Die Mischung aus Technik und Organisation macht‘s
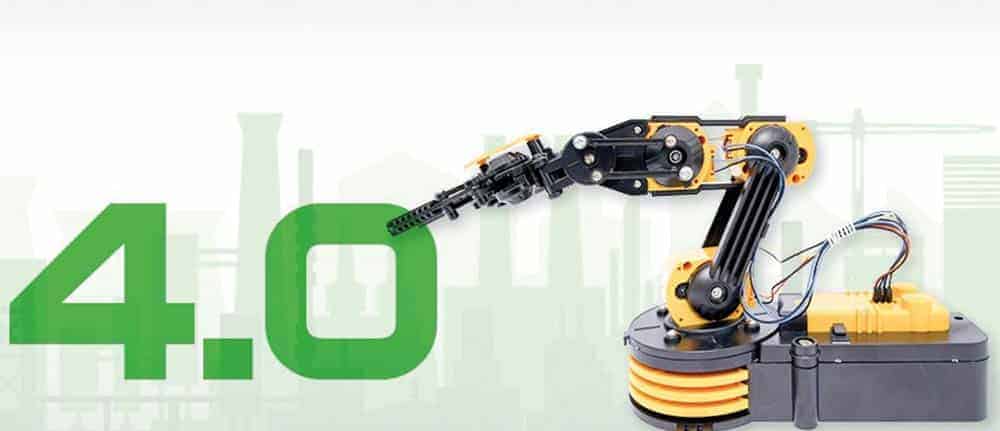
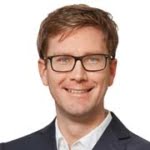
Das Thema Industrie 4.0 hat für deutsche Unternehmen hohe Priorität. Viele erwarten dadurch einen Wettbewerbsvorteil gegenüber der Konkurrenz, niedrigere Produktionskosten und sinkende allgemeine Kosten.
Bisher hat jedoch nur ein Fünftel der Unternehmen erste Projekte realisiert, wie die IDG-Studie „Industrie 4.0 – wo steht Deutschland“, zeigt. Doch Abwarten ist hier die falsche Strategie.
Jedes Fertigungsunternehmen kann von Industrie 4.0, also dem Industrial Internet of Things (IIoT), profitieren. Zum Vergleich: Anfang des 20. Jahrhunderts hat man sich gefragt: Für welchen Kutschereibetrieb lohnt sich ein Verbrennungsmotor?
Dessen durchschlagender Erfolg hat diese Überlegung schnell überflüssig gemacht. Genauso müssen wir heute das Thema Industrie 4.0 betrachten. Es ist die Pflicht eines jeden Unternehmens und liegt in seiner betriebswirtschaftlichen Verantwortung, sich mit den neuen technologischen Möglichkeiten auseinanderzusetzen, um die eigene Wettbewerbsfähigkeit zu sichern. Alles andere wäre fahrlässig.
Die Basis für ein erfolgreiches Industrie-4.0-Projekt bilden neue, disruptive Technologien. Doch alles, was ein Abweichen von bewährten Erfolgsmustern erfordert, sorgt für Skepsis – gerade in unserem traditionsreichen und florierenden Industriesektor.
Viele Entscheider schrecken davor zurück, Maschinen, ja ganze Fertigungsstraßen umgestalten oder elementare Produktionsprozesse stören zu müssen. Jeder Eingriff, jede Anpassung bedeutet ein Risiko, das kalkuliert werden muss.
Dabei können Unternehmen ganz einfach den ersten Schritt machen, indem sie nutzen, was sie bereits haben: ihre Daten. Diese zu sammeln, zu analysieren und in Mehrwert zu verwandeln – darum dreht sich jedes Industrie-4.0-Projekt. Beinahe jede Maschine generiert durchgehend Daten.
Wer diese nutzt, kann seine Investitionskosten im ersten Schritt entsprechend gering halten. Sind Anlagen noch nicht mit Sensoren ausgestattet, kann man dies mit einem sogenannten Retrofitting nachholen, um so den Mehrwert der vernetzten Anlage zu ermitteln.
Zudem stehen mittlerweile zahlreiche Tools zur Verfügung, um den vorhandenen Datenschatz einfach zu heben. Mithilfe spezialisierter Lösungen können Unternehmen etwa SAP-Daten auf Knopfdruck automatisiert auslesen und für Datenanalysen nutzbar machen – ganz ohne manuelle Bearbeitung oder zusätzliche Programmierarbeiten.
Über zertifizierte SAP-Schnittstellen werden die benötigten Daten aus verschiedenen Quellen in einem zentralen Data Lake zusammengeführt und stehen dort für die gemeinschaftliche Auswertung bereit.
Aber die Technik ist nur die halbe Miete. Um die Verschmelzung von Informationstechnik (IT) und Operativer Technologie (OT) zielführend voranzutreiben und verborgene Potenziale zu identifizieren, müssen Unternehmen Experten beider Bereiche zusammenbringen.
Gemeinsam sammelt dieses interdisziplinäre Team Ideen für digitale Optimierungen, erörtert deren Machbarkeit und wählt ein bis zwei Ideen aus, die weiterentwickelt werden sollen. Ziel ist, in kurzer Zeit einen funktionierenden Prototyp zu erarbeiten, der später einfach skaliert werden kann.
Der Schlüssel für die erfolgreiche Zusammenarbeit im IIoT-Projektteam ist, agil zu entwickeln und dabei auf den größtmöglichen Kundennutzen abzuzielen, wie es auch Start-ups tun. Die Projektmanagement-Methode Scrum etwa ermöglicht einerseits Flexibilität, andererseits aber ein sehr strukturiertes, zielgerichtetes Vorgehen. Start-ups haben naturgemäß wenige Ressourcen, wodurch sie extrem erfinderisch sein müssen.
Kurze Kommunikationswege unterstützen außerdem ein pragmatisches Vorgehen. Diese Eigenschaften sind auch bei Industrie-4.0-Projekten sehr wichtig. Anders als Start-ups verfügen etablierte Unternehmen zusätzlich über eine breite Mitarbeiterbasis, ein Netzwerk, langjährige Erfahrung und gewachsenes Know-how. All dies sollten sie ausspielen – und dann wie ein Start-up sehr kundenorientiert und zielgerichtet agieren.