Yes, just make a plan ...
![[shutterstock:416135350, Have a nice day Photo]](https://e3magpmp.greatsolution.dev/wp-content/uploads/2014/02/shutterstock_416135350.jpg)
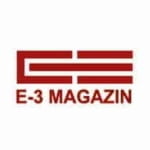
In the SAP–Community and especially with the ERP-veterans from the R/3-time, the legendary abbreviation APO is well known.
Several causes
The SAP module APO was a great challenge for the hardware and customizing from the very beginning; and the topic of production planning is not trivial with and without IT anyway - but it is crucial for success!
With a lot of effort, Advanced Planning & Optimization (APO) is now running successfully at the major SAP-Existing customers. The majority of SAP-but users come from the midmarket and upper midmarket.
Here, on the basis of SAP ERP, the products, solutions and knowledge of the SAP-partner in demand.
Björn Dunkel, Head of Sales & Marketing, will provide information on scheduling, planning and Excel. Marketing, Gunar Kunze, Head of Development, Anke Baier and Ulf Bauer, Development, and Oliver Schmelzer, Consulting (all from the SAP-partner G.I.B Gesellschaft für Information und Bildung mbH), in conversation with E-3 Editor in Chief Peter M. Färbinger Information.
Already Bertolt Brecht wrote in the Threepenny Opera:
"Yes, just make one plan, just be a big light, and then make a second plan, gehn they both do not."
The E-3 Editor in Chief asked Gunar Kunze, Head of Product Development at G.I.B in Siegen: What is the reaction at the SAP-Existing customers when you bring up the subject of planning?
"The interest in the topic of planning is usually there and also great. Of course the SAPIn addition, existing customers are constantly looking for solutions to meet their long-known and frequently discussed functional requirements.
Incidentally, this applies not only to the planning area, but to many other segments in which Add-on-vendors cavort."
And from the Practice is known that in many companies a standardized functionality in the area of production planning is also absolutely in the interest of IT.
"Because local solutions respectively MS Excel workarounds are hard to administrate".
Kunze adds.
"And often represent domination knowledge of individual employees."
But for many IT users at the PC, planning is synonymous with Excel. Is it allowed to be like that? What are the dangers?
"Well, Excel is first of all a very common software tool with high user acceptance"
says Gunar Kunze in an interview.
"SAP itself relies on Excel as the display and editing interface for some current developments. Also the function of the Excel export lies in the SAP-applications as a standard function.
For many applications, Excel is absolutely the right tool. In the case of production planning, where current data must constantly flow in and the results must also be available in the SAP-system must be kept up to date, a local Excel solution is the wrong way to go in our view."
While there may be good reasons for using Excel in the local area, SAP's Advanced Planning & Optimization often appears to be the solution for production planning.
"shooting with cannons at sparrows".
Is there a happy medium between Excel and APO? Or is that SAP-Module the only way out?
"No, we absolutely do not see the APO as the only way out"
contradicts development manager Kunze. There are definitely companies that are familiar with the planning tools in the SAPThe planning board is the most commonly used tool in the production planning process.
Other companies, on the other hand, decided years ago to introduce a nonSAP-planning software set. With massive interface effort for download and upload.
Such systems can also perform quite well.
"Our Dispo-Cockpit Planning, DCP, is of course a real alternative at this point"
Kunze knows from his professional Practice.
"Because the application offers a significantly higher level of performance compared to the SAP-Standard without APO with full integration into the SAP-system, i.e. without Interfaces-, hardware and administration overhead, offers."
Despite integrated SAP-standard software, the reality is heterogeneous. This does not have to be negative: A best-of-breed approach is sometimes promising.
Björn Dunkel, Head of Sales and Marketing at G.I.B, adds in an interview with E-3 magazine:
"A combination of APO and DCP can also be a successful model. Larger companies set the APO in the main plant, for example, and at the same time use the DCP in all other branches."
The fact is that G.I.B Dispo-Cockpit Planning and the APO with the SAP–ERP-system interact with each other. Both systems - APO and DCP - thus always access the same database and the results of planning from one system flow into the other system via this circuit, without APO and DCP communicating directly with each other.
For all the need for a powerful system like APO, the complexity and high administrative overhead are, by their very nature, also the downside of a system that attempts to solve almost all planning problems 100 percent of the time.
From the Practice knows almost everyone SAPIn addition, G.I.B. has found that the 80-20 rule is sometimes the better solution for day-to-day operations. What does G.I.B see as the main possible deficits in SAP APO?
"First of all, we can see again and again that APO is not in use in many companies, or at least not for production planning and production control"
Gunar Kunze explains the often surprising absence of an important planning tool. And where APO is in use at the central plant, the functions are often not to be rolled out to smaller plants in the company.
This is where a deficit or disharmony in planning sometimes arises.
"We clearly see the shortcomings of APO not in its functional performance, but in the resulting consequences for the introduction and operation of APO in manufacturing companies"
emphasizes Kunze, because often the APO functional scope is oversized for the individual company. This results in too high a price for the operation of the APO in the area of project runtimes, project costs, master data, Interfaces, Administration, Key User.
As a result, the company's acceptance rate drops. Gunar Kunze knows from experience that in this constellation, implementation projects often fail already in the decision phase, but sometimes also in the middle of the implementation project.
His colleague Björn Dunkel adds:
"APO's enormous scope of services makes the application very complex. Many users lack an overview and transparency. Especially when only individual sub-areas of APO are used.
This complexity is certainly one reason why some companies use the DCP in addition to the APO, ensuring greater transparency and ease of use."
Often, several, even parallel solutions are conceivable: But when does the SAP-The APO cannot be bypassed?
"Currently, functions are available in APO - and only in APO - that companies with complex interconnections within the supply chain cannot avoid"
defines Gunar Kunze. Examples include the functions of Global ATP (Available-to-Promise) or finite planning within a powerful MRP (Materials Requirements Planning).
Companies with such complex requirements usually also have a corresponding size and can therefore still most likely guarantee the prerequisites for operating an APO system.
"However, the smaller units of such companies do not necessarily have to benefit from APO functionalities"
Kunze adds.
At the other end is Microsoft Excel: Many companies are used to exporting Excel lists from APO for further processing. What alternatives are there to this? G.I.B Development Manager Kunze:
"When we talk here about the result of production planning in APO, we are mostly talking about information on production execution in the form of order lists, machine allocation plans, etc. Alternatively, one can certainly use functions of the SAP-standard, after the order data has been transferred from the APO to the R/3 were handed over.
Under this condition, however, our Dispo-Cockpit Planning is also a real alternative for preparing order data and presenting it in a bite-sized form for the production areas.
Our DCP can therefore support not only the planning but also the execution of the manufacturing process with information and functions. By the way, such a scenario is successfully in use at one of our existing customers."
Planning has always been a part of the G.I.B Dispo cockpit. Now G.I.B has extended the planning part using object-oriented Programming with ABAP Objects rewritten (see also box). What was missing functionally before, what is new now?
"The DCP initially pursued a simplified planning approach according to the motto: "The necessary as before in Excel simply, quickly, but just integrated in the SAP-process system." These are the benefits many companies want to secure"
knows Anke Baier, who has accompanied the Planning Module at G.I.B since its beginnings, and explains:
"At the same time, there is a desire to implement the more complex planning requirements with the DCP.
We have now responded to this with the 'new' Planning. We are thus following the needs of our customers."
The main innovations and enhancements are the simultaneous planning of several workstations and the possibility to display different planning versions.
The newly created option of creating special planning scenarios, such as slot or interval planning, should also be emphasized. In addition, the DCP offers automated scheduling proposals.
Especially important and convenient for the planner are the simulation options with the help of planning scenarios. Of course, the "new" Planning also offers user-friendly and clear information with the help of the dashboard, despite the enormously expanded scope of services.
G.I.B says that planning can also be simple and user-friendly. Is the traditional planning board a dead end?
"We say that the user must keep the chance to understand the behavior of his planning tool"
Baier emphasizes.
"In addition to comprehensible functions, we also want to provide our users with a high degree of usability to cope with their daily work. Both goals can only be achieved if the range of functions and information content meet the individual requirements of the planning workstation. Traditional planning boards usually suffer from a lack of information content.
Detailed information cannot be accommodated on, for example, one centimeter of displayable graphic area for a production order. In other words, traditional planning boards cover exactly one functional goal, namely the more or less manual sequencing of orders while taking available resources into account.
Our DCP, on the other hand, with its cockpit mindset, also covers all the adjacent tasks of a work preparer."
When discussing traditional planning boards, it is not far to the question: How do we succeed in combining user-friendliness and familiar SAP-User interface design into one concept? After the functionality comes the question about the GUI:
"We set our own standard for the surface design of our products years ago, but we definitely lean heavily on SAP on so that the SAP-user immediately feels at home in our cockpit".
Kunze explains his development work.
"We achieve user-friendliness with various tools. Our G.I.B RAC, Role Administration Cockpit, enables role-based or activity-oriented work with the Dispo Cockpit.
Individual users are thus offered only the information and functions they need to perform their jobs."
This approach defuses the overall complexity of the application for the individual user.
Flexibility and individualism are achieved by the G.I.B software with extensive user settings in combination with a function manager.
From the Practice How detailed should a plan be? With APO, you can plan in almost any depth. How do G.I.B's existing customers work?
"The first thing to keep in mind is that planning is usually the desirable theory, but is often affected by unplanned events of the Practice torpedoed.
Planning must therefore also take into account aspects of Practice such as average downtime of a machine sufficiently take into account".
Gunar Kunze knows from his professional Practice.
The level of detail of the planning may only be so high that the production can follow the planning exactly. For example, at a G.I.B Automotive customer, each assembly line is planned with shift precision with orders exactly in shift quantity.
The DCP runs on the line in display mode and is used, among other things, for timely feedback and material supply functions of the assembly line.
At another customer, the work preparation department defines a weekly production program and passes it on to the foreman departments. This procedure could be called rough-cut planning.
In the production area, the sequence of processing is planned. The DCP is used for both steps. The intuitive handling of the planning in the G.I.B Dispo-Cockpit is an essential success factor for the user.
To what extent do complicated handling and inflexible configuration definitions lead to poor planning results? Oliver Schmelzer from G.I.B Consulting can answer this question from the Practice report:
"With many solutions, there are predefined displays and setting options. In addition, important information is not directly accessible and makes planning more difficult. Standardized industry solutions are also widespread.
However, the problem here is that the processes shown are not the same in every company. The Dispo-Cockpit Planning, on the other hand, is structured like a construction kit.
Together with our customers, we identify the optimal key figures and parameters and adjust the module so that all relevant processes are mapped optimally and company-specifically".
Schmelzer explains his work.
"This gives the customer a customized planning board and usually no additional customization development is required, which yields surprisingly short implementation times."
For which industries and company sizes is the G.I.B solution offering suitable?
"Originally, the development of the G.I.B Dispo cockpits directly aligned with the requirements and processes of the manufacturing industry."
Björn Dunkel explains.
"The automotive and steel processing sectors in particular still represent a major pillar of success today."
And the marketing manager adds in the E-3 conversation:
"However, our Dispo Cockpit has grown enormously over the years and, of course, so has our know-how.
Today, with the five modules of the G.I.B Dispo-Cockpit, we cover large parts of the value chain and are constantly opening up to new topics such as In-memory Data Management and Vendor Managed Inventory.
Our range of industries has also expanded; in addition to the pharmaceutical and beverage industries, our customer portfolio increasingly includes customers from the retail sector. We are opening ourselves up to new exciting challenges, but always with quality assurance in mind."
Who is usually involved in a SAP–ERP- and business suite customers responsible for the topic of planning in the production and manufacturing environment? Who is G.I.B addressing with the new planning solution?
"In our sales and customer situations, we encounter, on the one hand, dispatchers who are also responsible for their assortment in the manufacturing environment.
A second group are the classic work planners and production controllers, who act downstream of the scheduling department, plan the production sequences and ensure their implementation together with the responsible forces in the production areas."
Kunze concludes by defining the potential users of Dispo Cockpit Planning.