Maintenance: Mobile, offline and affordable
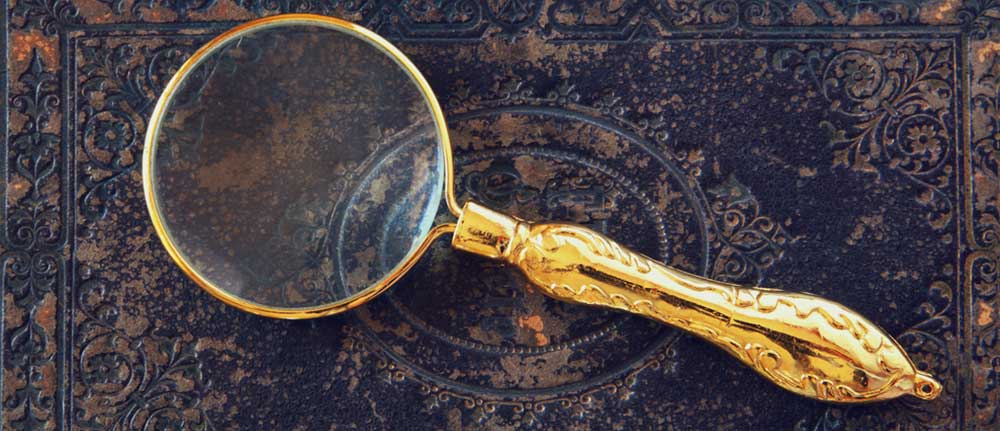
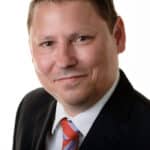
The Medical Devices Act and the Medical Devices Operator Ordinance demand a lot from ERP systems. Although the legislator has established clear guidelines for the installation, operation, use and maintenance of medical devices, the management of evidence of who has been instructed in which device is a considerable logistical challenge.
The least practicable option here is undoubtedly the hard-copy variant, i.e., carrying appropriate passports or keeping central paper lists. On the other hand, digital administration of referral management is not possible with a standard SAP delivery without additional developments.
Regardless of the industry, the operation and maintenance of equipment and products also require precise knowledge of the respective life cycles. This can be achieved by permanently switching back and forth between the required modules and building blocks, even within SAP.
Considering there are well over 100,000 pieces of equipment in an average hospital, however, that's not exactly a viable, let alone professional, solution.
In addition, technical facility management does not only take place in the comfort of the office, but sometimes also on site at the respective device - often without a stable online connection.
The technical possibilities to be this highly agile and flexible are available. However, the online components and the SAP cloud platform offered for this purpose are too expensive for many users or too complex to implement. In addition, important applications such as hospital or patient information systems are highly specialized in healthcare facilities.
And finally - to protect operational and patient data - applications that open SAP systems to the "outside" for the cloud are often not even considered. So innovations like SAP Fiori cannot simply be implemented here on a whim.
The answer to the above challenges is a modern, mobile cockpit called Snap TFM. In this technical facility management tool, more than 250 standard transactions can be addressed and master data from the PM, CS, PS, MM, RE and RE-FX modules can be edited.
The Snap MOB mobile application relies on SAP's own Fiori technology. It meets all requirements with regard to the documentation of safety-relevant technology and also satisfies the operational needs of employees in plant, building and equipment management.
At the same time, the mobile version proves that Fiori is not an SAP buzzword, but that the strategic decision in favor of it can actually solve the problems mentioned:
The order backlog can be operated completely offline and synchronized in an automated or manually triggered manner as desired. The fact that the use of SAP Mobile or the SAP Cloud Platform can be completely dispensed with reduces the effort (and sometimes also the doubts) on the customer side considerably.
Thanks to development based on the SAP UI5 user interface, these web applications run just as stably on the desktop as on mobile devices. And Fiori ensures that the user-friendliness of the applications also deserves this designation - something that was not always a matter of course with software from Waldorf.
The fact that the cockpit and mobile application are based on tried-and-tested processes also benefits smaller companies, because they can become productive very quickly at moderate cost. So the conclusion is: Yes, maintenance is possible - mobile, offline and affordable - with the right technology and the right tools.