Plant Maintenance in the Course of Digitalization
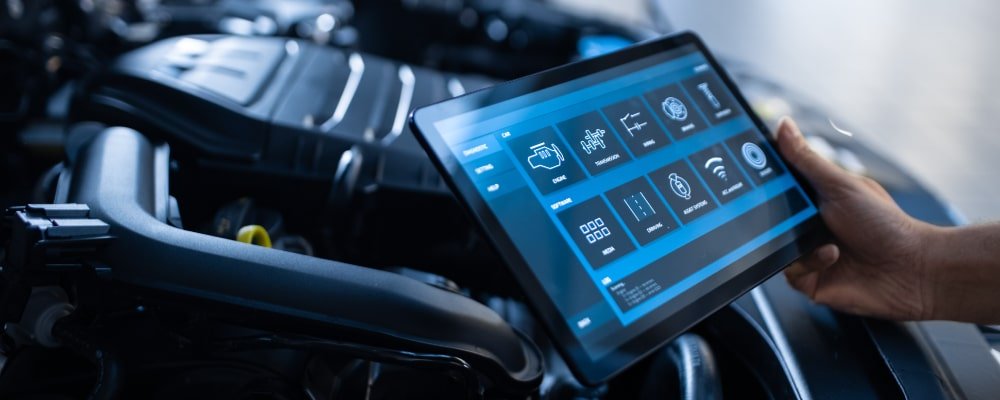
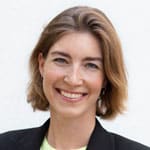
Maintenance staff are not IT professionals by nature. Of course they know how to use IT. However, a deep technical understanding of ERP systems, network technologies or databases is not part of the standard profile. Often this know-how is not even necessary. This is because many companies only use the rudimentary functions of the innovative technologies they have in place - or handle operational processes in the traditional way: the order is printed out and distributed, incidents and completed tasks are noted on paper, the data is transferred to the system and, if necessary, a log is scanned. Such a procedure takes a long time, is prone to errors and prevents employees from concentrating on their actual work.
Note disruptions in the shift log
Until recently, Deutz employees felt the same way. The company has stood for the development and production of innovative drive systems in the off-highway sector for around 160 years. As successful and up-to-date as the Group is overall, there was a long lack of consistency and user-friendliness when it came to fault management, which is so important for production. In housing production, faults were recorded in a shift book, i.e. on paper, and in engine assembly in an Excel spreadsheet. Finally, in crankshaft and camshaft production, where there had long been a PC at every workstation, the employee responsible entered the fault data into the SAP PM system (Plant Maintenance) via the SAP Fiori interface.
"One problem was that SAP PM was not really planned and designed from the perspective of a maintenance technician," says Hans-Günther Hensengerth, Head of Maintenance for component production and engine assembly at Deutz's Cologne plant. In addition, "the Fiori interface is not smartphone-compatible and therefore requires a PC".
Hensengerth's team therefore wanted a solution that would standardize, streamline and accelerate the process from fault reporting to maintenance - and motivate production to report every fault as quickly as possible. The ideal solution would be a maintenance front end that is user-friendly and can be operated via smartphone - regardless of location - with interfaces to data storage in the SAP system.
When looking for a new solution, one concern was that the introduction could consume unforeseeable capacities, especially for entering the data. With Mobile Maintenance from T.Con, the maintenance manager found the right system: "Firstly, the solution does not require any additional data storage outside of the SAP system. Secondly, the clear and intuitive user guidance appealed to us directly."
Nevertheless, there were doubts about the implementation. Internal discussions with the controlling department were particularly complicated and time-consuming. Originally, the maintenance manager and his team wanted to book and invoice each malfunction as a separate order, but his colleagues felt that this would have required too much monitoring. The solution to the conflict was to combine all malfunctions of one machine per month into one collective order.
And the maintenance staff also had to be persuaded. Some were afraid of too much control if the GPS connection of the technology meant that - theoretically - every trip to the bakery during working hours could be tracked.
Such concerns quickly disappeared as the benefits of the new technology became apparent to everyone. The early involvement of the works council, which was constantly informed about all the progress of the project, was certainly also helpful here. Hans-Günther Hensengerth installed two key users in each of the four departments in order to test the application and anchor its possibilities in the hearts and minds of the team for as long as possible. They spent two months familiarizing themselves extensively with the technology, then trained their colleagues and also acted as contact persons.
Status display of each message by the system
The T.Con solution, known internally as MoMa, went live at Deutz in April 2021 - and has been structuring the department's work extremely effectively ever since. For example, the control center immediately reports a malfunction in engine assembly to the maintenance department. The employees see it in the MoMa app on their smartphone and can assign the job to themselves, i.e. raise their hands, so to speak. Or the foreman distributes the maintenance tickets to his staff. The system supports him by documenting both the workload of each individual employee and the status of the fault reports.
This is achieved in a very clear way: If the app shows a wrench and a nut separately in red, the fault message has not yet been assigned to an employee. If the wrench and nut are combined and orange, this has been done. If the wrench is shown in green, the fault message has been completed. A red stripe next to the symbol indicates that the fault in question has brought the machine to a standstill - and must be rectified as a matter of priority. In addition, the foreman in charge can always see the order volume of each employee and can distribute newly displayed maintenance jobs accordingly.
Data quality and cost savings
It is also helpful that images can be stored in the app - for example to document transport damage to delivered parts. MoMa also shows the availability of spare parts. All the maintenance technician has to do is scan the QR code of the part in question and the app will inform them whether and where it is in stock.
The process described not only makes daily work easier. MoMa also improves data quality by documenting the history of each machine based on the malfunctions and displaying a detailed dashboard once a month showing how often maintenance was required and at what cost. The KPIs obtained from the fault analysis can be used to create an individual risk assessment for each machine. This makes the planning and execution of maintenance much more calculable than before. Maintenance manager Hensengerth particularly appreciates the fact that he can retrieve all the desired and necessary data via a single app - instead of having to click through several different applications.
In future, the app will also be used to process orders in the "Turning, milling and grinding equipment manufacturing" department. Example: If three clamping jaws are required for a milling machine, MoMa converts this request into an order with just a few clicks and sends it to the production equipment department.
A total of around 140 employees work with the system at the Cologne site and 40 at the small series and service plant in Ulm, where MoMa went live with fault recording last December. As soon as the maintenance plans have been entered into SAP, all maintenance in Ulm will also be handled via the app. The introduction is also set to take place in Herschbach in the Westerwald district, where Deutz operates a competence center for add-on parts such as power take-offs, valve controls and thermostat housings. MoMa was launched there at the end of March 2023; in the medium term, 20 to 30 people will be working with the system.
The bottom line is that Hans-Günther Hensengerth is highly satisfied with the new technology, which he calculates has not only given Deutz consistency, user-friendliness and greatly improved data quality, but also savings of around five percent.
Taking employees with you
When asked about the lessons learned from the project, he doesn't have to think long: First of all, you have to think carefully about which interfaces in the company are affected. It is a mistake to believe that such software only affects maintenance and controlling. Secondly, it is important to play with open cards vis-Ã -vis the works council from the outset and to involve the employees from the very beginning. "If half of the people are against such an introduction, it is very difficult to implement," says Hensengerth. The key users, colleagues who explain the technology to others, generate enthusiasm and answer questions when necessary, play a central role.