Master data governance with added value
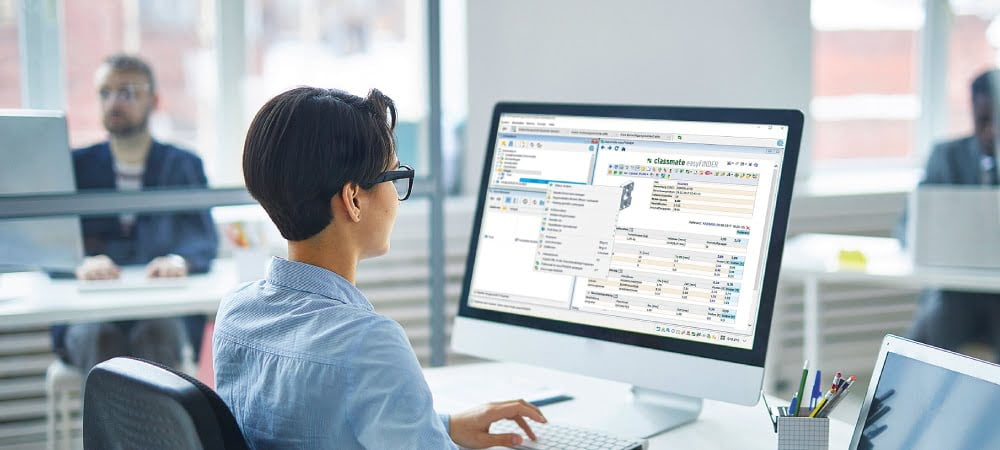

In all companies, every department, from engineering to marketing, has to create and maintain material master data. Responsibilities and process steps are rarely fully defined. If you want to ensure clarity in the ERP system, you have to define the authorization concept down to field level - a rigid and time-consuming solution. After all, a master data record can contain several hundred fields that are necessary for purchasing, production, logistics or sales.
Analyze and define data quality
What is written in the fields is also important - the quality of the content determines the success of digitization. The first step towards error-free processes is therefore an analysis of the existing data, combined with a quality target for the respective criteria. This means defining rules for the relevance and correctness of the data. This includes binding specifications for clear article designations. simus systems, a specialist in the cleansing, structuring and efficient use of technical databases, has developed a target-oriented methodology for this. The simus classmate software modules apply these rules efficiently to extensive databases.Â
Define responsibilities and processes
Clear responsibilities for the respective data content and data maintenance should already be defined during this project. Based on the experience gained in hundreds of projects, Simus systems recommends setting up a master data office or a master data officer as a contact person for all employees concerned. Together they develop processes for the creation and maintenance of material masters and the persons responsible for them.Â
Powerful tools
In this important task, employees are equipped with intelligent software modules from simus classmate. This includes a fast search engine that makes it easier for all departments to find data according to geometric, numerical or alphabetical criteria. This tool is particularly useful in the design department: Anyone who finds matching or similar components does not have to develop them from scratch. As a result, not only does the database grow more slowly, but also the purchasing volume and stock levels.
Material master application process
If the required part is not in stock, the search parameters are used as a template to request the creation of a new material master. If the master data team cannot find a suitable part and the request is filled out completely and correctly, the material is created in a structured way in ERP systems such as SAP via simus classmate. Automatic processes and e-mail notifications are set up for this purpose. This automated procedure prevents incorrect entries and duplicates and reduces the permanent growth of the component stock at manufacturers.
Flawless material master maintenance process
A customizable, comprehensive maintenance process is implemented in the same way. Each material passes through various processing steps until it is fully defined. For example, a drawing part is defined in engineering and passed on to work preparation with a visible status change. The software uses logic and plausibility checks, suggested designations and predefined formats to ensure that all fields are completed in accordance with the rules. This allows everyone involved to complete their respective tasks quickly and with concentration. The process often extends across distributed locations. The processes can be modified according to many specifications - for example for different types of material. Based on optimal master data, production information can then be provided, carbon footprints calculated and costs saved.Â
Added value of simus classmate
The simus classmate software suite, on-premises or in the cloud, delivers the added value of higher component reuse rates, cost-conscious design and the calculation of product carbon footprints in addition to optimum engineering data.
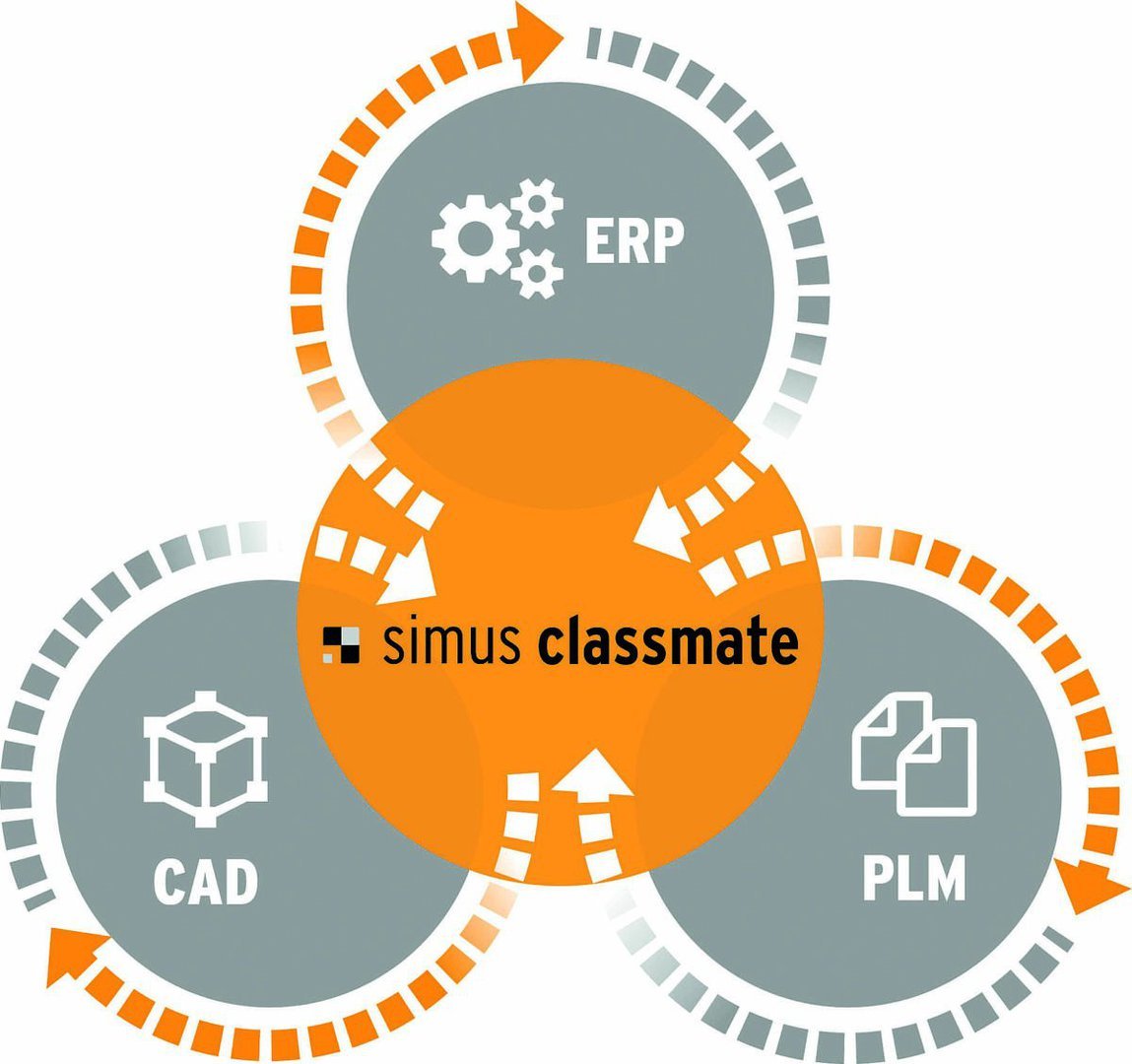
simus classmate combines the domains of product development, production, procurement and sales in end-to-end processes.Â
Provide manufacturing information
There is traditionally a great need for coordination between product development and production. Nevertheless, the technical data and CAD models of the components are kept separate from the information on manufacturing processes, capacity utilization, machine hour rates, material costs and finishing costs. simus classmate brings both areas together. The software automatically derives the necessary production sequences from the CAD model and creates a detailed work plan. Stored, customizable cost parameters are used for preliminary costing, which speeds up the preparation of quotations. The complete information facilitates decisions between in-house production and external procurement. If the latter is chosen, the knowledge of product and production costs gives the purchasing department a better negotiating position. In this way, the use of simus classmate helps to reduce manufacturing costs.
Determine product carbon footprint
Sustainability is becoming an important goal for many manufacturers, which also affects product development. The reduction of carbon dioxide emissions plays an important role - new products should be manufactured as CO2-neutral as possible. With simus classmate, the effects of each individual production step can now be calculated individually and precisely for each component and linked to information on the emissions generated.
Cost conscious design
Designers can also use simus classmate to automatically calculate the estimated manufacturing costs of their components and assemblies directly from the user interface of their 3D CAD system and display the calculation results. Costs for different tolerances, materials or surface treatments can be determined without making changes to the CAD model. The most expensive processes are identified at the touch of a button and displayed in color. This allows you to identify cost drivers during the development phase and take effective countermeasures. Easy to use without interrupting work, the automatic calculation triggers knowledge gains, creates calculation knowledge and strengthens the cost awareness of the designers.
