New workshop handling in Tradesprint
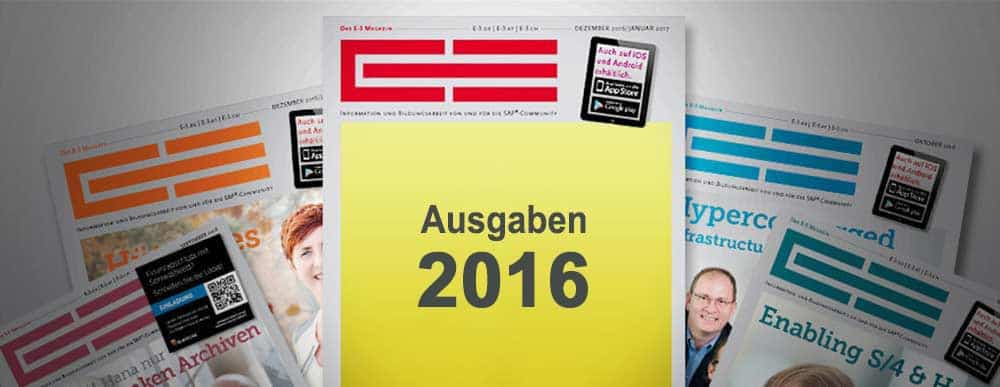
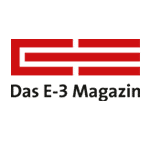
In the ERP industry software, workshop orders can now be managed and controlled even more transparently. A brand new feature is assembly planning in the workshop via app and a cash register function with TeleCash connection.
In addition, Cormeta supports omnichannel sales in tire retailing with mobile solutions and cloud applications. Another new feature is the assembly plan with the SAP Fiori app. This allows tire data to be recorded offline in the workshop, for example, and transferred directly to Tradesprint.
Tire industry under pressure
"The tire industry is under severe pressure"
knows Holger Behrens, CEO of Cormeta.
"Customers order directly from their dealer, but also via the web store or portals. The challenge for tire retailers is: How can I prepare my organization today for the digital transformation of tomorrow?"
says the Cormeta board member. Rigid, one-dimensional ERP and CRM solutions are no longer sufficient by far to be successful in the future.
"We support our customers on this path with solutions to be able to map the processes multidimensionally across all channels."
The focus is on the SAP Business All-in-One industry solution Tradesprint for all forms of modern tire retailing. All data from all front-end applications on tablets and laptops converge in the ERP (backend), regardless of whether from the mobile capture app, from the cloud or B2B platforms.
Usability in the workshop
The main focus of the revised workshop processing is on user-friendliness (usability). All data and information for a workshop order are now clearly available.
The orders can be created and controlled centrally. An information screen provides information on the storage/retrieval of tires/rims, on TPMS, on cost estimates with status management, warranty processing for vehicles and equipment, and much more.
Materials management in Tradesprint ensures that the materials for the repair are provided in the warehouse; parts/materials that are not required are automatically posted back. This means that the stock is always up to date.
Administration in the office is supported by industry-specific functions. To avoid data entry errors, many processes are automated. One example: All relevant data on a vehicle is uploaded via the KBA number and the vehicle master is created automatically.
This saves considerable time and avoids errors when creating master data. Or upcoming maintenance dates are evaluated at the push of a button and printed out via the serial letter function.
The workshop invoices can be freely designed customer-specifically and individually with just a few mouse clicks. An enormous advantage is the invoice simulation. This means that invoices can first be simulated and - only when everything is correct - printed.
"With workshop processing in a clear cockpit, Tradesprint supports the complete business processes in the automotive parts and tire trade. From administration to materials management to workshop orders, everything is mapped in the ERP software."
explains Holger Behrens.
Assembly plan via app
Since PCs are not available for data collection in every workshop and tire assembly, mobile devices have great potential here. Cormeta meets this need and provides an assembly planning app under SAP Fiori.
The workshop gets the installation plan displayed in the app, e.g. on the mobile device, complete with all workshop orders, appointments and fitters. The workshop foreman can assign new appointments for his fitters directly in the app and the tire fitter can jump straight to his workshop order. During tire fitting, he records the tire data offline; back in the office, it is automatically transferred to Tradesprint.