Industry 4.0 refreshes plants
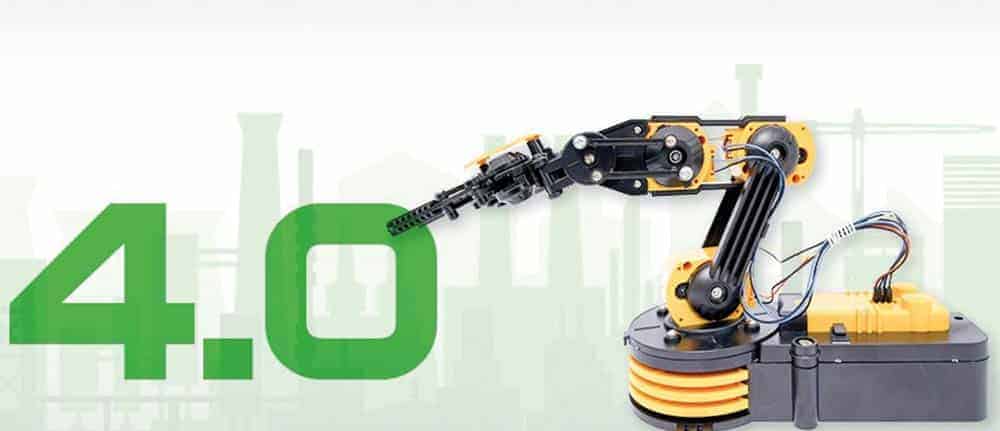
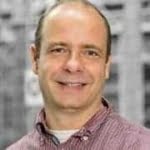
New trends are increasingly finding their way into the various sectors of industry. Production processes and different business areas are increasingly benefiting from the possibility of digital networking.
Immense amounts of data also expand the range of options available in the Industry 4.0 era. The framework for capturing relevant data begins at the production site and ends with delivery.
However, decision-makers often fail to recognize the full potential of the collected information material. Detailed data analyses ideally help to optimize processes and generate time and cost savings.
Efficient use of Big Data often generates an edge in close competition through the resulting adjustments. It is therefore advisable to incorporate solutions into existing systems that support evaluation.
In intralogistics, for example, innovative technology can be used to identify sources of error and potential for optimization in the material flow.
With such software, even automated plants can be controlled specifically by ERP systems. If this newly introduced program also has flexible interfaces, companies modernize independently of manufacturers and save almost 70 percent of the usual commissioning time. If, for example, SAP is already being used, the new solution ensures problem-free continued use.
The interfaces addressed also dissolve existing isolated machine solutions. Existing ERP and WMS systems provide the basis for linking the plants with each other in a meaningful way.
Communication mainly takes place via TCP/IP connections. This is a prescribed sequence of work steps in which the concatenations exchange telegrams with each other.
TCP ports regulate the transmission and communicate only what the current process actually requires. In SAP systems, there is the additional feature that Remote Function Calls transmit IDocs and SAP communicates event-driven telegrams via TCP/IP.
This feature is already available in SAP as standard. In addition, everything is programmable, so users do not have to modify existing PLC programs. Priority in the modernization and merging of different software is the allocation of task areas.
Since many companies already use SAP for their plants, the breakdown is similar for many projects. In intralogistics, for example, SAP continues to control master and order data, invoice creation, inventories per delivery unit, reservations, and inventory for orders and transport setting.
In contrast, the integrated software manages the warehouse layout, the routes in the warehouse or in production, and the warehouse strategy. A clear demarcation also reduces communication between the new system and SAP.
Only what is really needed for an optimized material flow should be passed on via the interface. This creates a synergy, as the new software omits these functions and lets SAP manage them.
Many companies are not yet confident enough to take the step toward new technologies. On the one hand, decision-makers fear high costs, and on the other, they consider existing processes to be mature.
However, data and the digital transformation offer new opportunities and open up new markets that companies should not resist. They will lose competitiveness in the long run.
Modernization measures that connect existing plants regardless of manufacturer and save costs are therefore a low-risk alternative. It is important that companies also take small, cost-effective steps toward the smart factory.
Those who gradually modernize plants and warehouses and thus get employees used to the new technologies create more acceptance for the digital transformation in the long term.