La reconversión digital como base para una integración exitosa en el taller
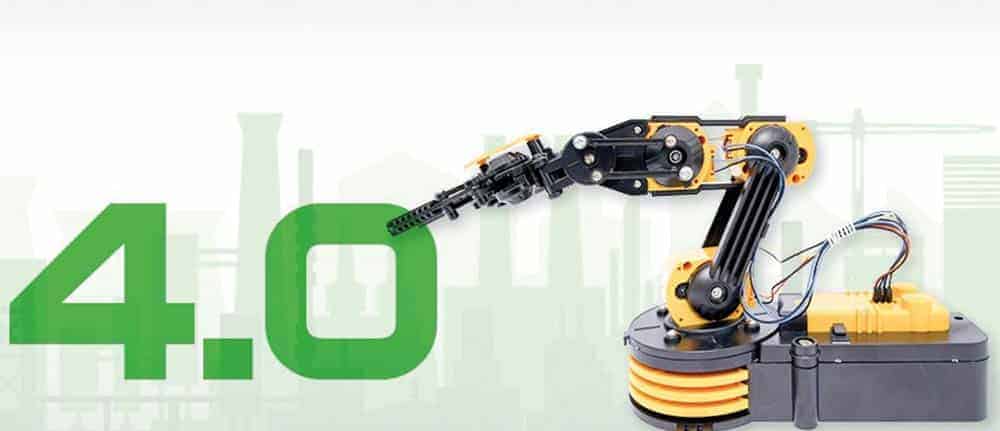
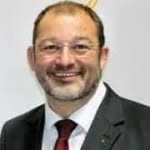
Los objetivos de la empresa son claros. La producción flexible y transparente, la determinación automatizada de las cifras clave de OEE, los procesos de mantenimiento orientados a las condiciones, como el mantenimiento predictivo, la notificación en tiempo real de cifras importantes de producción y calidad o la realimentación en tiempo real de los datos actuales de las órdenes de producción en sistemas de nivel superior (por ejemplo, SAP) permiten a la empresa reaccionar con rapidez y flexibilidad a los cambios y mantenerse en pie frente a sus competidores en el mercado. Hasta aquí la teoría.
Estas soluciones de Industria 4.0 son posibles gracias a la integración integral de la planta, en la que los valores y datos del proceso pueden leerse directamente desde los controles de la máquina o los dispositivos IoT a través de las interfaces existentes.
Pero, ¿qué aspecto tiene en la práctica? Una imagen bastante común de una empresa mediana se caracteriza por un panorama heterogéneo de máquinas.
En las naves de producción conviven máquinas de fabricantes muy diversos y de distintas edades. Para las aproximadamente 40.000 empresas del sector manufacturero en Alemania, la vida media de las máquinas es de unos 20 años.
Y una gran parte de estas máquinas no están preparadas para la Industria 4.0. Mientras que las máquinas modernas suelen disponer ya de funciones y sensores para registrar las señales relevantes de la máquina, no suele ser el caso de las máquinas antiguas o existentes.
Además, existen diferencias en la vida útil de los componentes de hardware y software de las instalaciones. Por ejemplo, los mecánicos suelen estar diseñados para una larga vida útil de muchos años, mientras que las soluciones informáticas y de software se quedan obsoletas rápidamente y normalmente pueden tener varias actualizaciones durante la vida útil de un sistema.
Según un estudio del KfW, las PYME en particular suelen mostrarse reacias a la digitalización porque les preocupa tener que adquirir maquinaria moderna y cara y por los elevados costes de inversión asociados.
No siempre tiene por qué ser una nueva adquisición. Con una reconversión digital, las plantas existentes pueden reequiparse con nuevos sensores y tecnología de comunicación de forma rentable y orientada a las tareas, y adaptarse así a las aplicaciones de la Industria 4.0. No es absolutamente necesaria una conversión completa de las plantas de producción.
En función de la tarea, basta con saber qué aspectos del proceso de producción deben supervisarse y controlarse digitalmente. A continuación, se trata de conectar en red los objetos en cuestión. Esto suele hacerse mediante el uso de las denominadas pasarelas IoT.
Con la ayuda de las pasarelas IoT y las correspondientes tecnologías marco, los datos de una amplia gama de sistemas y fabricantes pueden combinarse y conectarse a sistemas informáticos de nivel superior.
Los datos pueden leerse desde controladores como Siemens, Beckhoff, Rockwell o WAGO a través de OPC-UA, Modbus o una de las otras interfaces habituales como CANopen o RS232.
Ya sobre el terreno, una gran cantidad de los datos registrados pueden filtrarse y almacenarse temporalmente para poder acceder a los datos completos en cualquier momento, pero la transmisión de datos no se ve lastrada por una transferencia de datos innecesariamente elevada.
En combinación con la información procedente de sistemas informáticos de nivel superior, como SAP ERP, SAP MES, PLM externos u otros sistemas de terceros, resulta bastante sencillo recopilar información para controlar la producción, automatizar la información de retorno, visualizar en tiempo real la información sobre producción y calidad en el taller y crear así un verdadero valor añadido para la empresa.
Así pues, señor Meier (o como quiera que se llame), su tarea está clara. Empiece por la base.