MES as an enabler
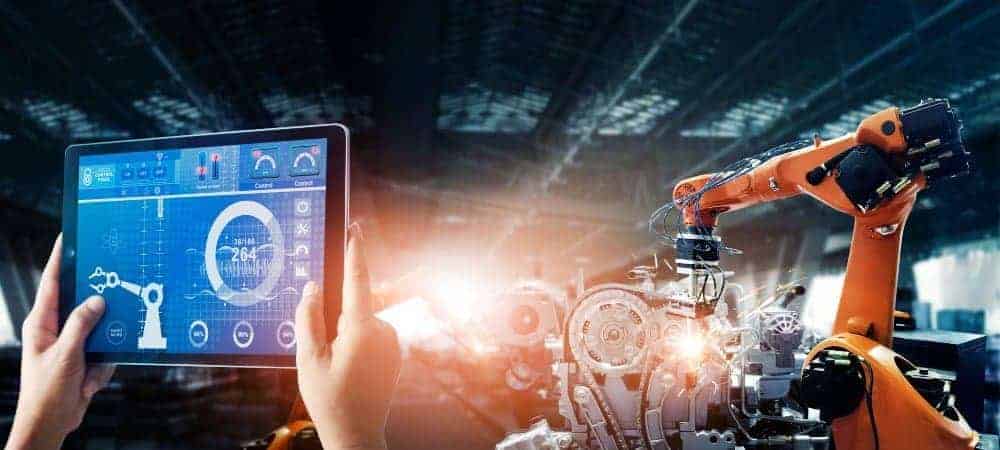
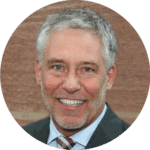
The MES deployment guarantees powerful single-part traceability, transparent visualization of manufacturing progress, and quality data collection to ensure the associated self-imposed standards.
Harald Ganster is the department head for store floor IT at Stihl and is responsible, among other things, for all production-related hardware and software systems. He describes his company's core requirements at the time for a new MES:
"At the time, the goal was to optimize our manufacturing processes so that extensive information on the devices produced was automatically captured.
In addition, we wanted to achieve more transparency for further optimization measures. With 23 assembly lines and high product diversification, it is also necessary for an MES to be flexibly adaptable to the conditions in production."
With the accumulated experience and requirements such as maximum flexibility, release security and transparent costing, they found what they were looking for. Ganster:
Industrie Informatik convinced us first and foremost with its unrestricted connectivity within the system landscape - including a certified SAP standard interface and QlikView connector. In addition, we were convinced by the comprehensive parameterizability within the standard of MES."
In 2016, the pilot operation with Cronetwork MES started on the first two of 23 assembly lines.
"At the assembly lines, we assemble our devices from several components in group work. The MES supports us here in recording and processing important process data.
A good example of this are torque values with which a blade is attached to the lawn mower. On the one hand, we already check the correct assembly at the workplace and, on the other hand, we are able to provide information to our customers at any time regarding important production parameters".
is how Ganster describes the added value of process data acquisition. Further possible applications from this and the associated individual part tracing have emerged over time.
Today, for example, serial numbers of the battery, charger and machine are married together in the case of battery-powered devices.
The classic advantages of machine and production data acquisition are almost a matter of course. Automatic quantity counting, including feedback to SAP, gives the foreman and the employees on the assembly line the necessary foresight for a wide range of optimization measures.
The "intermediate storage system" within production has been improved to the extent that stocks on the lines can now be kept as low as possible, while the required material is still available at the right place at all times.
Harald Ganster continues:
,,It was also important for us to largely relieve our foremen of manual terminal operation and to create time and space for their core tasks.
Today, for example, if a malfunction occurs on a line, the plant recognizes this and automatically goes to malfunction. In the past, this message had to be sent manually by the foreman. Today, he can take care of the basic troubleshooting during this time. The same applies to the notification of follow-up orders.
As soon as the current order has been delivered, the next order is automatically registered, the line switches to setup and only changes status again when the first unit of the next order has been packed. During this time, the employee is fully occupied with his core tasks, such as setting up and continuing the assembly work."
However, Stihl wanted to make the newly gained transparency through machine, operating data and process data acquisition available not only to the management, but also to the employees on the store floor. Screens on each assembly line serve as a source of information.
,,Whereas the information used to consist of a conglomerate of six different sources with outdated data, today, thanks to portal technology, we can generate individual dashboards and provide information collected from the MES in near real time."
says Ganster, who elaborates further:
Thanks to information on order progress, follow-up orders, hourly output, target and actual quantities, our employees can better prepare for setup work and material procurement, which results in shorter setup times, among other things.
In addition, the assembly workers also keep an eye on their current key performance indicator per assembly line. This is one of the influencing factors for the bonus calculation, which is carried out 100 percent with data from the MES. Consequently, the employees also look at good output and quality."