Fast entry into digital manufacturing
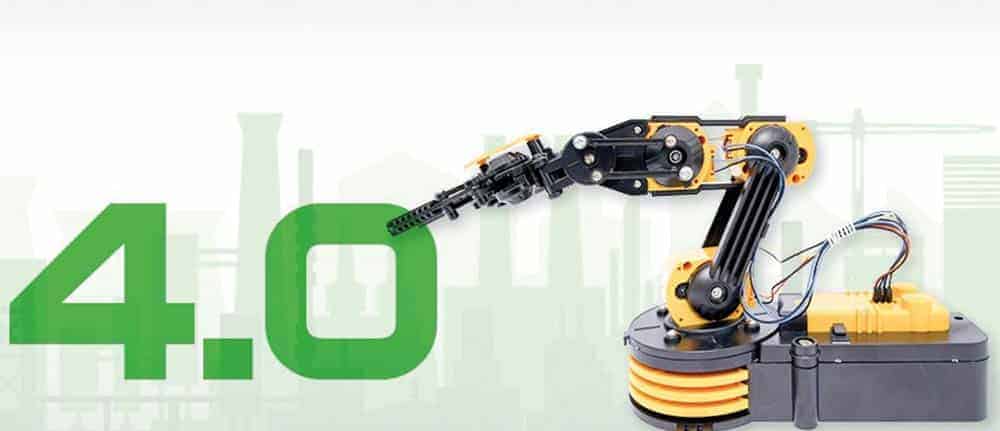
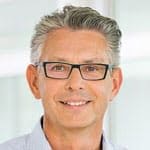
Many small and medium-sized industrial companies already efficiently handle commercial processes in ERP software from SAP (Business Suite 7 or S/4 Hana) and logistics processes in a logistics and JIS platform. However, in order to exploit the potential offered by the digital transformation and Industry 4.0, a clear view of current manufacturing operations is also necessary. This is provided by a manufacturing execution system (MES), which brings together information from individual data sources in production as a central "hub".
However, the use of such systems is not very widespread in medium-sized industrial companies. They are afraid of the long implementation period of a "classic" MES and the associated costs, which increase if commissioning is delayed by numerous adjustments and change requests. In addition, the usability and the range of functions of conventional MES often do not meet the needs of the users.
Many medium-sized companies still record their product data (finished, yield, scrap quantity, throughput and cycle time), process data (idle, operating, production and setup time, planned or unplanned downtimes) and quality notifications decentrally in CSV and Excel files, self-developed solutions, sometimes even on paper. The pitfalls of such an inhomogeneous database are well known: There is a lack of transparency about the manufacturing process, seamless tracking and tracing is almost impossible, and central questions about the optimization potential of throughput times or plant efficiency cannot be answered precisely, if at all. The use of special apps to map production processes is also not an option. It harbors the risk of a proliferation of apps and interfaces, which inflates the IT landscape, increases operating costs and places an additional burden on internal IT, which is usually understaffed and underutilized.
The way out of this dilemma is a modern, lean, intuitive and web-based MES that enables fast and cost-effective entry into digital manufacturing and tracking and tracing. The prerequisite for this is that it maps all production lines and workstations as a digital twin and thus reflects store floor processes and production logic one-to-one. It is just as important that business users and process engineers without special IT knowledge can configure their process and production parameters themselves according to the low-code/no-code approach. This, as well as the roll-out without outside help, is a real added value, because it relieves the internal IT and eliminates the costs for external IT consultants.
Invaluable benefits are also offered by an interface that is consistently designed according to the UX, which guides the end user safely and with dialog support through all process, configuration and administration steps, thus accelerating workflows and preventing incorrect entries. Target/actual comparisons of process parameters in real time, digital execution and confirmation of test instructions, and automatic locking of production in the event of an error are further plus points. In the best case, the MES has functions for analyzing the actual process parameters and directly triggers an alarm in the event of a deviation or malfunction on a machine or workstation, so that maintenance or servicing can be initiated immediately.
The MES should also be continuously developed by the supplier, support interface standards such as OPC UA for digital networking of production and the MQTT standard for IoT scenarios, and allow simple connection to SAP software and a logistics and JIS platform via Rest APIs. If it can also be scaled flexibly and operated in the cloud (private or public), hybrid or on-premises, the way is clear for digital production and a smart factory.