Interoperabilität im Shopfloor: Reibungsloses Zusammenspiel aller Lösungen in dezentralen IT-Architekturen mit Orbis DSP
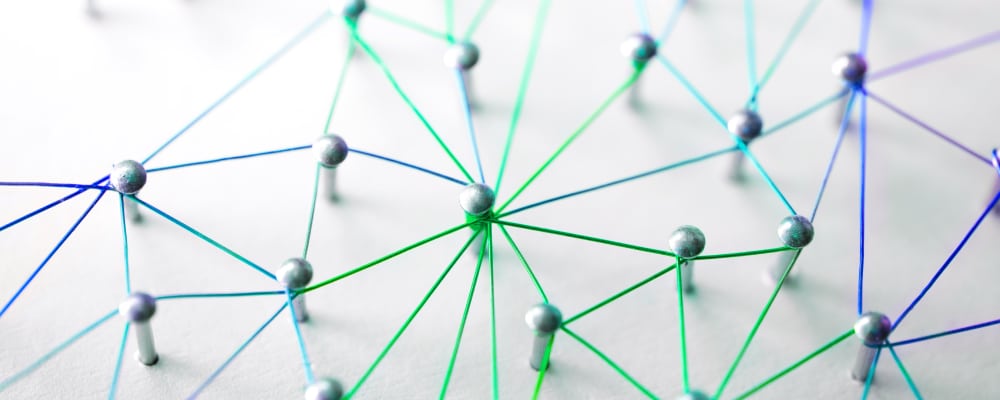
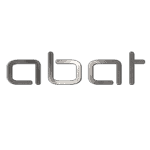
Doch das funktioniert nur, wenn die Interoperabilität aller beteiligten IT-Systeme in einer solch dezentralen IT-Landschaft gewährleistet ist, vom Shopfloor bis in das ERP-Back-End. Die innovative Lösung Orbis Distributed Shopfloor Processing (DSP) macht das möglich und schafft zugleich die Basis für mehr Prozessexzellenz und -effizienz. Die Fertigungsindustrie hat dank Automatisierung und durch den Einsatz von Methoden wie Lean Management die Shopfloor-Prozesse in den letzten Jahren spürbar effizienter gemacht und die Geschwindigkeit und die Leistung der Anlagen deutlich erhöht. Doch das Potenzial im Produktionsbereich ist noch lange nicht ausgereizt.
Ganzheitliche Optimierung
Moderne Technologien wie das Industrial Internet of Things (IIoT), intelligente Sensoren (Sensor Intelligence Devices, SID), Cloud-Computing, künstliche Intelligenz (KI) und Big-Data-Analytics ermöglichen eine ganzheitliche Optimierung im Sinne von Industrie 4.0. Eine Studie von Deloitte, „The Fourth Industrial Revolution. At the intersection of readiness and responsibility“, für die über 2000 C-Level-Entscheider in 19 Ländern befragt wurden, bestätigt die hohe Bedeutung der einzelnen Technologien für eine Optimierung der Produktion, an deren Ende die Smart Factory steht.
Die intelligente Fabrik vernetzt alle an der Produktion beteiligten Akteure digital und in Echtzeit: die Menschen, also Hersteller, Kunden, Zulieferer, den Maschinenpark, die Geräte, Sensoren, Aktoren und natürlich auch die IT-Systeme. Das schafft die Flexibilität, die im Hinblick auf die zunehmende Individualisierung – Stichwort Losgröße eins –, ständig wechselnde Kundenanforderungen und volatile Lieferketten für eine adaptive Fertigung benötigt wird. Es versteht sich dabei von selbst, dass in einer vernetzten Fertigung die Produktions- und Steuerungs-Systeme auch bestmöglich gegen IT-Angriffe abgesichert sein müssen.
Manufacturing-Execution-Systems
Um die damit verbundenen Herausforderungen zu meistern, geht der Trend zur dezentralen IT-Architektur, in der die SAP- und Shopfloor-Prozesse sowie die Datenspeicherung voneinander getrennt werden. Sofern es sinnvoll ist und Mehrwert verspricht, wird das ERP-Back-End (S/4 oder ECC) nach dem Best-of-Breed-Ansatz durch Cloud-basierte Services auf unterschiedlichen Plattformen, Low-Code-Apps oder Analysetools anderer Anbieter erweitert. Voraussetzung für den Aufbau einer Smart Factory und einer digital vernetzten Wertschöpfungskette, in der die Daten und Aktivitäten aus dem Shopfloor nahtlos mit ERP-Prozessen verknüpft sind, ist der Einsatz eines modernen Manufacturing-Execution-Systems (MES). Es fungiert als zentrale Drehscheibe zwischen den Daten aus der Fertigungsebene und den betriebswirtschaftlichen Anwendungen wie S/4 oder ECC.
Im SAP-Umfeld lässt sich diese vertikale Integration von Daten und Prozessen, zum Beispiel bei Instandhaltung und Qualitätsmanagement, unter anderem über die SaaS-Cloud-Lösung SAP Digital Manufacturing herstellen oder über das in der Praxis vielfach bewährte, SAP-basierte Orbis Manufacturing Execution System (MES), das sich nahtlos in S/4 Hana bzw. ECC 6.0 integriert. Viele SAP-Kunden nutzen aber auch das MES eines Drittanbieters, zum Beispiel weil es auf ihre speziellen Anforderungen in Bezug auf Fertigungsart, Produktionstyp oder Branchenfokussierung zugeschnitten ist. Laut dem vom MES-D.A.CH-Verband herausgegebenen „Marktspiegel MES 2022/2023“ gibt es allein in Deutschland rund 180 MES-Anbieter, die ein in SAP integriertes MES oder Drittlösungen nutzen.
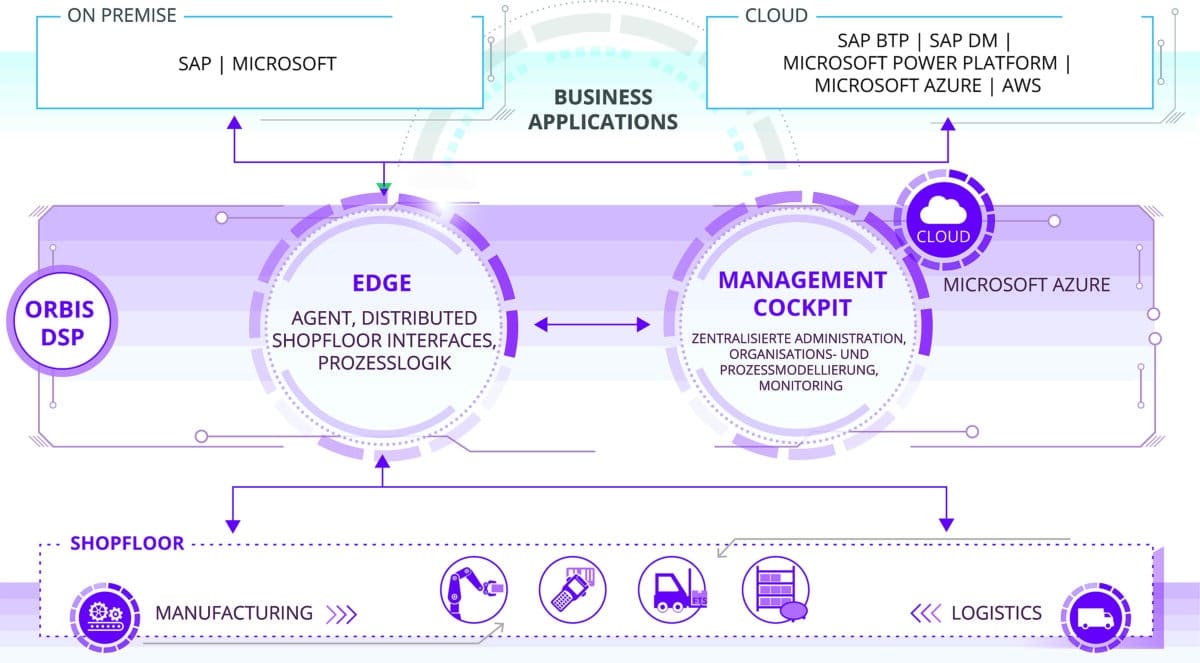
Interoperabilität im Shopfloor kennt viele wichtige On-prem- und Cloud-Komponenten, die Orbis perfekt orchestriert.
Industrie 4.0 nutzt Interoperabilität
Die Vernetzung und der Datenaustausch zwischen verschiedenen Systemen, Maschinen und Geräten werden dabei in der Regel durch Kompatibilität oder auf Basis von De-facto-Standards hergestellt. Um den Maschinenpark und alle für einen Prozess relevanten Komponenten in einer dezentralen IT-Landschaft zu verknüpfen, braucht es jedoch Interoperabilität auf Basis offener Standards. Sie ist der Schlüssel, der es ermöglicht, Daten zwischen Shopfloor, Back-End und Cloud-Plattformen automatisiert und reibungslos bidirektional auszutauschen und einen digitalen Zwilling zu erstellen. Interoperabilität ebnet damit auch den Weg für eine vernetzte, adaptive Produktion, die sich mithilfe von KI-Datenanalysen in Echtzeit (Machine-/Deep-Learning) flexibel anpassen und laufend optimieren lässt.
Hier setzt die von Orbis entwickelte innovative Lösung Distributed Shopfloor Processing (DSP) an, die das bewährte Orbis MES veredelt und erweitert und bereits bei mehreren Kunden im Praxiseinsatz ist. DSP harmonisiert die Anbindung von Maschinen werksübergreifend und kann dank offener Standards mit jeder beliebigen SAP- oder Non-SAP-Back-End- oder -SaaS-Cloud-Anwendung verknüpft werden und Informationen mit ihr austauschen.
Die Interoperabilität und die Plattformunabhängigkeit von Orbis DSP stellen einen echten Mehrwert für die Kunden dar. Die Lösung lässt sich in Verbindung mit Low-Code-Apps auf Basis von Microsoft Power Platform oder SAP BTP mit SAP Build, SAP Digital Manufacturing, Orbis MES oder einem Non-SAP-MES nutzen und ist unabhängig von der Public-Cloud-Plattform des Hyperscalers, in der die Anwendungen laufen. Die zentralen ERP- und MES-Prozesse treffen auf dezentrale Prozessbausteine im Shopfloor. Technisch gesehen besteht Orbis DSP aus zwei Komponenten, die größtmögliche Interoperabilität und Flexibilität gewährleisten: aus einer Edge-Lösung (Edge Node) und dem SaaS-Cloud-basierten Management-Cockpit.
Lokale EDGE-Komponente
Die plattformunabhängige Edge-Lösung wird lokal in einem Netzwerk oder in der Netzwerkperipherie installiert. Dabei spielt es keine Rolle, ob es sich um einen Windows- oder Linux-Server, einen Industrie-PC oder einen (Docker-)Container handelt. Das sorgt für hohe Konnektivität und kurze Latenzzeiten. Die native Verknüpfung mit den Produktionsanlagen, aber auch mit den Back-End-Systemen, egal ob ERP, MES, Analytics-Tool oder Cloud-Plattform, erfolgt über sogenannte Asset Units. Alle marktbekannten Protokolle werden nativ oder per OPC-UA unterstützt.
Über Agenten und Router stellt die Edge-Komponente die Verbindung und die Kommunikation mit dem Cloud-nativen Management-Cockpit her. Es wird in den TÜV-zertifizierten deutschen Rechenzentren der Blue Stec betrieben, die zur Orbis-Gruppe gehört, und läuft somit komplett herstellerunabhängig. Die Speicherung von Prozessdaten erfolgt temporär in der Edge-Komponente, zum Beispiel für ihre Visualisierung in Echtzeit. Prozessdaten, die für das Reporting relevant sind, werden aufbereitet und in der Cloud für Analysezwecke abgelegt.
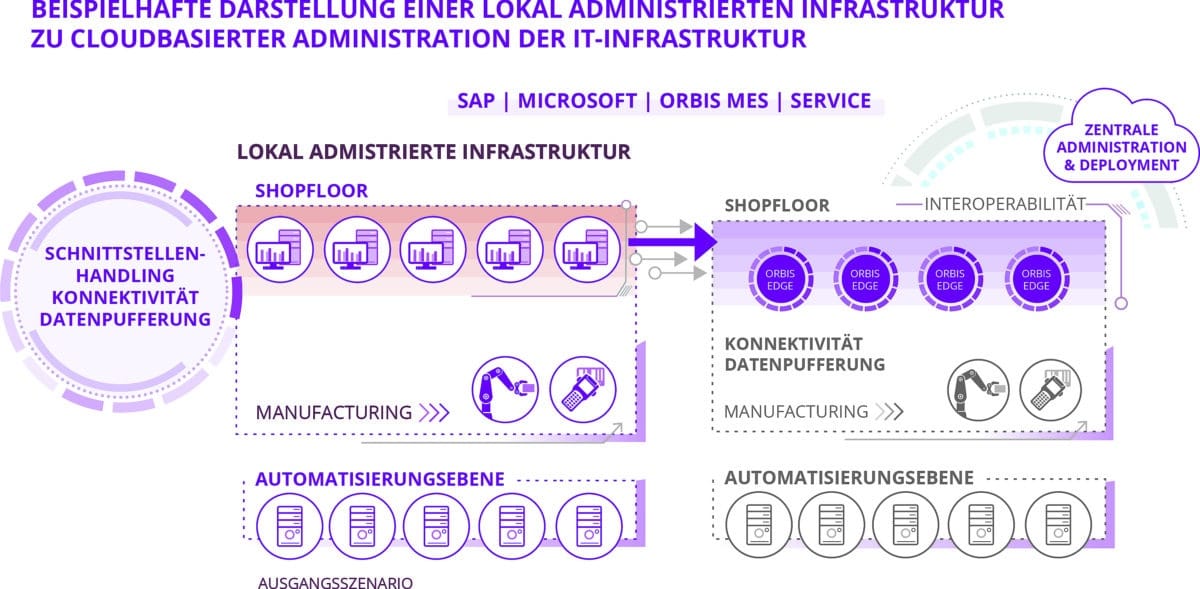
SaaS-Cloud-basiertes Management Cockpit
Das Management-Cockpit dient dazu, die Shopfloor-Organisation (Werke, Hallen, Fertigungslinien/-inseln), die Prozessobjekte (von 1 bis n) und die beteiligten Back-End-Systeme administrativ abzubilden sowie die Organisation und die Prozesse zu modellieren und zu verwalten. Daten werden dort nicht gespeichert.
Im Management-Cockpit wird bspw. festgelegt, welche der an der EDGE erfassten Maschinendaten in welches Back-End (ERP, MES, Cloud-IoT-Plattform, Low-Code-App) zu übertragen sind und, im Gegenzug, welche Daten aus den übergeordneten Applikationen (MES, IoT-Plattform etc.) in die EDGE-Lösung einfließen. Des Weiteren werden im Cockpit die Rollen und Berechtigungen verwaltet.
EDGE und Cloud-Cockpit im Zusammenspiel
Das Zusammenspiel der beiden Komponenten funktioniert wie folgt: Die Edge-Lösung erfasst Daten, die die Maschinensteuerungen in unterschiedlichen Protokollen bereitstellen, speichert sie und überträgt sie gemäß den im Management-Cockpit definierten Regeln in die angeschlossenen Back-End-Systeme. Im Gegenzug übermittelt sie die für die Produktion relevanten Informationen aus den freigegebenen Fertigungsaufträgen, die aus einem ERP beziehungsweise MES stammen, an die Maschinen.
Um teuren (Cloud-)Speicherplatz zu sparen, empfiehlt es sich, die Maschinendaten in der Edge-Komponente oder mithilfe intelligenter Sensoren (Sensor Intelligence Devices, SID) bereits auf der Hardwareebene zu prozessrelevanten Informationen (= Materialkennwerte) zu verdichten. Das reduziert den Datenstrom, der in Orbis DSP und übergeordnete IT-Systeme übertragen wird, deutlich.
Im Management Cockpit werden sämtliche Edge-Nodes, unabhängig davon, in welchen oder wie vielen Werken sie installiert sind (1 bis n), zentral und einheitlich konfiguriert und verwaltet. Bei Bedarf können weitere Werke, Komponenten und Back-End-Systeme hinzugefügt werden. Diese Flexibilität ermöglicht den Aufbau einer modernen Shopfloor-Plattform, in der alle Lösungen, egal ob von SAP, Microsoft oder einem anderen Hersteller, reibungslos in Echtzeit interagieren und die sich jederzeit erweitern lässt – ein weiterer großer Pluspunkt.
Die Vorteile in der Praxis
Herzstück einer IT-Systemlandschaft ist naturgemäß das ERP-System, etwa S/4 oder ECC. Für die Produktions- und Logistikprozesse werden diese durch ORBIS MES komplettiert. Für die Kommunikation mit einer Maschine werden Daten aus diesen Systemen, aber auch maschinenspezifische Parameter benötigt. Das können etwa Zustandsdaten eines
Betriebsmittels sein, wie der Energieverbrauch (z. B. zur Ermittlung eines CO2-Fußabdrucks) des Elektromotors einer Papiermaschine und die Durchflussgeschwindigkeit bei einer Spritzgießmaschine, aber auch Parameter wie der für den Start einer Maschine benötigte Druck und die notwendige Anlauftemperatur.
Diese Informationen müssen nicht zwingend im ERP- oder im MES-System gespeichert werden. Nach der Devise „Keep the core clean“ empfiehlt es sich stattdessen, die Datensätze und Parameter in einer eigenen Cloud-App zu speichern und zu pflegen. Dort erfolgt auch die Freigabe der Parameter zur Steuerung des Prozesses, zum Beispiel die der Startbedingungen für eine Maschine, sofern die dafür festgelegten Werte eingehalten sind. Eine solche App lässt sich mithilfe einer Low-Code-Plattform wie SAP Build oder der Microsoft-Power-Plattform zügig erstellen und trägt dazu bei, die Speicherkapazitäten im ERP zu entlasten.
Orbis DSP stellt die Interoperabilität zwischen den technischen Daten, Prozessen auf Produktionsebene, der Cloud-App beziehungsweise einer IoT-Plattform und „klassischen“ Business-Systemen wie Orbis MES und S/4 oder auch ECC 6.0 her. Die Edge-Komponente stößt dabei den Rüstvorgang an der Maschine an und meldet das Rüstende sofort an das MES zurück, das daraufhin die Produktion startet. Die Konfiguration und die Administration der einzelnen Werke und dort installierter Anlagen sowie der Daten- und Prozessflüsse erfolgen zentral im cloudbasierten Management-Cockpit.
15 Prozent mehr Produktivität in der Fertigung durch IoT-Analysen
Die an der Edge erfassten Rüstzeiten können darüber hinaus in die IoT-Plattform eingespielt und dort genau wie Stand-, Betriebs- und Produktionszeiten, geplante und ungeplante Stillstände oder Energieverbrauchsdaten ausgewertet werden. Diese Analysen liefern wichtige Hinweise auf Optimierungspotenzial in der Fertigung – ein geschäftskritischer Faktor. Anhand der Prozessdaten, die die Betriebszustände anzeigen, lassen sich außerdem Verfügbarkeit, Durchsatz und Zuverlässigkeit einer Anlage berechnen, was wichtige Indikatoren für die Maschineneffizienz sind.
Wegen ihrer enormen Skalierbarkeit bieten sich für solch datenintensive Prozesse und Analysen SaaS-Cloud-basierte Lösungen an. Prozessdaten aus Orbis DSP können zum Beispiel in der Azure-IoT-Platform gespeichert und mit der Analyselösung Microsoft Power BI ausgewertet werden oder die Datenspeicherung erfolgt in der SAP-Hana-Cloud-Datenbank (Bestandteil von SAP BTP) und für die Auswertung wird SAP Analytics Cloud (SAC) verwendet. Die Ergebnisse daraus liefern eine verlässliche Entscheidungsgrundlage, auf der sich gezielte Verbesserungsmaßnahmen für die Produktion ableiten lassen, zum Beispiel eine Reduzierung des Energieverbrauchs oder Möglichkeiten für eine Steigerung der Fertigungsproduktivität.
In einem konkreten Fall fand ein Hersteller von Zerspanungswerkzeugen durch die Analyse der Maschinendaten aus dem Herstellungsprozess heraus, dass eine Änderung der produktionsrelevanten Parameter eine Produktivitätssteigerung um 15 Prozent ermöglicht. Mithilfe solcher Analysen lassen sich aber auch ineffiziente Energieverbraucher wie ein Elektromotor, dessen Leistung sich in einem bestimmten Zeitraum bei gleichem Stromverbrauch stetig verringert, frühzeitig identifizieren und im Sinne von Predictive Maintenance rechtzeitig instand setzen. Das verhindert teure Ausfälle und Stillstandszeiten.
Fazit und Ausblick
Mit der Lösung Orbis Distributed Shopfloor Processing (DSP) gibt Orbis eine Antwort auf die zukünftigen Herausforderungen in Bezug auf die Interoperabilität in dezentralisierten IT-Landschaften im Shopfloor. In diesem Zusammenhang richtet sich der international agierende IT-Dienstleister strategisch und organisatorisch neu aus und bündelt sein Know-how in den Bereichen (Intra-)Logistik und Produktion in dem neu geschaffenen Geschäftsbereich „Manufacturing & Logistics“, um diesem Betätigungsfeld noch mehr Gewicht zu verleihen.Selbstredend wird DSP im Rahmen der festgelegten Produkt-Roadmap laufend verbessert und zielgerichtet weiterentwickelt.
Um den zukünftigen Anforderungen im IoT-Umfeld gerecht zu werden, wird die Lösung um eine systemübergreifende Prozessmodellierung auf Basis des BPMN-Standards (Business Process Model and Notation) erweitert, mit einem dezentralen, modellbasierten Logik-Layer als integralem Bestandteil. Das wird ein zentraler Punkt für die beiden kommenden Releases sein. Ein weiterer Kernaspekt ist die Mitarbeit an verschiedenen Forschungsprojekten zum Thema Nachhaltigkeit, um mit Hilfe von Orbis DSP einen Mehrwert bei der Entwicklung spezieller Sustainability-Lösungen zu schaffen, mit denen sich zum Beispiel der CO2-Fußabdruck ermitteln lässt. Darüber hinaus werden neue DSP-Anwendungen für die Prozessdatenerfassung und Parametersatzpflege entstehen.
Selbstredend wird auch die Integration in Cloud-Anwendungen aller Art laufend optimiert und erweitert, zum Beispiel in Richtung SAP BTP oder SAP Digital Manufacturing (DM). Vor dem Hintergrund der tiefen Integration von MES und DSP in die Prozesse von S/4-Hana-Cloud sind die Kunden bestens für die Zukunft aufgestellt. Darüber hinaus kann sich Orbis zukünftig auch als Anbieter SaaS-basierter IT-Architekturen positionieren; ein erster Schritt ist mit dem SaaS-Betrieb des Management-Cockpits in der Azure Cloud in den Rechenzentren der Orbis-Tochter Blue Stec bereits getan. Das Managed-Services-Angebot von Blue Stec gewährleistet zudem die Hochverfügbarkeit der Lösung inklusive eines optionalen 24/7-Supports.
