Cockpit für das Projektcontrolling
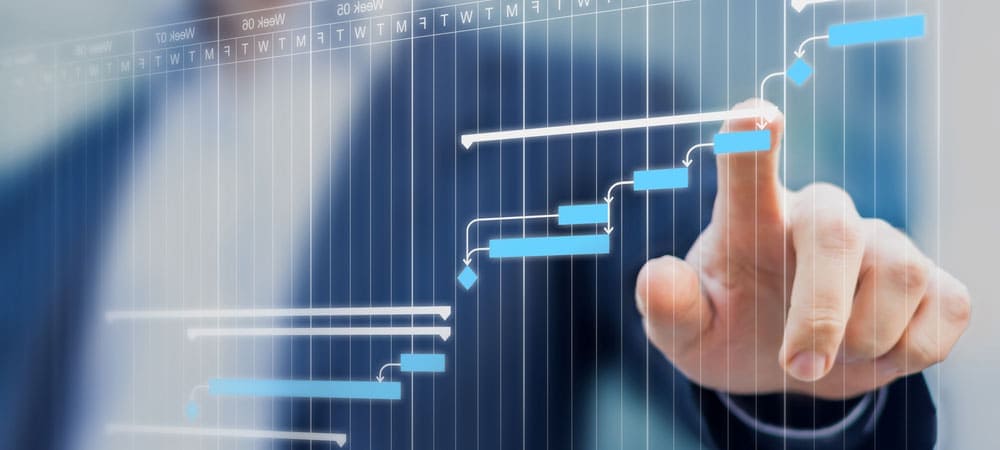
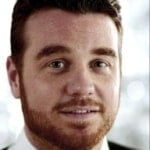
Produktionsprozesse werden immer anspruchsvoller
Das Projekt-Business, bei dem Produktionsanlagen nach den individuellen Anforderungen eines Kunden gefertigt und vor Ort installiert werden, ist ein Standbein der Kuka-Gruppe. Von der Erteilung eines Auftrags bis zur Inbetriebnahme einer Anlage kann es auch schon einmal mehrere Jahre dauern; die Kosten belaufen sich in der Regel auf mehrere Millionen Euro. „In den zurückliegenden Jahren hat die Komplexität der Projekte noch einmal immens zugenommen“, sagt Wilhelm Keppeler, Head of Project Management Office (PMO) Division Industries bei Kuka. „Das hängt vor allem damit zusammen, dass die Produktionsprozesse unserer Kunden – beispielsweise Automobilhersteller – immer anspruchsvoller werden. Für uns hat die steigende Komplexität dazu geführt, dass wir beim Projektcontrolling an Grenzen gestoßen sind.“
Projektcontrolling
So aktualisierten die Projektleiter ihre Reports zwar regelmäßig. Den Stand eines Projekts in Echtzeit abzurufen, war aber nicht möglich. Außerdem wurde nur ein Teil der grundsätzlich verfügbaren Daten zu Kennzahlen verdichtet. Die generierten Kennzahlen waren nur teilweise visualisiert. Um das Projektcontrolling zu verbessern, entschied sich Kuka 2019 dafür, das Thema neu aufzusetzen.
Oliver Kalka, Senior Manager bei MHP: „Wir sind schon seit vielen Jahren Partner von Kuka und haben bereits einige IT-Projekte gemeinsam realisiert. Daher war es naheliegend, dass die Verantwortlichen von Kuka als Erstes mit uns über ihr Vorhaben beim Projektcontrolling gesprochen haben.“ Zum einen erarbeiteten Mitarbeitende von Kuka einen neuen Prozess für das Multi-Projekt-Management und bauten ein neues Kennzahlensystem auf. Ziel war dabei, sich von einer vornehmlich ökonomischen Sicht zu einer ganzheitlichen Sicht weiterzuentwickeln, welche die Dimensionen Finanzen, Zeit und Leistung (Qualität) integriert. Zum anderen wurde eine individuelle Analytics-Lösung entwickelt, die exakt zu den funktionalen Anforderungen von Kuka passte und sich in die bestehende Systemlandschaft integrieren ließ.
Den Kern des Smart Intelligence Robotic Project Cockpits – so der Name der Applikation – bildet das Data Warehouse SAP BW on Hana, das schon seit einigen Jahren bei Kuka im Einsatz ist. Hier wurden in Abap und mittels Rapid Prototyping drei aufeinander aufbauende Schichten umgesetzt. Die erste Schicht dient dazu, Daten aus unterschiedlichen Modulen von S/4 (FI-, CO-, PS-Daten sowie mitlaufende Kalkulationen) in Echtzeit abzurufen und zu harmonisieren. Erforderlich ist diese Harmonisierung zum einen, um die Daten aus den unterschiedlichen Modulen zu vereinheitlichen. Zum anderen sollen so die individuellen Angewohnheiten der Projektleiter bei der Erfassung von Daten ausgeglichen werden. Aus den aufbereiteten Daten berechnet die Calculation Engine als zweite Schicht eine Reihe von Kennzahlen zu Finanzen, Zeit und Leistung. Dazu gehören beispielsweise die Material Ratio oder die Percentage of Completion.
Oliver Kalka: „Bei der Umsetzung der Calculation Engine kam es nicht so sehr darauf an, besonders elaborierte mathematische Verfahren zu implementieren. Die Kunst bestand vielmehr darin, in den verschiedenen Modulen von S/4 die richtigen Daten zu finden und damit aussagekräftige Datenmodelle aufzubauen.“ Als dritte Schicht gleicht die Monitoring Engine die errechneten Kennzahlen kontinuierlich mit den Soll-Werten ab und meldet mit dem täglichen Statusbericht Entwicklungen in Bezug zum Vortag und Differenzen zu kritischen Schwellwerten.
Visualisierung mit Add-on
Für eine ansprechende Visualisierung der Ergebnisse wurden mithilfe von QlikView, Qlik Sense und Qlik NPrinting unterschiedliche Sichten realisiert. Das Portfolio-Dashboard gibt einen Überblick über sämtliche laufende Projekte und zeigt die jeweiligen Meilensteine an. Außerdem signalisiert eine Ampel, in welchen Projekten alles rundläuft und wo es kritisch wird. Einen detaillierten Blick auf einzelne Projekte bietet das Projekt-Dashboard. Hier stehen zum Beispiel Finanzdetails mit einer Darstellung sämtlicher Cashflows, ein Gantt-Projektplan, der unter anderem eine Simulation von Soll-Ist-Abweichungen ermöglicht, und eine Time-und-Budget-Übersicht, die Abhängigkeiten hervorhebt, zur Verfügung.
Mittlerweile ist das Cockpit seit 2020 im Einsatz. Und das sehr erfolgreich. Wilhelm Keppeler: „Das neue Cockpit hat uns die erhoffte Transparenz verschafft. Beispielsweise können wir heute jederzeit nachvollziehen, ob wir in einem Projekt so weit sind, wie wir sein sollten. Falls nicht, können wir direkt reagieren und zum Beispiel zusätzliche Ressourcen einplanen. Natürlich wird dann auch unmittelbar ersichtlich, wie sich das auf die Finanzen oder eventuell auf andere Projekte auswirkt.“ Insgesamt hat die gewonnene Transparenz Kuka dabei geholfen, die Projektsteuerung auf ein neues Level zu bringen.
Keller und Knappich Augsburg
Ursprünglich einmal war Kuka ein Telegramm-Kürzel und stand für Keller und Knappich Augsburg. Heute ist Kuka eine Marke, die weltweit für intelligente Automatisierungslösungen steht. Bekannt ist das Unternehmen, das 1898 von Johann Josef Keller und Jakob Knappich als Acetylengaswerk in Augsburg gegründet wurde, jenseits der Industrie vor allem wegen seiner orangefarbenen Roboter. Zum Produkt- und Leistungsangebot gehört aber noch einiges mehr: von Fertigungsmaschinen für verschiedene Anwendungen über fahrerlose Transportsysteme bis zu vernetzten Produktionsanlagen. 2021 erwirtschafteten die circa 14.000 Mitarbeitenden damit einen Umsatz von 3,3 Milliarden Euro.