SAP master data management: automated and effective
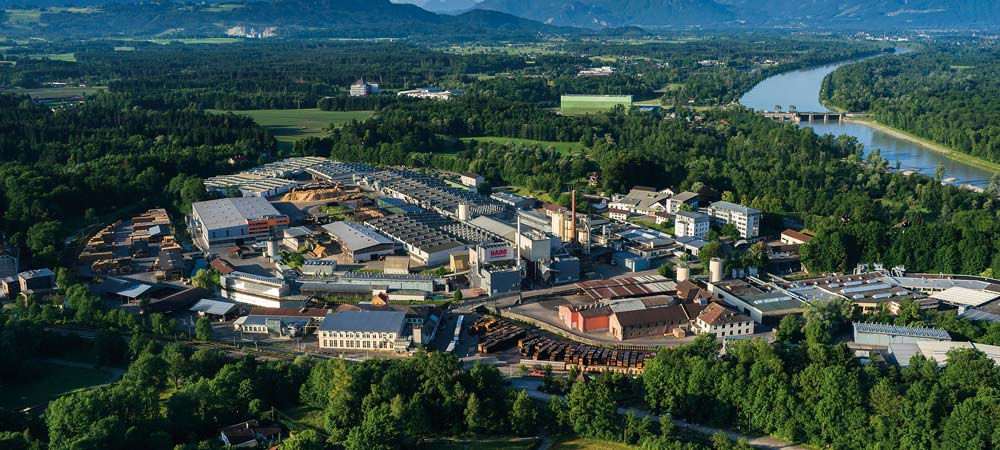
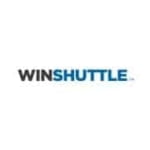
To achieve this, the use of application data management (ADM) software is recommended. The highlight here is that the departments themselves are the users and thus remain masters of their data.
Data has long been perceived as a strategic asset, but is usually not yet treated as such. Not only must data quality be consistently improved, but the volume of data, which generally grows exponentially with the size of the company, must also be taken into account. Without optimizing processes accordingly, competitiveness - and thus business success - will suffer. Business-critical data in particular must be brought into focus. A large part of this is master data. The lion's share of this is generated and/or modified in the specialist departments. This includes, for example, information on new materials or articles as well as on debtors and creditors, supplier, customer and personnel data as well as price conditions.
So why have the business department laboriously and largely manually prepare these master data creations and changes, which are then in turn entered into SAP manually or with the help of technical tools by the IT department? This can result not only in cost-intensive errors in downstream processes, but also in low productivity and incorrect reporting. The optimal solution is for business departments to close the gap themselves - automatically and without any SAP programming knowledge at all. How the biggest challenges associated with this can be overcome is described below.
Accelerate master data processes
Slow, manual master data processes can inhibit key processes such as ordering, asset maintenance, new product introduction, and supply chain operations. However, automating such processes has always been in the hands of specialized IT resources that were often already overloaded.
Today, professionals who certainly know their processes and data best can reduce cycle times by 50 percent or more using software designed specifically for them. The solutions are embedded in Microsoft Excel-based workbooks or web forms, eliminating manual data entry via the SAP GUI. In this way, they optimize master data management for every type of object - and not just for the "big four", i.e. material, customer, supplier and financial data.
Reduce duplicates
Duplicate master records cause a number of downstream problems and inaccurate reporting. New duplicates can be prevented by allowing agents to search existing records via web forms before creating new ones. Business users can also mark existing duplicate records for deletion based on Excel - cleaning up their own data and improving business operations.
Apply procedures and business rules consistently
If master data is maintained manually, procedures and business rules are often applied inconsistently. This results in poor data quality and unnecessary business risks.
However, with a forms and workflow-based solution, formal controls for data collection and release can be established that cannot be circumvented. Likewise, detailed business rules can be embedded to avoid data not being collected and thus missing. To do this, the required fields are created in the form - without having to be provided in the SAP system - data formats are standardized, and data is enhanced by using third-party web services for address validation or credit reports, for example. Documentation such as tax exemption forms or credit reports can also be stored in the workflow process, alongside the SAP data fields that are populated as part of the master data creation process.
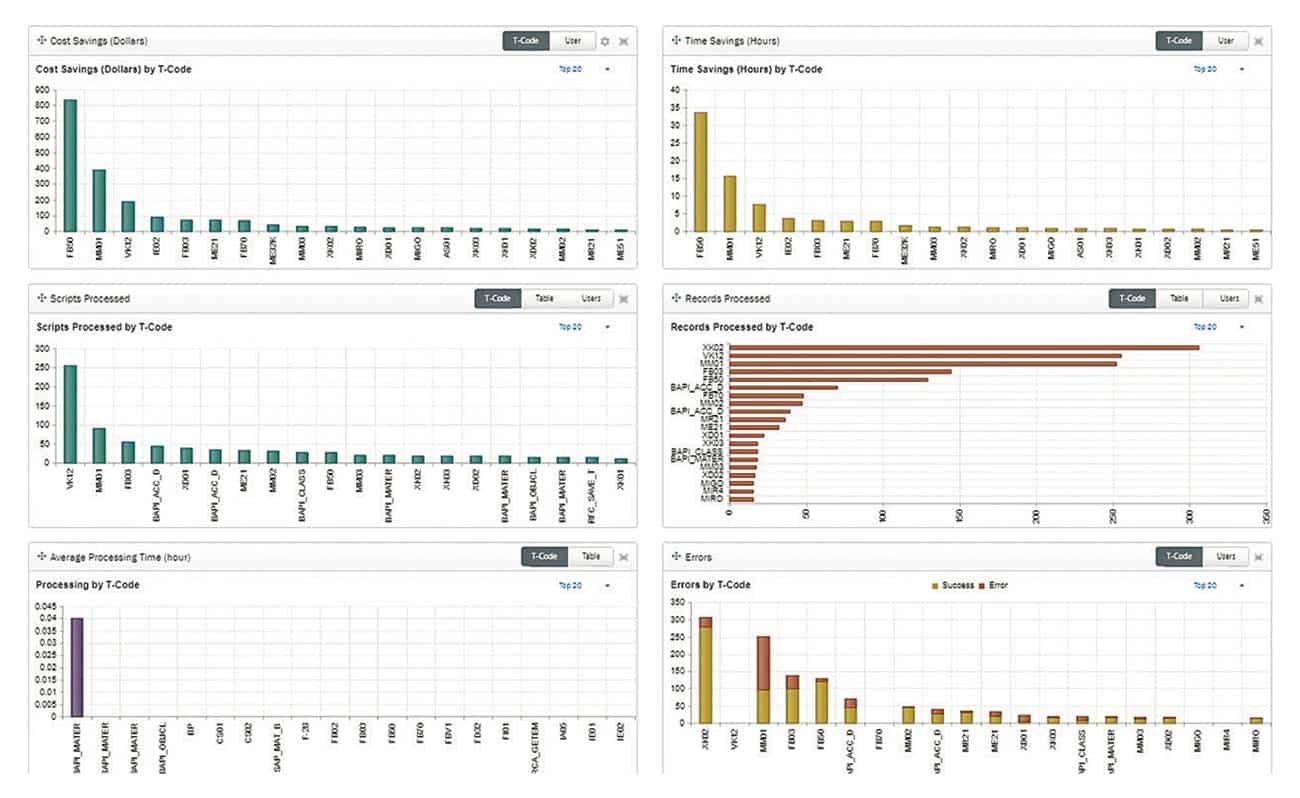
More insight into the status of master data requests
In the manual world, it's not easy to track the status of a master data request. Good workflow solutions ensure that agents are automatically notified or reminded of due or overdue tasks via email notifications or data collection forms.
Measure performance and optimize processes
Is it possible to determine exactly how long it takes to complete a master data request or whether the service level agreements (SLAs) have been met? With manual processes, probably not. But most master data management solutions automatically monitor key metrics around performance, such as savings in time, cycle times, data error rates and SLAs (see figure). Dashboards or other reporting capabilities help identify and resolve bottlenecks in the process as well as data quality issues.
Today, thanks to software from companies like Winshuttle, business users have the opportunity to overcome their most pressing challenges around master data, accelerate processes and significantly improve data quality. All of this has a long-lasting effect on the business. The following case study illustrates how and that this works in practice.
Standardization beats isolated solutions
Hamberger Industriewerke GmbH has been relying on Application Data Management (ADM) from Winshuttle since 2012 - and thus on automated processes in SAP data management. In this way, the company minimizes error-prone, time-consuming manual processes and benefits from completely digital processes and high data quality.
If data is to provide a valid basis for decision-making, it goes without saying that it must always be up-to-date and complete. The larger the data pool, the more important it is to have professional data management based on modern software. And if a company operates on a global level, this is virtually a must.
Hamberger Industriewerke GmbH, with its headquarters in Stephanskirchen near Rosenheim, also takes this approach to heart. With 2700 employees worldwide, Hamberger generates annual sales of around 325 million euros. The manufacturer of floor coverings and toilet seats attaches great importance to high data quality. For this reason, it began automating its data management with the help of Winshuttle software as early as 2012.
Creation and maintenance of master data of thousands of records
Due to market requirements, a four-digit number of material numbers had to be created each year. The number of characteristics to be maintained grew steadily, for example, due to the increasing importance of online trading. In addition, expansion necessitated the creation and maintenance of new master data and condition records for a large number of customers. In the case of successful takeovers of new store chains with hundreds of locations, it was often no longer possible to create the data manually in a timely manner as required by Sales. "Until then, our employees had laboriously entered all this data manually into the SAP ERP system we use. The departments had transmitted the necessary content to the responsible colleagues via Excel files or even in paper form," says Harald Dechant, DataWarehouse Architect, describing the procedure.
The error rate and the control and correction effort were correspondingly high, and they increased in parallel with the data volume. "For example, an incorrect price entry in fully electronic order processes could result in high additional costs," says Dechant. Since the volume of data will continue to grow as digitization progresses, a new IT-supported approach was recommended.
Hamberger had definite ideas regarding a software solution that would meet the following requirements:
- Acceleration and simplification of the above processes
- Easier management of increasing data volumes
- Reduced dependency on external consultants responsible for customizing workflows
- Standardization of processes and reduction of isolated solutions for individual application purposes or company divisions.
Automated data management processes
Hamberger found what it was looking for in an initial step in 2012 with "Winshuttle Studio". The Microsoft Excel-based software is used for the automated capture, completion and validation of data as well as its transfer to and from SAP. It was installed and ready for use within a few hours by the in-house IT department. Its operation is intuitive, so no training was required for the key users and they learned how to use the tool mainly autodidactically. In addition, the online tutorials, the support site and, in individual cases, employees of the ADM manufacturer's hotline helped.
"In 2018, we were then faced with the challenge of setting up a workflow for the material master plant," adds Manfred Zacherl, SAP module supervisor. "For this, we solicited offers from corresponding providers, but here too, Winshuttle was ultimately able to win the race with its 'Foundation Enterprise' platform." He cites the excellent usability, the significantly more extensive range of functions and the interface-free connection to SAP as reasons for the selection. In addition, the tool is suitable for all SAP transactions in all modules with a GUI interface, while other workflow solutions are usually tied to one module or even one transaction.
The platform, including the development and production environment, was implemented within a few days in November 2018 through teamwork between the manufacturer's support and the company's own IT base administrators. It makes it possible to automate all SAP-related processes through configurable workflows. Supported by sets of rules, the various departments can validate and approve the entries before they flow into SAP. In many cases, field contents are even filled automatically in the background due to the software's logic. This optimizes data quality and thus maximizes the ROI of the SAP investment. The key users were trained in the use of the system in a three-day workshop and have since been able to solve problems largely on their own.
Conclusion: Strongly accelerated processes
Hamberger uses both tools for all mass maintenance tasks. On the one hand, this includes the maintenance of - in view of the large variety of product ranges - extensive customer-specific condition records, material master changes, and the mass creation and maintenance of customer master data. The latter also includes the data of new customers, which is made available electronically. In addition, complete processes across multiple transactions have been automated. For example, order, delivery bill and invoice creation can be triggered with a single Winshuttle template in the case of store chain promotions. The ability to create characteristics and key figures when implementing the SAP BW/4HANA data warehouse is also very beneficial. The platform also provides valuable support for the replication of content from SAP R/3 as part of the planned switch to S/4HANA.
Overall, employees are very satisfied with the new way of working. In particular, the comparatively simple Excel-based operation is also rated positively by the specialist departments. The IT-based processes, instead of manual, monotonous activities, meet with a high level of acceptance, especially among young specialists.
Harald Dechant summarizes the advantages of the solution as follows. "We now benefit from greatly accelerated processes thanks to the 'first-time-right' principle. Likewise, we have been able to create more value-adding work content and thus make more meaningful use of the working time gained through automation. Data maintenance at our company has undergone a massive expansion towards a product information management (PIM) system, with all required and desired content consolidated on one platform." As a result, Hamberger has been able to replace its paper and slip-of-paper economy and is in the process of setting up completely digital processes. In combination with SAP BW/4HANA as the output medium, checking, correcting and completing data can be carried out as quickly as possible.
Based on the positive experience, the company plans to use the "Foundation" workflow solution to implement a wide range of requirements in all areas of the company in the long term. In the course of this, the software is to be used by around 200 users.
Hamberger will give a presentation on the use of Winshuttle software on September 18, 2019, from 5:45 p.m. to 6:30 p.m. at the DSAG Annual Congress at the NurembergConvention Center (NCC).