First on the market
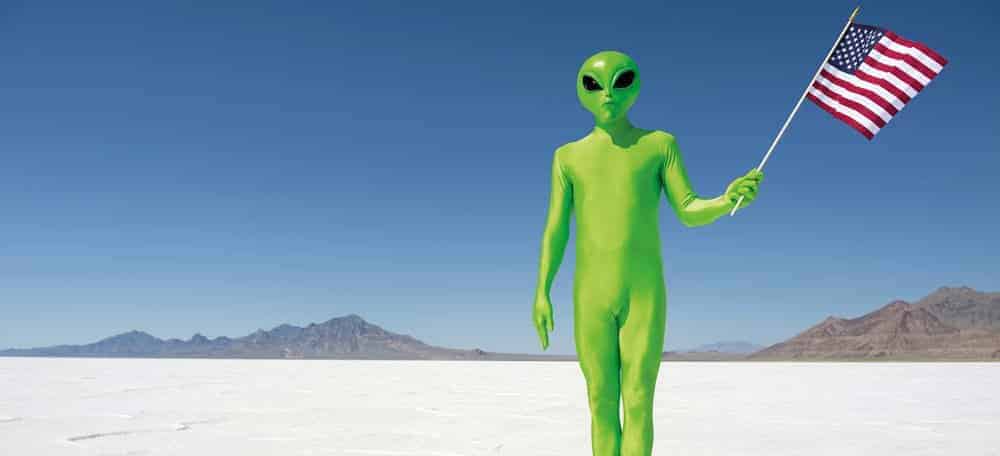
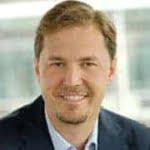
Market dynamics are doing their part to increase product diversity to an unprecedented extent and shorten product life cycles. At the same time, disruptive market players and business models threaten established companies.
Capturing SAP data digitally, more streamlined and faster, helps shorten launch cycles - enabling large enterprises to move quickly and agilely to survive in today's competitive market environment.
Leaner product introduction processes
Around 120 SAP professionals from supply chain, IT and product management in manufacturing companies were surveyed. The emergence of the "millennials", i.e. those born between 1980 and 1990, and the increased use of all available communication channels by consumer groups are seen as drivers of massive product proliferation.
Consumers increasingly rely on mobile devices and expect products that fit their lifestyle. They want new shopping options as well as greater transparency in terms of ingredients, components and the companies behind a brand.
Transformation at consumer and business level
Such changes in consumer behavior have a ripple effect. Supply chain partners are adapting and aligning more innovatively to produce the ingredients, raw materials and components that drive the consumer economy.
Change is also based on rapid technological innovation. The Internet of Things, machine learning and artificial intelligence will continue to influence or even change product design, manufacturing and distribution.
Ubiquitous broadband and mobile technologies, coupled with Big Data analytics, will transform business in ways previously unimaginable.
This market dynamic is seen as a door-opener for smaller, more agile manufacturers, who are making strong inroads into the territory of established companies and cutting into their profits. This fact has not gone unnoticed by the managers of large companies.
According to KPMG's "2016 CEO Outlook," 78 percent of business leaders are concerned that their products will lose relevance over the next three years.
Barriers to the necessary changes
With all this change, however, one thing is clear: To survive and thrive, large companies must design and deliver their new products at an unprecedented pace and breadth.
Unfortunately, not everyone is prepared for this challenge. The survey revealed that more than half of the interviewees still rely on manual processes to obtain the SAP operational data required as part of a product launch.
In contrast, 75 percent of study participants feel the need to pick up the pace. The most frequented method of data entry is based on spreadsheets and e-mail messages.
Yet twelve percent of companies still rely on paper forms. Slow, manual processes for data retrieval or suboptimal automated workflows are increasingly hampering growth.
Especially when you consider the increase in new products that manufacturers are trying to market to keep up with changing demands and business models. 75 percent of the manufacturers interviewed expect the number of new products to increase over the next four years.
And the scale of the growth they are forecasting is substantial, at 79 percent. Accordingly, they would have to increase their capacity by over 25 percent in the next few years.
Some companies may struggle to increase staff quickly enough to meet the new requirements. And those that are able to hire more staff must reckon with the extra costs incurred reducing their profit margins or dwindling them altogether.
Complex launch processes
Anyone with experience in launching products with SAP knows the dimension of the task at hand. There are hundreds of data fields to be filled in - and only for one newly completed product.
Each of these goods is supported by numerous other master data records. These include, for example, raw materials, invoices for materials, recipes or routings.
Just a small error in a single field - such as a unit of measurement - can have costly consequences. And this is not only true when dealing with a broad database or complex data.
Bringing a new product to market requires data inputs and/or approvals from various teams within the company. Whether it's a brand new, innovative product, an extension of a product line, geographic expansion, or a simple component change: There are generally eight or more departments involved in this process of a new product introduction (NPI).
Room for improvement
Given the large amount of data involved, the cross-functional nature of the process, and the prevalence of manual data collection methods, it's not surprising that manufacturing professionals see a lot of potential for improvement.
Here, respondents cited "simplify and automate manual processes," "deploy more staff," "automate data capture and entry into systems," "enable implementation of rapid process changes," "gain more process visibility," and "ensure better data governance and validation."
Nearly one-third of respondents believe that automated data capture and entry would have the greatest effect on their NPI process. In contrast, about a quarter see optimized data governance and validation as crucial.
Digitize and unify
For those large enterprises that rely on SAP to manage their manufacturing processes, there is good news. With today's powerful workflow solutions, a lot can be accomplished to automate the product launch process.
At the same time, NPI life cycles that are half as short or twice as many new product launches with the same staffing level are no longer utopian. There are workflow solutions that accelerate the data acquisition process enormously and ensure high data quality.
This is ensured by functions for parallel task execution and convenient validation. This enables different departments to provide and release data simultaneously. This saves valuable time and relieves employees of tedious, error-prone and annoying manual data entry.
Sophisticated software with deep SAP integration is able to both automate data entry and reconcile data with SAP. In addition, data quality can be further improved by adding additional business rules to those already available in SAP to achieve the highest possible level of data quality.
Whether adding required fields or limiting the values users can choose when entering data: Integrated workflow solutions have a wealth of data editing capabilities to ensure that new product data is entered correctly the first time.
Modern workflow solutions, such as those from Winshuttle, are not only suitable for IT departments. SAP business analysts or SAP power users who are familiar with the business process and data can also create flexible workflows to give wings to their launch processes - even without Abap programming.
Conclusion
Of course, even the best automation software cannot optimize a poorly set up or suboptimal process in such a way that convincing results are achieved. Therefore, it is advisable to first analyze and understand the business goals and current processes together with the customer in order to apply industry best practices in the next step.
This is the only way to ensure that a process is digitized that has proven itself in practice. This step-by-step approach usually leads to 50 percent shorter NPI cycles.
In today's highly competitive and dynamic marketplace, every day counts. Getting products to market faster not only drives sales, but can also help manufacturers be first to market - giving them a competitive edge that can make the difference between success and failure.