Optimized beer runs with SAP
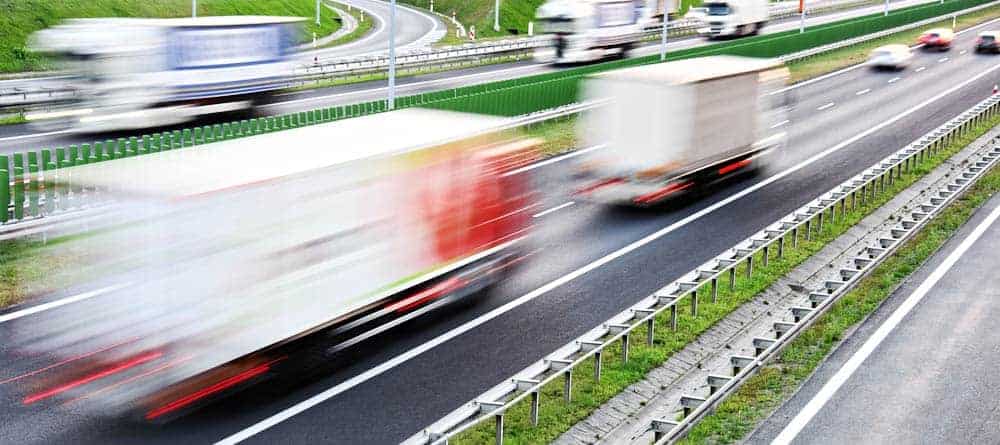
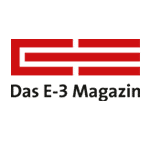
With the high number of trucks entering and leaving the various Holsten Brewery plants every day, the task was to maintain an overview of the status and location of the vehicles while at the same time controlling and monitoring the vehicle movements in a targeted manner.
Since 2004, the brewery has been a subsidiary of the international Carlsberg Group, the fourth largest brewery group in the world. The coordination effort for the processes in logistics was enormous and also explained the high administrative costs.
Added to this were long order lead times and the associated increased delivery times from the customer's point of view. Holsten's goal was to sustainably reduce logistics costs and optimize logistics processes, especially the control and monitoring of vehicle movements at the various locations.
An SAP yard control system solution from Serkem provides the beverage manufacturer with an overview of vehicle movements at multiple locations.
The forklift guidance system registers all trucks entering and leaving the respective brewery premises and displays in SAP all means of transport that are in the yard.
It is possible to display all transports to the selected location depending on status, date, transshipment point, etc. The solution also has other functions that help the brewery to shorten throughput times and reduce costs. In addition, the solution has other functions that help the brewery to shorten throughput times and reduce costs.
The time window of 15 minutes for loading and unloading the truck is adhered to without any problems. Tours can be planned in advance via an appointment reservation and times relevant for control can be calculated.
Loading lists can be sent to the carrier by mail in advance. The planning of the vehicles is simplified both on the part of the brewery and on the part of the forwarders.
When the vehicles enter the premises, the entry and exit weights for each vehicle are recorded via a connected electronic scale and stored in the system. A traffic light display in SAP shows at a glance whether, for example, limit values have been reached or exceeded. This significantly increases process reliability and reduces sources of error.
In addition, a loading lane can be assigned to each vehicle in SAP, including the creation of transport orders. In combination with the connected beeper SAPphone, the correct loading lane is then displayed to the respective driver on the beeper.
The assignment of the lane in SAP starts the actions: The trucks are notified via the beeper and a transport order is automatically generated in the forklift control system. For this purpose, only a tour and beeper number is entered in the SAP system for each means of transport.
To further reduce throughput times, a cross-docking concept is being implemented in the project: When containers are picked up at the filling lines, a check is made to see whether the transport order can be diverted to a delivery. If this is the case, the forklift truck is automatically guided to the appropriate lane.
The forklift control system warehouse control station developed by Serkem was adapted to the brewery's processes. With the help of the warehouse control station, rebookings and stock transfers can be carried out quickly and easily. In addition, critical transport orders are specially marked in terms of time and priority.
Evaluations and statistics enable Holsten to continuously monitor processes and identify possible optimization potential. For this purpose, on the one hand the total distances covered per industrial truck as well as the performance rendered per user and truck are determined, various time differences are calculated and the possibility is created to indicate the reason for excessively long waiting times.
Holsten benefited from the implemented yard management system primarily through a sustainable reduction in logistics costs. Performance was increased and the investment paid for itself within a very short time.
At the same time, order throughput times have been significantly reduced and empty runs avoided. At Holsten, the forklift trucks are now routed through the plant premises in a route-optimized manner, depending on process and order priorities.
All processes are mapped in real time in the SAP system and the establishment of an alert system for critical processes provides additional transparency and security.