Into digital production!
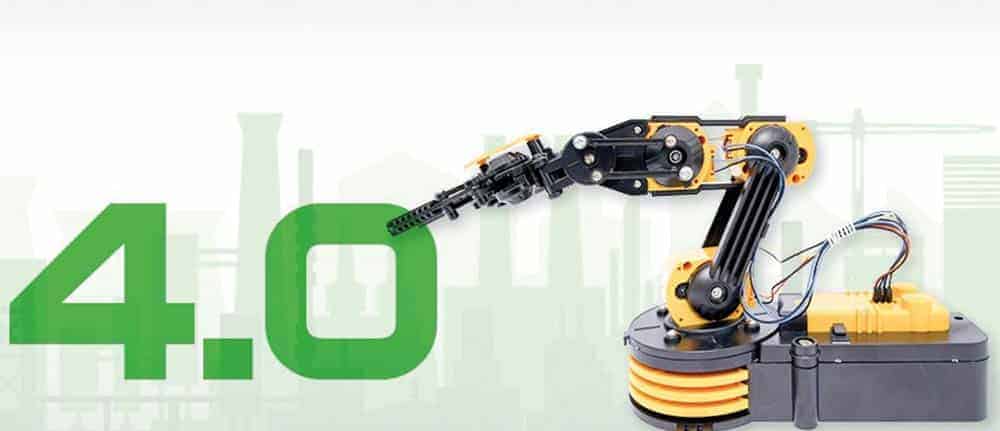

In order to remain competitive, manufacturers must develop and produce ever more complex and individualized products ever faster. Digital networking is therefore the dominant topic in the industry. The objective is to improve the interconnection of people, machines and products via digital systems.
But the truth is: Industry 4.0 is still merely wishful thinking for most German product manufacturers. At best, the vast majority have only taken the first steps toward digitization. This is demonstrated by our many years of experience as a software and IT specialist for the manufacturing industry.
But why is that the case? Why aren't these companies already much further along in terms of digitization and Industry 4.0? When they undoubtedly know that this will enable them to bring their products to market faster and in better quality, and thus increase their sales? It can't be down to the technical requirements either - they now exist.
The answer: In many cases, day-to-day business prevents faster digitization. A solution to the dilemma can therefore only be provided by determined corporate management. Only it can create the necessary freedom in everyday work to test and establish digital technologies.
And the widespread silo thinking in German SMEs can also be overcome exclusively by management. In many respects, different departments often work only for themselves - and this also applies to the selection of suitable software. For this reason, management should also understand overarching software systems as a management task.
Now the Corona crisis, of all things, could have ended the digital stagnation. Video conferencing, for example, has finally become established in many companies. Of course, digital work with Zoom, for example, is still a long way from digitization. However, the new digital normality could also make it clear to managers from the manufacturing sector that it can, and indeed must, work with less on-site presence.
The learning effect is reinforced by slumps in orders due to the crisis - painful as they are. The resulting overcapacities have created potential free spaces in which there was more time again for the pressing topic of digitization.
Forward-looking managers could use this time to evaluate the current situation. Then, almost inevitably, they had to draw a conclusion: In the future, it will be imperative to be able to work increasingly away from the real production environment. This inevitably includes a complete digital product model. We are convinced that this "digital twin" is the real core of Industry 4.0.
It contains all the information about the product, its manufacture and its condition along the entire value chain from development, planning and production to after-sales service. The properties and behavior of a product can be perfectly simulated by this digital image even before physical production. It is then only a small step to automating even complex production processes.
Digital transformation takes time
Ultimately, it does not necessarily take a crisis to drive digitization forward - but above all the slowly and thoroughly growing realization that manufacturing companies cannot survive in the long term without networked and self-learning systems.
That's why Industry 4.0 is not really an industrial revolution, but an evolution. Good thing! Because for most companies, comprehensive digitization means nothing less than a painful cultural change. And it's better to do it gradually than abruptly.