to discontinuous requirements. The data basis is the key figures previously derived from the historical order confirmations and material bookings.
Optimal safety stocks and reorder points are determined from the results of requirements planning for corrective and preventive maintenance as well as the material master data and their segmentation. Finally, for a complete planning cycle, the target/actual comparison can take place, which is usually performed either in IBP or in SAC. The basis for this is the target data from IBP or SAC and the actual data stored in S/4.