Paradigm shift—Why Manufacturing Needs Next-Generation Connectivity
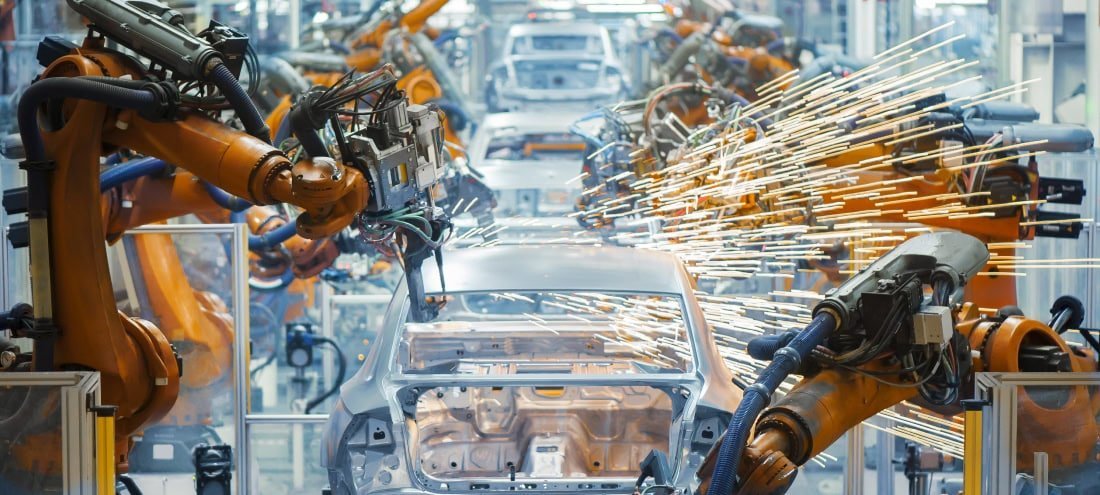
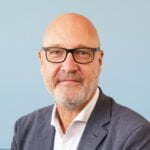
Value creation and supply chains can be organized in a more fail-safe way than before - through microservices and industrial mini PCs. In industry, value creation takes place in the factory. From a management perspective, this means that company management defines its strategic and financial goals, which ultimately have to be implemented on the store floor.
From a production manager's perspective, the goal is to organize a closed-loop problem-solving cycle through digital production control. Machines automatically report faults in real time, and teams of workers can take immediate action.
The success of each action is monitored using digitally recorded metrics. Lean management processes ensure that production is continuously optimized. Teams are empowered to analyze and correct errors independently. On the shop floor, the Excel spreadsheet still reigns supreme.
That’s all in theory. In reality, of course, many processes still look very different. Instead of digitally controlled automation, events are often still managed in Excel spreadsheets. According to ARC analyst Colin Masson: "Despite waves of innovation and consolidation, the typical industrial enterprise has a complex web of siloed applications held together by a kind of digital duct tape [...] the ubiquitous Microsoft Excel spreadsheet.
MES in vogue
This description of the current situation is in line with an analysis by research and markets, which predicts that the market for manufacturing execution systems (MES) will continue to grow strongly—by an average of 9.2 percent from 14 billion to 23 billion USD by 2029. The reason is the following: "The growth of this market is due to the increasing adoption of industrial automation in process and discrete manufacturing, the rising demand for operational efficiency, and the increasing complexity of manufacturing processes.”
Achieving operational efficiency in the face of increasing production complexity poses two key questions for production and IT managers. How can processes be optimized while production is running? How can you consolidate parallel IT structures into a single architecture?
SAP answers both questions with its cloud-based MES solution Digital Manufacturing (SAP DM), supported by a large partner network. The key is a successful overall process. The backbone for this is a "single source" IT architecture. With its various modules, SAP DM offers measurable benefits for every role in the company. These include easy-to-configure user interfaces; transparency through meaningful key figures and analyses; visual checks for precise decisions; seamless integration with the planning level (SAP/ERP); and increased profitability through improved quality and traceability.
Data must flow horizontally and vertically. As an SAP partner, our company brings shop floor connectivity to SAP DM. We always focus on the goal of creating a holistic problem-solving cycle. Comprehensive connectivity is the foundation for an end-to-end working architecture of transparent shop floor processes, optimized planning, and more efficient supply chains. The starting point is the most comprehensive horizontal and vertical networking of assets and IT systems.
The connectivity solution must be able to capture a wide variety of signals from machines, sensors, and tools and generate a standardized data model from them. Other systems, such as SAP DM, work with this data model to create transparency and efficiency through real-time and historical analysis of machine availability, consumption, quality, and traceability.
Further vertical integration of shop floor data with the top floor optimizes the management of orders, personnel, and invoices.
Shop floor management can take advantage of new opportunities. The IT world is changing rapidly; hardware is getting smaller and cheaper. On the software side, there are new opportunities with microservices, containerization, and Kubernetes. According to McKinsey experts: "The emergence of microservices heralds a paradigm shift from monolithic applications to a decentralized architecture."
Data streams and microservices
This paradigm shift also offers new opportunities on the shop floor: optimized data flows and more flexible IT architectures. The trick with microservices is to build them like standardized containers that can be easily combined and reassembled into new forms. Microservices are small, independent, and combinable software modules that can be used to create scalable applications. They enable a fundamental shift from monolithic to modular architectures.
The containerization approach allows microservices to be packaged into standardized and easily transportable units. Good for cost efficiency: more tasks can be distributed over less hardware. Open source frameworks such as Kubernetes act as a robust logistics instance on which containers and microservices are automatically orchestrated: which containers need to be where, in what order, and when? One Gartner expert joked: "Kubernetes plays Tetris with containers.
At this year's Hannover Messe, in Germany, we had the opportunity to showcase the prototype for next-generation connectivity at the SAP booth. It is called AC4DC. It represents an entirely new generation of software that addresses the paradigm shift toward microservices. The solution can significantly increase flexibility, scalability, and reliability in production. The most striking feature is that AC4DC runs on industrial mini-PCs. Users configure and operate the software centrally via the cloud. As a result, companies can manage machines around the world more reliably than before and ensure a secure flow of data from the machine level to management systems such as SAP DM.
What are the specific benefits of using AC4DC? Greater reliability, since mini PCs enable the cost-effective use of cluster technology. If a hardware component fails, a redundant Mini PC immediately takes over. In the event of a network failure, data is buffered and will not be lost.
Increased data security because the software runs on mini PCs that act as a gateway directly on one or more machines, it is possible to encrypt data close to the machine. This increases protection and security for highly sensitive data streams.
They are easy to connect. Factory teams centrally configure and manage the software via the cloud. Machines are connected through a central control center maintenance using standardized templates. This greatly simplifies installation and. Rapid scaling, as many mini PCs that can be centrally controlled from a control center in the cloud, enabling rapid scaling of machine connections. IEC standard signal interpretation is stored in a library for easy global scalability.
Fail-safe data streams are the foundation for flexible and resilient production. AC4DC combines software and hardware innovations in a "design to scale" solution. The goal is to ensure added value through improved availability and security for highly sensitive production data.
To the partner day:
